CDB150X-01-Z Cirrus Logic Inc, CDB150X-01-Z Datasheet - Page 10
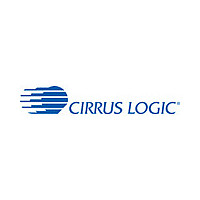
CDB150X-01-Z
Manufacturer Part Number
CDB150X-01-Z
Description
High-efficiency PFC Demo. Board
Manufacturer
Cirrus Logic Inc
Series
-r
Datasheets
1.CDB150X-01-Z.pdf
(16 pages)
2.CDB150X-01-Z.pdf
(16 pages)
3.CDB150X-01-Z.pdf
(16 pages)
4.CDB150X-01-Z.pdf
(2 pages)
Specifications of CDB150X-01-Z
Silicon Manufacturer
Cirrus Logic
Kit Application Type
Power Management
Application Sub Type
Power Factor Correction (PFC)
Kit Contents
Board, Datasheet
Design Resources
CS150x/160x PCB Layout Guidelines Boost Inductance vs. Inductor Size
Featured Product
CS1501/CS1601 Power Factor Correction IC Controllers
Main Purpose
Power Management, Power Factor Correction
Embedded
No
Utilized Ic / Part
CS1501
Primary Attributes
400V, 90W output
Secondary Attributes
90 ~ 265 VAC universal input
Lead Free Status / Rohs Status
Lead free / RoHS Compliant
5.3 Burst Mode
Burst mode is utilized to improve system efficiency when the
system output power (P
implemented by intermittently disabling the PFC over a full
half-line period under light-load conditions, as shown in
Figure 15.
5.4 Output Power and PFC Boost Inductor
In normal operating mode, the nominal output power is
estimated by the following equation.
where:
P
V
V
f
L
<1
Equation 1 is provided for explanation purposes only. Using
substituted required design values for V
following equation:
Changing the value for the V
10
max
B
o
in(min)
link
[V]
V
P
[W]
P
o
P
in
o
o
=
=
by the PFC algorithm)
against boost inductor tolerances.
rated output power of the system
efficiency of the boost converter (estimated as 100%
minimum RMS line voltage is 90V, measured after
the rectifier and EMI filter
nominal PFC output voltage (must be 400V)
maximum switching frequency is 70kHz
boost inductor specified by rated power requirement
margin factor to guarantee rated output power (P
V
90V
Figure 15. Burst Mode
in min
V
in
Burst Threshold
2
o
) is <5% of nominal. Burst mode is
2
------------------------------------------------------------ -
2
Burst Mode
link
400V
Disable
V
-------------------------------------------------------- -
2 f
70kHz
PFC
link
Active
voltage is not recommended.
–
max
–
V
90V
in min
link
L
L
B
B
and f
400V
V
2
link
max
t [ms]
t [ms]
2
FET
V
gs
gives the
[Eq.1]
[Eq.2]
o
)
Solving Equation 2 for the PFC boost inductor, L
following equation:
If a value of the boost inductor other than that obtained from
Equation 3 above is used, the total output power capability as
well as the minimum input voltage threshold will differ
according to Equation 2. Note that if the input voltage drops
below 90Vrms and the inductance value is <L
voltage V
5.5 PFC Output Capacitor
The value of the PFC output capacitor should be chosen
based upon voltage ripple and hold-up requirements. To
ensure system stability with the digital controller, the
recommended value of the capacitor is within the range of
0.5F/watt to 2.0F/watt with a V
5.6 Output IFB Sense & Input IAC Sense
A current proportional to the PFC output voltage, V
supplied to the IC on pin IFB and is used as a feedback control
signal. This current is compared against an internal
fixed-value reference current.
The ADC is used to measure the magnitude of the I
through resistor R
compared to an internal reference current (I
Figure 16. Relative Effects of Varying Boost Inductance
L
B
=
link
I
FB
will drop below 400V and fall out of regulation.
Figure 17. IFB Input Pin Model
90V
IFB
90
R5
R6
. The magnitude of the I
2
R
IFB
V
IFB
------------------------------------------------------------ -
2
AC(rms)
400V
1
70kHz P
L < L
L > L
L = L
link
–
8
15k
V
V DD
90V
B
24k
B
voltage of 400V.
link
B
o
ref
400V
IFB
CS1501
2
) of 129A.
ADC
265
current is then
DS927PP6
B
B
, gives the
IFB
I
, the link
ref
current
[Eq.3]
link
, is