3616 Loctite, 3616 Datasheet - Page 2
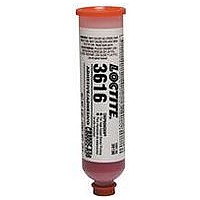
3616
Manufacturer Part Number
3616
Description
EPOXY ADHESIVE, STENCIL PRINT 300ML
Manufacturer
Loctite
Datasheet
1.3616.pdf
(3 pages)
Specifications of 3616
Adhesive Type
Epoxy
Color
Red
Dispensing Method
Stencil Print
Volume
300ml
Chemical Solution
Epoxy
For Use With
Open Squeege & Enclosed Head Stencil Printing Systems
Lead Free Status / RoHS Status
Lead free / RoHS Compliant
Available stocks
Company
Part Number
Manufacturer
Quantity
Price
TYPICAL ENVIRONMENTAL RESISTANCE
Hot Strength
Tested at temperature
Chemical/Solvent Resistance
Aged under conditions indicated and tested @ 22 °C.
Resistance to Hot Solder Dip
GENERAL INFORMATION
For safe handling information on this product, consult the
Material Safety Data Sheet (MSDS).
Directions for use
Henkel Americas
+949.789.2500
Environment
Air
98% RH
Cured for 30 minutes @ 150 °C
Cured for 90 seconds @ 150 °C
1. 3616™ is suitable for all common open squeegee and
2. After storage in a refrigerator the adhesive must be
3. Printing conditions should be about 25°C, and RH less
Lap Shear Strength, ISO 4587:
Hot Solder Dip, IPC SM817, TM-650 Method 2.4.42.1, Pass/Fail:
Steel (grit blasted)
R-1206 on bare FR4 board:
enclosed head stencil printing systems, such as ProFlow
, PumpPrint
are suitable for print speeds of 20 mm/s up to 150 mm/s -
this will vary with product selected and printer set-up.
allowed to equilibrate to room temperature before use,
typically 2 to 4 hours.
than 70 % for optimum results. Higher temperatures will
decrease the viscosity and will effect the printing results.
Higher humidity conditions may lead to moisture pick up
and will reduce the "on stencil" life of the product: At
25°C, 55 % RH, the product will remain dispensable on
the stencil for a maximum of 5 days of continuous
operation. The quality of the print results will depend on
board support, print gap, print speed, print pressure and
separation speed.
100
Supported 60 seconds above solder
bath @ 260°C and dipped for 10
seconds
75
50
25
0
For the most direct access to local sales and technical support visit: www.henkel.com/electronics
-50
®
, Varidot™. Loctite stencil print Chipbonders
0
°C
22
40
100 h
100
90
50
% of initial strength
500 h
85
80
100
Pass
1000 h
85
80
+44.1442.278.000
Henkel Europe
150
®
Loctite Material Specification
LMS dated January-14, 2002. Test reports for each batch are
available for the indicated properties. LMS test reports include
selected QC test parameters considered appropriate to
specifications for customer use. Additionally, comprehensive
controls are in place to assure product quality and
consistency. Special customer specification requirements may
be coordinated through Henkel Quality.
Storage
Store product in the unopened container in a dry location.
Storage information may be indicated on the product container
labeling.
Optimal Storage: 2 °C to 8 °C. Storage below 2 °C or
greater than 8 °C can adversely affect product properties.
Material removed from containers may be contaminated during
use. Do not return product to the original container. Henkel
Corporation cannot assume responsibility for product which
has been contaminated or stored under conditions other than
those previously indicated. If additional information is required,
please contact your local Technical Service Center or
Customer Service Representative.
Conversions
(°C x 1.8) + 32 = °F
kV/mm x 25.4 = V/mil
mm / 25.4 = inches
µm / 25.4 = mil
N x 0.225 = lb
N/mm x 5.71 = lb/in
N/mm² x 145 = psi
MPa x 145 = psi
N·m x 8.851 = lb·in
N·m x 0.738 = lb·ft
N·mm x 0.142 = oz·in
mPa·s = cP
4. Typical starting parameters (steel stencil/ steel squeegee/
5. Uncured adhesive should only be cleaned from the board
6. Cured adhesive can only be removed mechanically with
single stroke mode*):
*For higher dots Print and Flood Mode can be used. Set
up pressure for front squeegee as described above. For
flood printing, rear squeegee pressure should be set to 0
stencil. These parameters will vary depending on type of
printing process and should be optimized accordingly.
with isopropanol, MEK or ester blends such as LOCTITE
adhesive and may lead to blocked apertures if left on the
stencil for over 5 minutes. Automatic under-stencil-wipe is
not recommended.
the aid of heat.
Print Speed
Squeegee Pressure
Separation Speed
Gap between Stencil and PCB On contact
kg to leave a sufficient adhesive layer (1 to 2 mm) on the
7360™.
Alcohols (e.g. Isopropanol) can cure the
LMS
60 mm/s
3 to 4 N/cm (just enough to
clean the stencil)
0.1 to 3 mm/s
TDS 3616™, March-2008
Henkel Asia Pacific
+86.21.2891.8000
®