ADNS-2620 Avago Technologies US Inc., ADNS-2620 Datasheet - Page 4
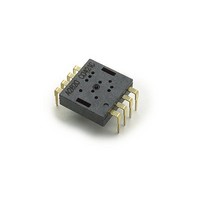
ADNS-2620
Manufacturer Part Number
ADNS-2620
Description
Optical Mouse Sensor,DIP
Manufacturer
Avago Technologies US Inc.
Datasheet
1.ADNK-2620.pdf
(27 pages)
Specifications of ADNS-2620
Lead Free Status / RoHS Status
Lead free / RoHS Compliant
Lead Free Status / RoHS Status
Lead free / RoHS Compliant, Lead free / RoHS Compliant
Other names
516-2238-5
ADNS-2620
Q2073278A
ADNS-2620
Q2073278A
PCB Assembly Considerations
1. Insert the sensor and all other electrical components
2. Bend the LED leads 90° and then insert the LED into
3. Insert the LED/clip assembly into PCB.
4. Wave solder the entire assembly in a no-wash solder
5. Place the lens onto the base plate.
6. Remove the protective kapton tape from optical
7. Insert PCB assembly over the lens onto the base plate
8. The optical position reference for the PCB is set by the
9. Install mouse top case. There MUST be a feature in
Surface
Figure 7. Sectional view of PCB assembly highlighting optical mouse components (optical mouse sensor, clip, lens, LED, PCB and base plate).
Base Plate
into PCB. Note: Pin 1 of the sensor should always be
the reference point of mechanical cutouts.
the assembly clip until the snap feature locks the LED
base.
process utilizing solder fixture. The solder fixture
is needed to protect the sensor during the solder
process. The fixture should be designed to expose
the sensor leads to solder while shielding the optical
aperture from direct solder contact. The solder fixture
is also used to set the reference height of the sensor
to the PCB top during wave soldering (Note: DO NOT
remove the kapton tape during wave soldering).
aperture of the sensor. Care must be taken to keep
contaminants from entering the aperture. It is recom-
mended not to place the PCB facing up during the
entire mouse assembly process. The PCB should be
held vertically for the kapton removal process.
aligning post to retain PCB assembly. The sensor ap-
erture ring should self-align to the lens.
base plate and lens. Note that the PCB motion due to
button presses must be minimized to maintain optical
alignment.
the top case to press down onto the clip to ensure
all components are interlocked to the correct vertical
height.
Lens/Light Pipe
PCB
Sensor
Design Considerations for Improving ESD Performance
The flange on the lens has been designed to increase
the creepage and clearance distance for electrostatic
discharge. The table below shows typical values assum-
ing base plate construction per the Avago supplied IGES
file and HDNS-2100 lens flange.
Typical Distance
Creepage
Clearance
For improved ESD performance, the lens flange can be
sealed (i.e. glued) to the base plate. Note that the lens
material is polycarbonate and therefore, cyanoacrylate
based adhesives or other adhesives that may damage the
lens should NOT be used.
Clip
LED
Millimeters
16.0
2.1