AD9224-EB Analog Devices Inc, AD9224-EB Datasheet - Page 21
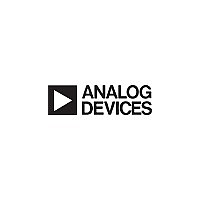
AD9224-EB
Manufacturer Part Number
AD9224-EB
Description
BOARD EVAL FOR AD9224
Manufacturer
Analog Devices Inc
Datasheet
1.AD9224ARSZRL.pdf
(24 pages)
Specifications of AD9224-EB
Rohs Status
RoHS non-compliant
Number Of Adc's
1
Number Of Bits
12
Sampling Rate (per Second)
40M
Data Interface
Parallel
Inputs Per Adc
1 Differential
Input Range
4 Vpp
Power (typ) @ Conditions
425mW @ 40MSPS
Voltage Supply Source
Single Supply
Operating Temperature
-40°C ~ 85°C
Utilized Ic / Part
AD9224
Lead Free Status / Rohs Status
Not Compliant
GROUNDING AND DECOUPLING
Analog and Digital Grounding
Proper grounding is essential in any high speed, high resolution
system. Multilayer printed circuit boards (PCBs) are recom-
mended to provide optimal grounding and power schemes. The
use of ground and power planes offers distinct advantages:
1. The minimization of the loop area encompassed by a signal
2. The minimization of the impedance associated with ground
3. The inherent distributed capacitor formed by the power
These characteristics result in both a reduction of electromag-
netic interference (EMI) and an overall improvement in
performance.
It is important to design a layout that prevents noise from cou-
pling onto the input signal. Digital signals should not be run in
parallel with input signal traces and should be routed away from
the input circuitry. While the AD9224 features separate analog
and driver ground pins, it should be treated as an analog com-
ponent. The AVSS and DRVSS pins must be joined together
directly under the AD9224. A solid ground plane under the A/D
is acceptable if the power and ground return currents are care-
fully managed. Alternatively, the ground plane under the A/D
may contain serrations to steer currents in predictable directions
where cross coupling between analog and digital would other-
wise be unavoidable. The AD9224/AD9225EB ground layout,
shown in Figure 47, depicts the serrated type of arrangement.
The evaluation board is primarily built over a common ground
plane. It has a “slit” to route currents near the clock driver. Figure
40 illustrates a general scheme of ground and power implementa-
tion in and around the AD9224.
REV. A
and its return path.
and power paths.
plane, PCB insulation and ground plane.
V
IN
A
D
A
Figure 40. Ground and Power Consideration
= ANALOG
= DIGITAL
ADC
A
IC
CIRCUITS
ANALOG
AVDD
A
A
AVSS
I
A
C
C
STRAY
STRAY
A
CIRCUITS
DIGITAL
DVDD
A
B
DVSS
I
D
V
D
DIGITAL
SUPPLY
LOGIC
LOGIC
GND
ICs
D
–21–
Analog and Digital Driver Supply Decoupling
The AD9224 features separate analog and digital supply and
ground pins, helping to minimize digital corruption of sensitive
analog signals. In general, AVDD, the analog supply, should be
decoupled to AVSS, the analog common, as close to the chip as
physically possible. Figure 41 shows the recommended decou-
pling for the analog supplies; 0.1 F ceramic chip and 10 F
tantalum capacitors should provide adequately low impedance
over a wide frequency range. Note that the AVDD and AVSS
pins are colocated on the AD9224 to simplify the layout of the
decoupling capacitors and provide the shortest possible PCB
trace lengths. The AD9224/AD9225EB power plane layout,
shown in Figure 48 depicts a typical arrangement using a multi-
layer PCB.
The CML is an internal analog bias point used internally by the
AD9224. This pin must be decoupled with at least a 0.1 F
capacitor as shown in Figure 42. The dc level of CML is ap-
proximately AVDD/2. This voltage should be buffered if it is to
be used for any external biasing.
The digital activity on the AD9224 chip falls into two general
categories: correction logic, and output drivers. The internal
correction logic draws relatively small surges of current, mainly
during the clock transitions. The output drivers draw large
current impulses while the output bits are changing. The size
and duration of these currents are a function of the load on the
output bits: large capacitive loads are to be avoided. Note, the
internal correction logic of the AD9224 is referenced to AVDD
while the output drivers are referenced to DRVDD.
The decoupling shown in Figure 43, a 0.1 F ceramic chip and
10 F tantalum capacitors are appropriate for a reasonable
capacitive load on the digital outputs (typically 20 pF on each
pin). Applications involving greater digital loads should consider
increasing the digital decoupling proportionally, and/or using
external buffers/latches.
A complete decoupling scheme will also include large tantalum
or electrolytic capacitors on the PCB to reduce low frequency
ripple to negligible levels. Refer to the AD9224/AD9225EB
schematic and layouts in Figures 44-50 for more information
regarding the placement of decoupling capacitors.
Figure 41. Analog Supply Decoupling
Figure 43. Digital Supply Decoupling
10 F
10 F
Figure 42. CML Decoupling
0.1 F
0.1 F
0.1 F
CML
AVDD
DRVDD
AVSS
DRVSS
AD9224
AD9224
AD9224
AD9224