MAX115EVB16 Maxim Integrated Products, MAX115EVB16 Datasheet - Page 13
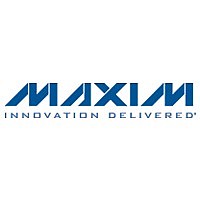
MAX115EVB16
Manufacturer Part Number
MAX115EVB16
Description
EVAL KIT FOR MAX115
Manufacturer
Maxim Integrated Products
Specifications of MAX115EVB16
Number Of Adc's
1
Number Of Bits
12
Sampling Rate (per Second)
116k
Data Interface
Parallel
Inputs Per Adc
8 Single Ended
Input Range
±5 V
Power (typ) @ Conditions
17mW @ 116kSPS
Voltage Supply Source
Analog and Digital
Operating Temperature
0°C ~ 70°C
Utilized Ic / Part
MAX115
Lead Free Status / RoHS Status
Lead free / RoHS Compliant
part of the current (torque) feedback loop. The
MAX115/MAX116 digitize the currents and deliver raw
data to the following DSP and controller stages, where
the vector processing takes place. Sensorless vector
control uses a computer model for the motor and an
algorithm to split each output current into its magnetiz-
ing (stator current) and torque-producing (rotor current)
components.
If a two-to-three phase conversion is not practical,
three currents can be sampled simultaneously with the
addition of a third sensor (not shown). Optional voltage
(position) feedback can be derived by measuring two
phase voltages (CH3A, CH4A). Typically, an isolated
differential amplifier is used between the motor and the
MAX115/MAX116. Again, the third phase voltage can
be derived from the magnitude (phase voltage) and its
relative phase.
For optimum speed control and good load regulation
close to zero speed, additional velocity and position
feedback are derived from an encoder or resolver and
brought to the MAX115/MAX116 at CH4B. The addi-
Figure 10. Vector Motor Control
SETPOINTS
EXTERNAL
______________________________________________________________________________________
CONTROLLER
DSP
µC
2x4-Channel, Simultaneous-Sampling
12
POWER
12 BIT ADC +
STAGE
SEQUENCER
MAX115
MAX116
MICRO-
MAIN DC
CH1
CH2
CH3
CH4
A
B
A
B
A
B
A
B
tional channels can be used to evaluate slower analog
inputs, such as the main DC bus voltage (CH2B), tem-
perature sensors (CH3B), or other analog inputs (AUX,
CH1B).
For optimum system performance, use printed circuit
boards with separate analog and digital ground planes.
Wire-wrapped boards are not recommended. Connect
the two ground planes together at the low-impedance
power-supply source. For the best ground connection,
connect the DGND and AGND pins together and con-
nect that point to the system analog ground plane to
avoid interference from other digital noise sources. If
DGND is connected to the system digital ground, digi-
tal noise may get through to the ADC’s analog portion.
The AGND pins must be connected directly to a low-
impedance ground plane. Extra impedance between
the pins and the ground plane increases crosstalk and
degrades INL.
MAIN DC
AUX
TEMP
and Ground Management
Power-Supply Bypassing
12-Bit ADCs
FEEDBACK
VELOCITY
MOTOR
MOTOR
AC
AC
RESOLVER/
ENCODER
R/E
13