CDB5530U Cirrus Logic Inc, CDB5530U Datasheet - Page 22
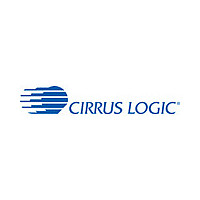
CDB5530U
Manufacturer Part Number
CDB5530U
Description
BOARD EVAL FOR CS5530
Manufacturer
Cirrus Logic Inc
Type
A/Dr
Specifications of CDB5530U
Number Of Adc's
1
Number Of Bits
24
Sampling Rate (per Second)
3.84k
Data Interface
Serial
Inputs Per Adc
1 Differential
Input Range
±2.5 V
Power (typ) @ Conditions
35mW @ 5 V
Voltage Supply Source
Analog and Digital, Dual ±
Operating Temperature
-40°C ~ 85°C
Utilized Ic / Part
CS5530
Product
Data Conversion Development Tools
Resolution
24 bit
Maximum Clock Frequency
4 MHz
Interface Type
USB
Supply Voltage (max)
5 V
Supply Voltage (min)
3.3 V
For Use With/related Products
CS5530
Lead Free Status / RoHS Status
Contains lead / RoHS non-compliant
Lead Free Status / RoHS Status
Lead free / RoHS Compliant, Contains lead / RoHS non-compliant
Other names
598-1158
2.4.4 Performing Calibrations
To perform a calibration, the user must send a com-
mand byte with its MSB=1, and the appropriate
calibration bits (CC2-CC0) set to choose the type
of calibration to be performed. The calibration will
be performed using the filter rate, and siganl span
(unipolar or bipolar) as set in the configuration reg-
ister. The length of time it takes to do a calibration
is slightly less than the amount of time it takes to do
a single conversion (see Table 1 for single conver-
sion timing). Offset calibration takes 608 clock cy-
cles less than a single conversion when FRS = 0,
and 729 clock cycles less when FRS = 1. Gain cal-
ibration takes 128 clock cycles less than a single
conversion when FRS = 0, and 153 clock cycles
less when FRS = 1.
Once a calibration cycle is complete, SDO falls and
the results are automatically stored in either the
gain or offset register. SDO will remain low until
the next command word is begun. If additional cal-
ibrations are performed while referencing the same
calibration registers, the last calibration results will
replace the effects from the previous calibration.
Only one calibration is performed with each com-
mand byte.
2.4.5 System Calibration
For the system calibration functions, the user must
supply the converter input calibration signals which
22
Figure 10. System Calibration of Offset
represent ground and full-scale. When a system off-
set calibration is performed, a ground referenced sig-
nal must be applied to the converter. Figure 10
illustrates system offset calibration.
As shown in Figure 11, the user must input a signal
representing the positive full-scale point to perform
a system gain calibration. In either case, the cali-
bration signals must be within the specified calibra-
tion limits for each specific calibration step (refer
to the System Calibration Specifications).
2.4.6 Calibration Tips
Calibration steps are performed at the output word
rate selected by the WR3-WR0 bits of the configu-
ration register. To minimize the effects of peak-to-
peak noise on the accuracy of calibration the con-
verter should be calibrated using the slowest word
rate that is acceptable. It is recommended that
word rates of 240 Sps and higher not be used for
calibration.) To minimize digital noise near the de-
vice, the user should wait for each calibration step
to be completed before reading or writing to the se-
rial port. Reading the calibration registers and aver-
aging multiple calibrations together can produce a
more accurate calibration result. Note that access-
ing the ADC’s serial port before a calibration has
finished may result in the loss of synchronization
between the microcontroller and the ADC, and may
prematurely halt the calibration cycle.
Figure 11. System Calibration of Gain
CS5530
DS742F3