NCP5318 ON Semiconductor, NCP5318 Datasheet - Page 21
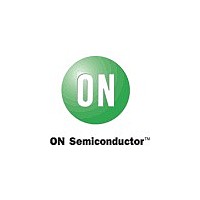
NCP5318
Manufacturer Part Number
NCP5318
Description
Two/Three/Four-Phase Buck CPU Controller
Manufacturer
ON Semiconductor
Datasheet
1.NCP5318.pdf
(31 pages)
Available stocks
Company
Part Number
Manufacturer
Quantity
Price
Company:
Part Number:
NCP5318FT
Manufacturer:
IR
Quantity:
52 000
Company:
Part Number:
NCP5318FTR2
Manufacturer:
ON Semiconductor
Quantity:
10 000
Company:
Part Number:
NCP5318FTR2G
Manufacturer:
ON Semiconductor
Quantity:
10 000
3. Output Inductor Selection
converter because it directly affects the choice of other
components and affects both the steady−state and transient
performance of the converter. When selecting an inductor,
the designer must consider factors such as DC current, peak
current, core loss, magnetic saturation, output voltage
ripple, load step and release, temperature, physical size and
cost.
electrically and physically as small as possible in order to
provide the best transient response at minimum cost. If a
large inductance value is used, the converter will not
respond quickly to rapid changes in the load current. On the
other hand, lower inductance requires more parallel ceramic
output capacitors to make the output filter ESL low enough
to avoid excessive output voltage ripple. And the higher
ripple current in the MOSFETs and input capacitors
increases dissipation and lowers converter efficiency
(especially at light loads) − possibly requiring the use of
higher rated MOSFETs, an oversized thermal solution, and
the use of more or higher current rated input capacitors,
which increases converter cost. Too high a ripple current
may saturate the inductor, further increasing ripple current
and all losses including core loss.
size the inductor to produce a specified maximum ripple
current in the inductor. Lower ripple currents will result in
less core and MOSFET losses and higher converter
efficiency. Equation 4 may be used to calculate the inductor
value to produce a given maximum ripple current (a) per
phase. The inductor value calculated by this equation is a
minimum because values less than this will produce more
ripple current than desired. Conversely, higher inductor
values will result in less than the selected maximum ripple
current.
output current per phase (a = 0.15 for ±15%, a = 0.25 for
±25%, etc.). If the minimum inductor value is used, the
inductor current will swing ± (a/2)% about its value at the
center. Therefore, for a four−phase converter, the inductor
must be designed or selected such that it will not saturate
with a peak current of (1 + a/2) ⋅ I
response required of the converter. If the converter is to have
a fast transient response, the inductor should be made as
small as will be allowed by other constraints. If the inductor
is too large, its current will change too slowly, the output
voltage will droop excessively, more bulk capacitors will be
required and the converter cost will be increased. For a given
inductor value (L
required to increase or decrease the current.
The output inductor is a very critical component in the
In general, the output inductance value should be
One method of calculating an output inductor value is to
a is the ripple current as a percentage of the maximum
The maximum inductor value is limited by the transient
Lo MIN +
O
(a
), it is useful to determine the time
(V IN * V OUT )
I O,MAX
O,MAX
V IN
V OUT
/4.
f SW )
http://onsemi.com
(eq. 4)
21
less than one quarter of the input voltage, the current can be
increased more quickly than it can be decreased. Thus, it
may be more difficult for the converter to avoid
overshooting the regulation limits when the load is removed
than when it is applied.
4. Input Capacitor Selection
ceramic types. Bulk capacitors are needed to ensure
converter stability, and can provide some buffering of the
ATX power supply from the effects of load step and release.
The ceramic capacitors are needed to provide the input
ripple current. The choice and number of ceramic input
capacitors is primarily determined by their voltage and
ripple current ratings. The designer must choose capacitors
that will support the worst case input voltage with adequate
margin. To calculate the number of input capacitors, the
converter RMS input ripple current must be calculated by
the following procedure:
where:
is ON and charge when the control FET is OFF as shown in
Figure 23.
For increasing current:
For decreasing current:
For typical processor applications with output voltages
Input capacitors must be both bulk electrolytic and
The input capacitors will discharge when the control FET
−I
I
IN,AVG
C,MAX
I
C,MIN
D is the duty cycle of the converter, D = V
h is the specified minimum efficiency;
I
Figure 23. Input Capacitor Current for a
O,MAX
0 A
Control FET On,
Input Caps Discharging
Dt INC + Lo
Dt DEC + Lo
is the maximum converter output current.
I IN,AVG + I O,MAX
Four−Phase Converter
t
ON
Control FET Off,
Input Caps
Charging
DI
C,IN
(V IN * V OUT )
(V OUT )
T/4
= I
DI O
DI O
C,MAX
D
h
− I
C,MIN
OUT
(eq. 5)
(eq. 6)
(eq. 7)
/V
IN
;