NCP5314 ON Semiconductor, NCP5314 Datasheet - Page 19
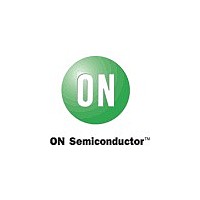
NCP5314
Manufacturer Part Number
NCP5314
Description
Two/Three/Four-Phase Buck CPU Controller
Manufacturer
ON Semiconductor
Datasheet
1.NCP5314.pdf
(28 pages)
Available stocks
Company
Part Number
Manufacturer
Quantity
Price
Part Number:
NCP5314FTR
Manufacturer:
ON/安森美
Quantity:
20 000
Company:
Part Number:
NCP5314FTR2
Manufacturer:
ON Semiconductor
Quantity:
10 000
Company:
Part Number:
NCP5314FTR2G
Manufacturer:
ON Semiconductor
Quantity:
10 000
3. Output Inductor Selection
in the converter because it will directly effect the choice of
other components and dictate both the steady−state and
transient performance of the converter. When selecting an
inductor, the designer must consider factors such as DC
current, peak current, output voltage ripple, core material,
magnetic saturation, temperature, physical size and cost
(usually the primary concern).
electrically and physically as small as possible to provide the
best transient response at minimum cost. If a large
inductance value is used, the converter will not respond
quickly to rapid changes in the load current. On the other
hand, too low an inductance value will result in very large
ripple currents in the power components (MOSFETs,
capacitors, etc.) resulting in increased dissipation and lower
converter efficiency. Increased ripple currents force the
designer to use higher rated MOSFETs, oversize the thermal
solution, and use more, higher rated input and output
capacitors, adversely affecting converter cost.
size the inductor to produce a specified maximum ripple
current in the inductor. Lower ripple currents will result in
less core and MOSFET losses and higher converter
efficiency. Equation 3 may be used to calculate the
minimum inductor value to produce a given maximum
ripple current ( ) per phase. The inductor value calculated
by this equation is a minimum because values less than this
will produce more ripple current than desired. Conversely,
higher inductor values will result in less than the selected
maximum ripple current.
output current per phase ( = 0.15 for 15%,
inductor current will swing
center. Therefore, for a four−phase converter, the inductor
must be designed or selected such that it will not saturate
with a peak current of (1 + ) I
response of the converter. If the converter is to have a fast
transient response, the inductor should be made as small as
possible. If the inductor is too large its current will change
too slowly, the output voltage will droop excessively, more
bulk capacitors will be required and the converter cost will
be increased. For a given inductor value, it is useful to
determine the times required to increase or decrease the
current.
25%, etc.). If the minimum inductor value is used, the
The output inductor may be the most critical component
In general, the output inductance value should be
One method of calculating an output inductor value is to
The maximum inductor value is limited by the transient
For increasing current:
is the ripple current as a percentage of the maximum
Lo MIN +
Dt INC + Lo @ DI O (V IN * V OUT )
(a @ I O,MAX @ V IN @ f SW )
(V IN * V OUT ) @ V OUT
O,MAX
% about its value at the
/4.
= 0.25 for
http://onsemi.com
(3.1)
(3)
NCP5314
19
less than half the input voltage, the current will be increased
much more quickly than it can be decreased. Thus, it may be
more difficult for the converter to stay within the regulation
limits when the load is removed than when it is applied and
excessive overshoot may result.
output inductor value derived in this Section (Lo
number of output capacitors (N
capacitor ESR determined in the previous Section:
V OUT,P−P + (ESR per cap
more than one phase on at any time. The second term in
Equation 4 is the total ripple current seen by the output
capacitors. The total output ripple current is the “time
summation” of the four individual phase currents that are 90
degrees out−of−phase. As the inductor current in one phase
ramps upward, current in the other phase ramps downward
and provides a canceling of currents during part of the
switching cycle. Therefore, the total output ripple current
and voltage are reduced in a multi−phase converter.
4. Input Capacitor Selection
determined by their voltage and ripple current ratings. The
designer must choose capacitors that will support the worst
case input voltage with adequate margin. To calculate the
number of input capacitors, one must first determine the
total RMS input ripple current. To this end, begin by
calculating the average input current to the converter:
where:
is ON and charge when the control FET is OFF as shown in
Figure 24.
minimum currents delivered by the input capacitors:
where is the number of phases in operation.
For decreasing current:
For typical processor applications with output voltages
The output voltage ripple can be calculated using the
This formula assumes steady−state conditions with no
The choice and number of input capacitors is primarily
D is the duty cycle of the converter, D = V
I
The input capacitors will discharge when the control FET
The following equations will determine the maximum and
I
I
O,MAX
Lo,MAX
Lo,MIN
is the specified minimum efficiency;
(V IN * #Phases @ V OUT ) @ D
is the maximum converter output current.
is the minimum output inductor current:
is the maximum output inductor current:
I C,MAX + I Lo,MAX h * I IN,AVG
I Lo,MAX + I O,MAX f ) DI Lo 2
I C,MIN + I Lo,MIN h * I IN,AVG
I Lo,MIN + I O,MAX f * DI Lo 2
Dt DEC + Lo @ DI O (V OUT )
I IN,AVG + I O,MAX @ D h
N OUT,MIN ) @
OUT,MIN
(Lo MIN @ f SW )
) and the per
OUT
/V
MIN
IN
), the
;
(3.2)
(4)
(5)
(6)
(7)
(8)
(9)