QT310-IS Atmel, QT310-IS Datasheet - Page 10
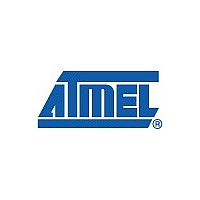
QT310-IS
Manufacturer Part Number
QT310-IS
Description
SENSOR IC TOUCH PROG 1CH 8-SOIC
Manufacturer
Atmel
Series
QProx™r
Type
Capacitiver
Datasheet
1.QT310-IS.pdf
(20 pages)
Specifications of QT310-IS
Rohs Status
RoHS non-compliant
Touch Panel Interface
1, 2-Wire
Number Of Inputs/keys
1 Key
Resolution (bits)
16 b
Data Interface
Serial
Voltage Reference
Internal
Voltage - Supply
1.8 V ~ 5 V
Current - Supply
600µA
Operating Temperature
-40°C ~ 85°C
Mounting Type
Surface Mount
Output Type
*
Interface
*
Input Type
*
Package / Case
-
Other names
427-1028
Available stocks
Company
Part Number
Manufacturer
Quantity
Price
Sense direction (SD) behavior: In both BG modes OUT can
be made active on either positive or negative Cx changes
(Section 2.8.2). SD selection affects which side of the
reference the threshold and hysteresis points are placed.
In addition, the OUT pin can be made either active low or
active high (Section 2.7.1).
2.8.4.1 BG1 Mode (volatile reference)
In BG1 mode, the reference is set via recalibration initiated
using the /CAL_CLR pin or on power-up. The resulting
reference level is not stored into EEPROM. Max On-Duration
and drift compensation are able to function normally.
BG1 mode is useful when the signal can change slightly over
time and temperature, and it is useful to track these changes
without a loss of sensitivity.
2.8.4.2 BG2 Mode (stored reference)
In BG2 mode, the reference level is fixed and stored in
internal EEPROM. Drift compensation (Section 2.2) can be
used, but changes to the reference due to drift compensation
are not updated to EEPROM. Max On-Duration can also be
enabled (Section 2.6); if a MOD timeout occurs, the new
reference will be stored in EEPROM.
The reference is normally set during recalibration when the
/CAL_CLR pin pulses low (Section 1.6); the resulting
reference value is then stored in EEPROM. At power-up the
part automatically restores this reference level and runs
without another recalibration.
The reference value can also be entered numerically via the
cloning process (Table 4-1, page 14) to precisely replicate the
calibration point across many devices.
BG2 mode is useful when it is desired to lock in the reference
to prevent changes on startup, for example to replace
mechanical switches in process controls.
LQ
Vdd
Closed Loop
Open Loop
Figure 2-3 Daisy chain wiring
Vdd
Vdd
Vdd
1
6
2
1
6
2
1
6
2
/CAL
/SYNC_I
/SYNC_O
/CAL
/SYNC_I
/SYNC_O
/CAL
/SYNC_I
/SYNC_O
SNS1
SNS2
SNS1
SNS2
SNS1
SNS2
OUT
OUT
OUT
U1
U2
Un
7
3
5
7
3
5
7
3
5
CS1
CS2
CS3
OUT1
OUT2
OUT_N
SENSOR 1
SENSOR 2
SENSOR N
10
2.8.5 OBJ (O
This mode is useful to do a ‘learn by example’ calibration.
Typically, a test object is placed at the electrode in such a
way as to create a 50% signal level change relative to a
normal, full presentation of the object. The QT310 is then
calibrated in OBJ mode. Calibration in OBJ mode should
never be done with a full presentation of signal, as this will
create a marginal, unreliable detection.
This mode is suited to material detection, fluid level sensing,
and similar applications.
In OBJ mode, on calibration the current signal value is
recorded as a fixed threshold point and stored to EEPROM.
The hysteresis level is made relative to the fixed threshold,
and can be altered as with the BG modes. If hysteresis is too
large, the sensor can ‘stick’ on; hysteresis should normally be
set to a small value, just enough to prevent output chatter.
Hysteresis can also be made intentionally large, for example
for ‘bang-bang’ fluid level sensing, where an ‘upper’ level is
calibrated using OBJ, and a ‘lower’ cut-out level is defined by
the hysteresis value. The sensor must have SD = positive for
this mode (Section 2.8.2).
OBJ mode does not make use of a reference level and does
not allow drift compensation or Max On-Duration to operate.
The threshold point is fixed for all time until another
/CAL_CLR signal is received.
The OBJ threshold value can also be entered numerically via
the cloning process (Table 4-1, page 14) to precisely replicate
the threshold point across many devices.
Positive, negative detection mode behavior: In OBJ mode
OUT can be made active on either positive or negative signal
changes (Section 2.8.2). The signal direction selection affects
which side of the threshold the hysteresis level is placed after
calibration.
The OUT pin can be made either active low or active high
(Section 2.7.1).
2.9 SYNCHRONISATION
The synchronization feature allows a QT310 to generate its
burst on demand from an external trigger rather than of its
own accord. This feature is made possible by the fact that the
QT310 operates in burst mode, rather than continuously.
Sync is a powerful feature that permits two important
operating modes: Daisy-chaining, and noise synchronization.
The SYNC_I pin is used to trigger the QT310 to generate a
burst. The sleep timer will always wake the part if a sync
pulse has not been received before the sleep time expires.
The sleep timer is always restarted when a sync pulse is
received.
The pulse applied to SYNC_I must be normally high,
negative-going, of >15µs pulse duration. SYNC_O emits a
80µs pulse at the end of each burst.
During calibration (Section 1.6) and fast integration (Section
2.5), where bursts are generated quickly a number of times in
sequence without regard to the sleep timer, a single SYNC_O
pulse is generated only after the last burst in the series of fast
spaced bursts in order to prevent downstream slave parts
from being triggered too rapidly.
BJECT
) D
ETECTION
M
ODE
QT310/R1.01 07/02