HC55185ECM Intersil, HC55185ECM Datasheet - Page 15
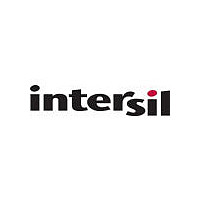
HC55185ECM
Manufacturer Part Number
HC55185ECM
Description
Manufacturer
Intersil
Datasheet
1.HC55185ECM.pdf
(20 pages)
Specifications of HC55185ECM
Number Of Channels
1
On-hook Transmission
Yes
Polarity Reversal
Yes
On-chip Ring Relay Driver
Yes
Longitudinal Balanced
64
Operating Supply Voltage (typ)
5/-18/-24/-28V
Operating Temp Range
0C to 85C
Package Type
PLCC
Loop Current Limit
45mA
Operating Temperature Classification
Commercial
Pin Count
28
Mounting
Surface Mount
Operating Current
10.3mA
Operating Supply Voltage (max)
5.25/-52V
Operating Supply Voltage (min)
4.75/-16V
Lead Free Status / RoHS Status
Not Compliant
Available stocks
Company
Part Number
Manufacturer
Quantity
Price
Part Number:
HC55185ECM
Manufacturer:
INTERSIL
Quantity:
20 000
Company:
Part Number:
HC55185ECM*
Manufacturer:
INTERSIL
Quantity:
26
Part Number:
HC55185ECM96
Manufacturer:
INTERSIL
Quantity:
20 000
Company:
Part Number:
HC55185ECMR
Manufacturer:
INTERSIL
Quantity:
12 388
Company:
Part Number:
HC55185ECMR4854
Manufacturer:
INTERSIL
Quantity:
8 831
Company:
Part Number:
HC55185ECMR4854*
Manufacturer:
MMI
Quantity:
3
Company:
Part Number:
HC55185ECMZ
Manufacturer:
INTERSIL
Quantity:
12 388
Company:
Part Number:
HC55185ECMZR4854
Manufacturer:
INTERSIL/PBF
Quantity:
7 119
Part Number:
HC55185ECMZR4854
Manufacturer:
INTERSIL
Quantity:
20 000
AC Verification
The entire AC loop of the device is active during the forward
loop back mode. Therefore a 4-wire to 4-wire level test
capability is provided. Depending on the transhybrid balance
implementation, test coverage is provided by a one or two
step process.
System architectures which cannot disable the transhybrid
function would require a two step process. The first step
would be to send a test tone to the device while on hook and
not in forward loop back mode. The return signal would be
the test level times the gain R
amplifier. Since the device would not be terminated,
cancellation would not occur. The second step would be to
program the device to FLB and resend the test tone. The
return signal would be much lower in amplitude than the first
step, indicating the device was active and the internal
termination attenuated the return signal.
System architectures which disable the transhybrid function
would achieve test coverage with a signal step. Once the
transhybrid function is disable, program the device for FLB
and send the test tone. The return signal level is determined
by the 4-wire to 4-wire gain of the device.
Tip Open
Overview
The tip open mode (110) is intended for compatibility for PBX
type interfaces. Used during idle line conditions, the device
does not provide transmission. Loop supervision is provided
by either the switch hook detector (E0 = 1) or the ground key
detector (E0 = 0). The ground key detector will be used in
most applications. The device may be operated from either
high or low battery.
Functionality
During tip open operation, the Tip switch is disabled and the
Ring switch is enabled. The minimum Tip impedance is
30kΩ. The only active path through the device will be the
Ring switch.
In keeping with the MTU characteristics of the device, Ring
will not exceed -56V when operating from the high battery.
Though MTU does not apply to tip open, safety requirements
are satisfied.
Power Denial
Overview
The power denial mode (111) will shutdown the entire device
except for the logic interface. Loop supervision is not
provided. This mode may be used as a sleep mode or to
shut down in the presence of a persistent thermal alarm.
Switching between high and low battery will have no effect
during power denial.
15
F
/R
A
of the transhybrid
HC55185
Functionality
During power denial, both the Tip and Ring amplifiers are
disabled, representing high impedances. The voltages at
both outputs are near ground.
Thermal Shutdown
In the event the safe die temperature is exceeded, the ALM
output will go low and DET will go high and the part will
automatically shutdown. When the device cools, ALM will
go high and DET will reflect the loop status. If the thermal
fault persists, ALM will go low again and the part will
shutdown. Programming power denial will permanently
shutdown the device and stop the self cooling cycling.
Battery Switching
Overview
The integrated battery switch selects between the high
battery and low battery. The battery switch is controlled
with the logic input BSEL. When BSEL is a logic high, the
high battery is selected and when a logic low, the low
battery is selected. All operating modes of the device will
operate from high or low battery except forward loop back.
Functionality
The logic control is independent of the operating mode
decode. Independent logic control provides the most
flexibility and will support all application configurations.
When changing device operating states, battery switching
should occur simultaneously with or prior to changing the
operating mode. In most cases, this will minimize overall
power dissipation and prevent glitches on the DET output.
The only external component required to support the battery
switch is a diode in series with the V
event that high battery is removed, the diode allows the
device to transition to low battery operation.
Low Battery Operation
All off hook operating conditions should use the low battery.
The prime benefit will be reduced power dissipation. The
typical low battery for the device is -24V. However this may
be increased to support longer loop lengths or high loop
current requirements. Standby conditions may also operate
from the low battery if MTU compliance is not required,
further reducing standby power dissipation.
High Battery Operation
Other than ringing, the high battery should be used for
standby conditions which must provide MTU compliance.
During standby operation the power consumption is typically
85mW with -100V battery. If ringing requirements do not
require full 100V operation, then a lower battery will result in
lower standby power.
BH
supply lead. In the
December 18, 2006
FN4831.14