IM-T-11A BANNER ENGINEERING, IM-T-11A Datasheet - Page 3
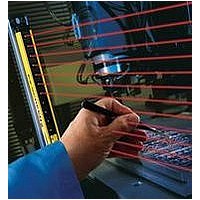
IM-T-11A
Manufacturer Part Number
IM-T-11A
Description
Interfacing Module
Manufacturer
BANNER ENGINEERING
Datasheet
1.IM-T-11A.pdf
(12 pages)
Specifications of IM-T-11A
Supply Voltage Max
24VDC
Control Output Type
2NO/1NC
Figure 3. Requirements for pulsed output
+24V dc
1. DO NOT connect E-stop switches,
2. ALWAYS connect terminals
This Module does not have the circuitry
required to perform a self-check. A single
fault inside the unit or in external devices
(like switches or E-stop buttons) can go
undetected and create an unsafe condition.
Failure to properly connect this Interface
Module to a primary safety device with
a monitoring function could result in
serious injury or death.
0V dc
2-hand control actuators/switches,
safety interlock switches, or similar
devices directly to this Interface
Module.
Y1-Y2 and Y3-Y4 of this Interface
Module to the monitoring input of the
primary safety device that controls it
(see Figures 4 through 8).
Banner Engineering Corp.
Banner Engineering Corp.
WARNING . . .
Stand-Alone Safety Module
t
t
1
2
www.bannerengineering.com • Tel: 763.544.3164
www.bannerengineering.com • Tel: 763.544.3164
> 500
signals from a primary safety
device
t
(500 µs max.)
2
Not for Use As a
t
1
•
•
Minneapolis, MN U.S.A.
Minneapolis, MN U.S.A.
Interface Modules IM-T-9A and IM-T-11A are driven by one or two safety output channels
of a primary safety device. For higher risk applications, the design of the primary safety
device must meet OSHA/ANSI control reliability requirements (U.S. applications) or ISO/IEC/
The Safety Module must be installed inside an enclosure. It is not designed for exposed wiring. It is
the user’s responsibility to house the Safety Module in an enclosure with NEMA 3 (IEC IP54) rating,
or better.
The Safety Module mounts directly to standard 35 mm DIN rail; see Dimensions.
Heat Dissipation Considerations
For reliable operation, ensure that the operating specifications are not exceeded. The enclosure
must provide adequate heat dissipation, so that the air closely surrounding the Module does not
exceed the maximum operating temperature stated in the Specifications. Methods to reduce heat
build-up include venting, forced airflow (e.g., exhaust fans), adequate enclosure exterior surface
area, and spacing between modules and other sources of heat.
EN Category 3 or 4, Performance Level d or e, and SIL 2 or 3 requirements for European
applications. IM-T-..A Modules must be used only with primary safety devices which have
External Device Monitoring capability (see Figures 4 through 8 and the Warning Interfacing
MPCEs on page 7).
At a minimum, each output channel of the primary safety device must:
• Include one normally open forced-guided (mechanically linked) contact (FSD), or
• Include one solid-state 24V dc sourcing safety output (OSSD), and
• Be self-monitored to result in a safe (OFF) condition in the event of a failure, and
• Be capable of switching 50 mA @ 24V dc ± 15%.
NOTE: A s OSSD solid-state outputs on primary safety devices very often are pulsed, it is
Final Switching Device (FSD): The component of the machine’s safety-related control system
that interrupts the circuit to the machine primary control element (MPCE) when the output
signal switching device (OSSD) goes to the OFF-state.
Output Signal Switching Device (OSSD): The component of the electro-sensitive protective
equipment (ESPE) connected to the control system of the machine which, when the sensing
device is actuated during normal operation, responds by going to the OFF-state.
possible that the relay coils will produce an audible buzzing. This relay buzzing does
not affect the function of the Interface Module, as long as the pulse width is below
500 µs (microseconds) and the duty cycle (t1/ t2) is greater than 500.
Primary Safety Device Requirements
Mechanical Installation
– Interface Modules
– Interface Modules
P/N 62822 rev. C
3