0805ZD225KAT2A AVX Corporation, 0805ZD225KAT2A Datasheet - Page 17
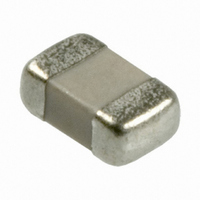
0805ZD225KAT2A
Manufacturer Part Number
0805ZD225KAT2A
Description
CAP CERM 2.2UF 10% 10V X5R 0805
Manufacturer
AVX Corporation
Series
0805r
Specifications of 0805ZD225KAT2A
Capacitance
2.2µF
Tolerance
±10%
Package / Case
0805 (2012 Metric)
Voltage - Rated
10V
Temperature Coefficient
X5R
Mounting Type
Surface Mount, MLCC
Operating Temperature
-55°C ~ 85°C
Applications
General Purpose
Size / Dimension
0.079" L x 0.049" W (2.00mm x 1.25mm)
Thickness
1.40mm Max
Voltage Rating
10 Volts
Operating Temperature Range
- 55 C to + 85 C
Temperature Coefficient / Code
X5R
Product
General Type MLCCs
Dimensions
1.25 mm W x 2.01 mm L x 1.4 mm H
Termination Style
SMD/SMT
Dielectric Characteristic
X5R
Capacitance Tolerance
± 10%
Capacitor Case Style
0805
No. Of Pins
2
Capacitor Mounting
SMD
Rohs Compliant
Yes
Brand/series
AVX
Case Size
0805
Dielectric Strength
No breakdown or visual defects
Dissipation Factor
5 %
Dissipation Factor, Test Condition
(Max.)
Insulation Resistance
500 Megohms
Length
0.079 in. ± 0.008 in.
Material, Element
Ceramic
Package Type
0805
Temperature, Operating, Maximum
85 °C
Temperature, Operating, Minimum
-55 °C
Termination
SMT
Voltage, Rating
10 VDC
Width
0.049 in. ± 0.008 in.
Lead Free Status / RoHS Status
Lead free / RoHS Compliant
Features
-
Ratings
-
Lead Spacing
-
Lead Free Status / Rohs Status
Lead free / RoHS Compliant
Other names
478-1413-2
Surface Mounting Guide
MLC Chip Capacitors
and a target figure 2°C/second is recommended. Although
an 80°C to 120°C temperature differential is preferred,
recent developments allow a temperature differential
between the component surface and the soldering temper-
ature of 150°C (Maximum) for capacitors of 1210 size and
below with a maximum thickness of 1.25mm. The user is
cautioned that the risk of thermal shock increases as chip
size or temperature differential increases.
Soldering
Mildly activated rosin fluxes are preferred. The minimum
amount of solder to give a good joint should be used.
Excessive solder can lead to damage from the stresses
caused by the difference in coefficients of expansion
between solder, chip and substrate. AVX terminations are
suitable for all wave and reflow soldering systems. If hand
soldering cannot be avoided, the preferred technique is the
utilization of hot air soldering tools.
Cooling
Natural cooling in air is preferred, as this minimizes stresses
within the soldered joint. When forced air cooling is used,
cooling rate should not exceed 4°C/second. Quenching
is not recommended but if used, maximum temperature
differentials should be observed according to the preheat
conditions above.
Cleaning
Flux residues may be hygroscopic or acidic and must be
removed. AVX MLC capacitors are acceptable for use with
all of the solvents described in the specifications MIL-STD-
202 and EIA-RS-198. Alcohol based solvents are acceptable
and properly controlled water cleaning systems are also
acceptable. Many other solvents have been proven successful,
and most solvents that are acceptable to other components
on circuit assemblies are equally acceptable for use with
ceramic capacitors.
72
Angled crack between bottom of device to top of solder joint.
POST SOLDER HANDLING
Once SMP components are soldered to the board, any
bending or flexure of the PCB applies stresses to the sol-
dered joints of the components. For leaded devices, the
stresses are absorbed by the compliancy of the metal leads
and generally don’t result in problems unless the stress is
large enough to fracture the soldered connection.
Ceramic capacitors are more susceptible to such stress
because they don’t have compliant leads and are brittle in
nature. The most frequent failure mode is low DC resistance
or short circuit. The second failure mode is significant loss
of capacitance due to severing of contact between sets of
the internal electrodes.
Cracks caused by mechanical flexure are very easily identi-
fied and generally take one of the following two general
forms:
Mechanical cracks are often hidden underneath the termi-
nation and are difficult to see externally. However, if one end
termination falls off during the removal process from PCB,
this is one indication that the cause of failure was excessive
mechanical stress due to board warping.
Fracture from top of device to bottom of device.
Type A:
Type B: