PIIPM25P12B008X Vishay, PIIPM25P12B008X Datasheet - Page 15
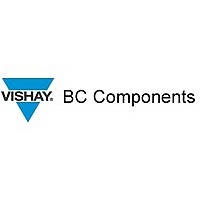
PIIPM25P12B008X
Manufacturer Part Number
PIIPM25P12B008X
Description
IC PWR MODULE PROG ISO 25A 1200V
Manufacturer
Vishay
Datasheet
1.PIIPM25P12B008X.pdf
(28 pages)
Specifications of PIIPM25P12B008X
Module/board Type
Programmer Module
For Use With/related Products
Servo Motors
Lead Free Status / RoHS Status
Contains lead / RoHS non-compliant
www.irf.com
PIIPM25P12B008
the same leg. In this case the protection is
implemented by means of the fourth sensing
element, with the same resistive value of the
other shunts present in the power module,
inserted in series to the DC bus minus. The
related dropout voltage is then filtered by a
15kHz passive filter to avoid false fault
detections due to unwanted induced voltage
spikes and finally applied to an operational
amplifier configured as a comparator. All data
referred to the OC protection are listed on page 9
of this datasheet.
4. Gate Drivers
Devices used to perform this task are the well-
known IR2213, capable of 2A sink and 2A source
maximum gate driving current, in a SO16W
package; on page 2 is shown also the block
schematic of the gate driving section of the
module.
The IGBTs used in the PI-IPM
1200V - 25A from IR) do not need any negative
gate drive voltage for their complete turn off, this
simplifies the flyback power supply design
avoiding the need of center tapped transformer
outputs or the use of zener diodes to create the
central common reference for the gate drivers
floating ground. Though the IR2213 do have +/-
2A of gate current capability, in the PI-
IPM25P12B008 we use different gate resistor
values for turn on and turn off as follows:
Commonly realized through a diode-resistor
series in parallel with a single resistor used in
turn on only. Observed rise and fall times are
around 250ns – 300ns depending on the output
current level, this values are considered as pretty
adequate for a 12.5A application at 16kHz
symmetric
modulation.
PWM
turn
turn
on
off
I27147 02 - Oct
carrier,
68
22
ohm
ohm
space
(genV NPT
vector
These gate drivers do provide levels shifting
without any galvanic isolation, that is no opto-
couplers are built inside. This turns out to be a
major benefit in this stage where the usual 1 s
delay of optos impacts on the system control as a
systematic and fastidious delay.
5. DC bus and Input voltage feedback
The purpose of this block is to continuously
check the voltage of the two supply lines of the
system: Vin and DC bus. Vin is the only external
power supply needed for all electronics in the
EDB. The internal flyback regulator has its own
under-voltage lockout to prevent all electronics
from start working when an insufficient supply
voltage is present; minimum recommended
supply voltage is 12V. Low side gate drivers are
directly fed from the Vin line and there is no
further control to this voltage than their own
under-voltage lockout. This is typically set at
8.5V and this level could be not sufficient to
properly drive the IGBT gates, then it is advisable
to check with the DSP the input voltage and
impose that the system could start switching only
when the Vin voltage is between 10V and 18V
thus providing also an over-voltage control.
The DC bus voltage is also important for the
system functioning and needs to be continuously
kept under control. A resistor divider provides a
partition
maximum mapped voltage of around 1100V
As the block schematic shows, it has to be taken
into account that, to avoid false detections due to
voltage
partitioned voltage, a 1kHz passive filter has been
inserted between the divider and the voltage
follower buffer whose output is connected to one
of the ADC inputs.
spikes
coefficient
inevitably
of
2.44mV/V
present
on
and
the
15
a