LM34914EVAL National Semiconductor, LM34914EVAL Datasheet - Page 11
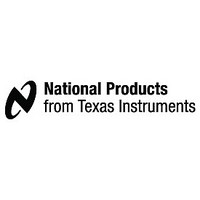
LM34914EVAL
Manufacturer Part Number
LM34914EVAL
Description
BOARD EVALUATION LM34914
Manufacturer
National Semiconductor
Specifications of LM34914EVAL
Main Purpose
DC/DC, Step Down
Outputs And Type
1, Non-Isolated
Voltage - Output
5V
Current - Output
1A
Voltage - Input
8 ~ 40V
Regulator Topology
Buck
Frequency - Switching
275kHz
Board Type
Fully Populated
Utilized Ic / Part
LM34914
Lead Free Status / RoHS Status
Contains lead / RoHS non-compliant
Power - Output
-
- Minimum and maximum load current (I
(max)
- Switching Frequency (F
R1 and R2: These resistors set the output voltage. The ratio
of these resistors is calculated from:
R1 and R2 should be chosen from standard value resistors in
the range of 1.0 kΩ - 10 kΩ which satisfy the above ratio.
R
switching frequency. Its value can be determined using equa-
tion 5 based on the frequency, or equation 4 if a specific on-
time is required. The minimum allowed value for R
calculated from:
L1: The main parameter affected by the inductor is the output
current ripple amplitude (I
used to determine the maximum allowable ripple. In order to
maintain continuous conduction mode the valley should not
reach 0 mA. This is not a requirement of the LM34914, but
serves as a guideline for selecting L1. For this case, the max-
imum ripple current is:
If the minimum load current is zero, use 20% of I
I
then used in the following equation:
where Fs is the switching frequency. This provides a minimum
value for L1. The next larger standard value should be used,
and L1 should be rated for the peak current level, equal to
I
C2 and R3: Since the LM34914 requires a minimum of 25
mVp-p of ripple at the FB pin for proper operation, the required
ripple at V
ple is created by the inductor ripple current flowing through
R3, and to a lesser extent by C2 and its ESR. The minimum
inductor ripple current is calculated using equation 7, rear-
ranged to solve for I
The minimum value for R3 is then equal to:
Typically R3 is less than 5Ω. C2 should generally be no small-
er than 3.3 µF, although that is dependent on the frequency
and the desired output characteristics. C2 should be a low
ESR good quality ceramic capacitor. Experimentation is usu-
ally necessary to determine the minimum value for C2, as the
nature of the load may require a larger value. A load which
creates significant transients requires a larger value for C2
than a non-varying load.
OUT(min)
OUT(max)
ON
)
: The resistor sets the on-time, and consequently, the
in equation 6. The ripple calculated in Equation 6 is
+ I
OUT
OR(max)
is increased by R1 and R2. This necessary rip-
I
OR(MAX)
/2.
R1/R2 = (V
OR
at minimum V
= 2 x I
S
)
OR
). The minimum load current is
OUT
OUT(min)
/2.5V) - 1
IN
.
OUT(min)
OUT(max)
and I
ON
OUT
(6)
(7)
for
is
11
D1: A Schottky diode is recommended. Ultra-fast recovery
diodes are not recommended as the high speed transitions at
the SW pin may inadvertently affect the IC’s operation through
external or internal EMI. The diode should be rated for the
maximum input voltage (V
(I
rent limit and maximum ripple current are reached simultane-
ously. The diode’s average power dissipation is calculated
from:
where V
cycle.
C1 and C5: C1’s purpose is to supply most of the switch cur-
rent during the on-time, and limit the voltage ripple at VIN, on
the assumption that the voltage source feeding VIN has an
output impedance greater than zero. If the source’s dynamic
impedance is high (effectively a current source), it supplies
the average input current, but not the ripple current.
At maximum load current, when the buck switch turns on, the
current into V
inductor’s ripple current, ramps up to the upper peak, then
drop to zero at turn-off. The average current during the on-
time is the load current. For a worst case calculation, C1 must
supply this average load current during the maximum on-time.
C1 is calculated from:
where t
ripple voltage at V
and ringing due to long lead inductance leading to the VIN pin.
A low ESR, 0.1 µF ceramic chip capacitor is recommended,
and must be located close to the VIN and RTN pins.
C3: The capacitor at the V
filtering and stability, but also prevents false triggering of the
V
no smaller than 0.1 µF, and should be a good quality, low
ESR, ceramic capacitor. C3’s value, and the V
determine a portion of the turn-on-time (t1 in Figure 1).
C4: The recommended value for C4 is 0.022 µF. A high quality
ceramic capacitor with low ESR is recommended as C4 sup-
plies a surge current to charge the buck switch gate at turn-
on. A low ESR also helps ensure a complete recharge during
each off-time.
C6: The capacitor at the SS pin determines the softstart time,
i.e. the time for the output voltage, to reach its final value (t2
in Figure 1). The capacitor value is determined from the fol-
lowing:
PC BOARD LAYOUT
The LM34914 regulation, over-voltage, and current limit com-
parators are very fast, and respond to short duration noise
pulses. Layout considerations are therefore critical for opti-
mum performance. The layout must be as neat and compact
as possible, and all of the components must be as close as
possible to their associated pins. The current loop formed by
D1, L1, C2 and the SGND and ISEN pins should be as small
as possible. The ground connection from SGND and RTN to
C1 should be as short and direct as possible.
OUT(max)
CC
UVLO at the buck switch on/off transitions. C3 should be
ON
F
), and the peak current which occurs when the cur-
is the diode's forward voltage drop, and D is the duty
is the maximum on-time, and ΔV is the allowable
IN
suddenly increases to the lower peak of the
IN
P
. C5’s purpose is to help avoid transients
D1
= V
IN(max)
F
CC
x I
output provides not only noise
OUT
), the maximum load current
x (1-D)
CC
current limit,
www.national.com