MAX126EVB16 Maxim Integrated Products, MAX126EVB16 Datasheet - Page 4
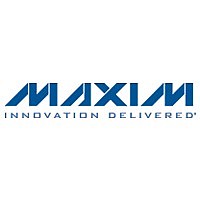
MAX126EVB16
Manufacturer Part Number
MAX126EVB16
Description
EVAL KIT FOR MAX126
Manufacturer
Maxim Integrated Products
Specifications of MAX126EVB16
Number Of Adc's
4
Number Of Bits
14
Sampling Rate (per Second)
250k
Data Interface
Parallel
Inputs Per Adc
2 Single
Input Range
±2.5 V
Power (typ) @ Conditions
165mW @ 250kSPS
Voltage Supply Source
Analog and Digital, Dual ±
Operating Temperature
0°C ~ 70°C
Utilized Ic / Part
MAX126
Lead Free Status / RoHS Status
Lead free / RoHS Compliant
To sample data at rates up to 40ksps, select “Sampling
Tool” from the Window menu, make your selections,
and click on the Start button. Adjust the timing delays
as appropriate to control the sample rate. Estimate the
effective sample rate by taking the reciprocal of the
sum of the delay between samples, the power-up
delay, and the conversion time. Sample size is restrict-
ed to a power of two so that the “Fast Fourier
Transform” (FFT) tool can process the data. “Sample
Size” controls the number of samples collected on
each selected channel. After the samples have been
collected, the data is automatically uploaded to the
host and graphed. Once displayed, the data can
optionally be saved to a file.
The EV software includes an FFT tool that can display
the spectral content of data collected with the high-
speed sampling tool.
To view the spectral content of a waveform, first select
a data sample that was previously collected with the
“Sampling Tool.” Then select “FFT Tool” from the
Window menu. Check the output plots desired and
click on the Start button.
A data-windowing function preprocesses the data
sample before performing an FFT.
nal is not synchronized to the sampling clock, spectral
energy appears to leak into nearby frequency buckets.
A suitable data window tapers the raw data to zero
amplitude at the beginning and end, reducing this spec-
tral leakage.
The “Device Characteristics” dialog box contains para-
meters that are not expected to change often. The
device selection is used to select between the MAX125
and the MAX126.
The MAX125 software can evaluate the MAX126 direct-
ly. From the Window menu, select “Device Charac-
teristics.” Next, change the device type from MAX125
to MAX126. This tells the program that the input voltage
span is ±V
MAX125/MAX126 Evaluation
Systems/Evaluation Kits
1) For more information on the FFT and data-windowing functions, refer to W.H. Press, et al., Numerical Recipes in Pascal: The Art of
4
Scientific Computing, Cambridge University Press, 1989, ISBN 0-521-37516-9.
_______________________________________________________________________________________
REF
instead of ±2V
Device Characteristics
REF
Evaluating the MAX126
.
1)
When the input sig-
Sampling Tool
FFT Tool
The EV kit software assumes a 2.5V reference voltage,
unless otherwise specified. Apply an external 2.5V ref-
erence to the REFIN pad to overdrive the internal refer-
ence. See the MAX125/MAX126 data sheet for more
information. From the Window menu, select “Device
Characteristics.” Next, type the new reference voltage
into the “Reference Voltage” edit box.
The ADC (U1) is an 8-channel, 14-bit data-acquisition
system with four simultaneous track/holds. Linear regu-
lators U2 and U4 provide clean analog ±5V power sup-
plies for the ADC. R8 and C1 filter digital noise out of
the analog power supply. U3 isolates the
and CONVST signals from the main system bus to fur-
ther prevent digital noise from entering the ADC. R7
and C11 filter the TTL clock oscillator to prevent over-
shoot at the CLK input.
The MAX125/MAX126’s chip-select (CS) is memory-
mapped to location 7E000 on the 68HC16 module. This
location is used for writing configuration bytes and
reading data. The convert-start (CONVST) signal is also
memory-mapped and is asserted for one memory-
access cycle when memory location 7E800 is
accessed. The MAX125/MAX126’s interrupt (INT) out-
put triggers an interrupt on the 68HC16 through the
input capture vector.
To monitor supply current, measure the voltage across
resistor R1 (for the +5V supply) or R6 (for the -5V sup-
ply). These resistors are 100Ω ±1%, so every 1mV
across R1 or R6 represents 10µA of supply current.
Table 3. Troubleshooting Guide
No output measurement.
System seems to report
zero voltage or fails to
make a measurement.
PROBLEM
Changing the Reference Voltage
Measuring Supply Current
Detailed Description
CORRECTIVE ACTIONS
Check the +5V and -5V sup-
ply voltages.
Check the 2.5V REFOUT ref-
erence voltage using a digi-
tal voltmeter.
Use an oscilloscope to verify
that the 16MHz clock is run-
ning and that the conver-
sion-start signal is being
strobed.
of Hardware
CS, RD, WR,