MAX1714AEEP Maxim Integrated Products, MAX1714AEEP Datasheet - Page 12
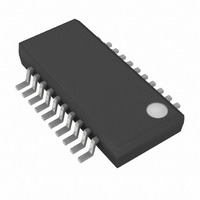
MAX1714AEEP
Manufacturer Part Number
MAX1714AEEP
Description
IC CTRLR HS STEPDOWN 20-QSOP
Manufacturer
Maxim Integrated Products
Type
Step-Down (Buck)r
Datasheet
1.MAX1714AEEP.pdf
(24 pages)
Specifications of MAX1714AEEP
Internal Switch(s)
No
Synchronous Rectifier
Yes
Number Of Outputs
1
Voltage - Output
2.5V, 3.3V, Adj
Current - Output
8A
Frequency - Switching
600kHz
Voltage - Input
2 ~ 28 V
Operating Temperature
-40°C ~ 85°C
Mounting Type
Surface Mount
Package / Case
20-QSOP
Power - Output
727mW
Output Voltage
1 V to 5.5 V
Output Current
3000 mA
Mounting Style
SMD/SMT
Switching Frequency
600 KHz
Maximum Operating Temperature
+ 85 C
Minimum Operating Temperature
- 40 C
Synchronous Pin
No
Topology
Buck
Case
SSOP20
Dc
04+
Lead Free Status / RoHS Status
Contains lead / RoHS non-compliant
Available stocks
Company
Part Number
Manufacturer
Quantity
Price
Part Number:
MAX1714AEEP
Manufacturer:
MAXIM/美信
Quantity:
20 000
Company:
Part Number:
MAX1714AEEP+
Manufacturer:
Maxim Integrated Products
Quantity:
135
Company:
Part Number:
MAX1714AEEP+
Manufacturer:
ISSI
Quantity:
7 229
Part Number:
MAX1714AEEP+
Manufacturer:
MAXIM/美信
Quantity:
20 000
Company:
Part Number:
MAX1714AEEP+T
Manufacturer:
MAXM
Quantity:
7 341
Company:
Part Number:
MAX1714AEEP-T
Manufacturer:
ISSI
Quantity:
6 816
Part Number:
MAX1714AEEP-T
Manufacturer:
MAXIM/美信
Quantity:
20 000
High-Speed Step-Down Controller
for Notebook Computers
where K is set by the TON pin-strap connection and
0.075V is an approximation to accommodate for the
expected drop across the low-side MOSFET switch.
One-shot timing error increases for the shorter on-time
settings due to fixed propagation delays; it is approxi-
mately ±12.5% at 600kHz and 450kHz, and ±10% at the
two slower settings. This translates to reduced switching-
frequency accuracy at higher frequencies (Table 5).
Switching frequency increases as a function of load cur-
rent due to the increasing drop across the low-side
MOSFET, which causes a faster inductor-current dis-
charge ramp. The on-times guaranteed in the Electrical
Characteristics are influenced by switching delays in the
external high-side power MOSFET.
Two external factors that influence switching-frequency
accuracy are resistive drops in the two conduction loops
(including inductor and PC board resistance) and the
dead-time effect. These effects are the largest contribu-
tors to the change of frequency with changing load cur-
rent. The dead-time effect increases the effective
on-time, reducing the switching frequency as one or
both dead times are added to the effective on-time. It
occurs only in PWM mode (SKIP = high) when the induc-
tor current reverses at light or negative load currents.
With reversed inductor current, the inductor’s EMF caus-
es LX to go high earlier than normal, extending the on-
time by a period equal to the low-to-high dead time.
For loads above the critical conduction point, the actual
switching frequency is:
where V
in the inductor discharge path, including synchronous
rectifier, inductor, and PC board resistances; V
the sum of the resistances in the charging path, and t
is the on-time calculated by the MAX1714.
In skip mode (SKIP low), an inherent automatic
switchover to PFM takes place at light loads. This
switchover is effected by a comparator that truncates the
low-side switch on-time at the inductor current’s zero
crossing. This mechanism causes the threshold between
pulse-skipping PFM and nonskipping PWM operation to
coincide with the boundary between continuous and dis-
continuous inductor-current operation (also known as the
“critical conduction” point; see the Continuous to
Discontinuous Inductor Current Point vs. Input Voltage
graph in the
12
______________________________________________________________________________________
DROP1
Automatic Pulse-Skipping Switchover
f
=
Typical Operating Characteristics). In low-
t
is the sum of the parasitic voltage drops
ON IN
V
OUT
(V
+
+
V
V
DROP1
DROP2
)
DROP2
ON
is
duty-cycle applications, this threshold is relatively con-
stant, with only a minor dependence on battery voltage.
where K is the on-time scale factor (Table 5). The load-
current level at which PFM/PWM crossover occurs,
I
rent, which is a function of the inductor value (Figure 3).
For example, in the standard application circuit with
K = 3.3µs (Table 5), V
6.8µH, switchover to pulse-skipping operation occurs at
I
occurs at an even lower value if a swinging (soft-satura-
tion) inductor is used.
The switching waveforms may appear noisy and asyn-
chronous when light loading causes pulse-skipping
operation, but this is a normal operating condition that
results in high light-load efficiency. Trade-offs in PFM
noise vs. light-load efficiency are made by varying the
inductor value. Generally, low inductor values produce a
broader efficiency vs. load curve, while higher values
result in higher full-load efficiency (assuming that the coil
resistance remains fixed) and less output voltage ripple.
Penalties for using higher inductor values include larger
physical size and degraded load-transient response
(especially at low input voltage levels).
DC output accuracy specifications refer to the error-com-
parator threshold of the error comparator. When the
inductor is in continuous conduction, the output voltage
will have a DC regulation level higher than the trip level
by 50% of the ripple. In discontinuous conduction (SKIP
= AGND, light-loaded), the output voltage will have a DC
regulation level higher than the error-comparator thresh-
old by approximately 1.5% due to slope compensation.
The low-noise forced-PWM mode (SKIP = high) disables
the zero-crossing comparator, which controls the low-
side switch on-time. This causes the low-side gate-drive
waveform to become the complement of the high-side
gate-drive waveform. This in turn causes the inductor
current to reverse at light loads while DH maintains a
duty factor of V
mode is to keep the switching frequency fairly constant,
but it comes at a cost: the no-load battery current can be
10mA to 40mA, depending on the external MOSFETs.
Forced-PWM mode is most useful for reducing audio-
frequency noise, improving load-transient response, pro-
viding sink-current capability for dynamic output voltage
adjustment, and improving the cross-regulation of
LOAD(SKIP)
LOAD
I
= 0.51A or about 1/8 full load. The crossover point
LOAD(SKIP)
, is equal to 1/2 the peak-to-peak ripple cur-
Forced-PWM Mode ( SKIP = High)
OUT
≈
KV
/V
OUT
2L
OUT
IN
. The benefit of forced-PWM
= 2.5V, V
⋅
V - V
IN
V
IN
IN
OUT
= 15V, and L =