SC418ULTRT Semtech, SC418ULTRT Datasheet - Page 13
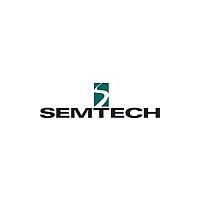
SC418ULTRT
Manufacturer Part Number
SC418ULTRT
Description
IC BUCK SYNC ADJ 20MLPQ
Manufacturer
Semtech
Series
EcoSpeed™, SmartDrive™r
Type
Step-Down (Buck)r
Datasheet
1.SC418ULTRT.pdf
(30 pages)
Specifications of SC418ULTRT
Internal Switch(s)
No
Synchronous Rectifier
Yes
Number Of Outputs
1
Voltage - Output
0.5 ~ 5.5 V
Frequency - Switching
200kHz ~ 1MHz
Voltage - Input
3 ~ 28 V
Operating Temperature
-40°C ~ 85°C
Mounting Type
Surface Mount
Package / Case
20-MLPQ
Lead Free Status / RoHS Status
Lead free / RoHS Compliant
Current - Output
-
Power - Output
-
Other names
SC418ULTRTTR
Applications Information
Synchronous Buck Converter
The SC418 is a step down synchronous DC-DC buck con-
troller with a programmable LDO. It provides high effi-
ciency operation in a space saving 3x3 (mm) 20-pin
package. The programmable operating frequency range
of 200kHz to 1MHz enables optimizing the configuration
for PCB area and efficiency.
The controller uses a pseudo-fixed frequency adaptive
on-time control. This allows fast transient response which
permits the use of smaller output capacitors.
Input Voltage Requirements
The SC418 requires three input supplies for normal opera-
tion: V
range of 3V to 28V. VDDA and VDDP require a 3.3V or 5V
supply which can be from an external source or from the
internal LDO configured to 3.3V or 5V. VDDA and VDDP
should derive from the same source voltage. Power-save
operation and Ultrasonic Power-save are not supported
for VDDA/VDDP below 4.5V.
Psuedo-fixed Frequency Adaptive On-time Control
The PWM control method used by the SC418 is pseudo-
fixed frequency, adaptive on-time, as shown in Figure 1.
The ripple voltage generated at the output capacitor ESR
is used as a PWM ramp signal. This ripple is used to trigger
the on-time of the controller.
In addition to the following information, the user can
click on the applicable link to go to the SC418 online
C-SIM design and simulation
user through the design process.
IN
, VDDA, and VDDP. V
tool, which will lead the
IN
operates over the wide
The adaptive on-time is determined by an internal one-
shot timer. When the one-shot is triggered by the output
ripple, the device sends a single on-time pulse to the high-
side MOSFET. The pulse period is determined by V
V
inversely proportional to input voltage. With this adaptive
on-time configuration, the device automatically antici-
pates the on-time needed to regulate V
V
The advantages of adaptive on-time control are:
One-Shot Timer and Operating Frequency
One-shot timer operation is shown in Figure 2. The FB
comparator output goes high when V
internal 500mV reference. This feeds into the DH gate
drive and turns on the high-side MOSFET, and also starts
the one-shot timer. The one-shot timer uses an internal
IN
IN
Q1
Q2
•
•
•
•
•
V
. The period is proportional to output voltage and
condition and at the selected frequency.
IN
Figure 1 — PWM Control Method, V
Predictable operating frequency compared to
other variable frequency methods.
Reduced component count by eliminating the
error amplifier and compensation components.
Reduced component count by removing the
need to sense and control inductor current.
Fast transient response — the response time is
controlled by a fast comparator instead of a typi-
cally slow error amplifier.
Reduced output capacitance due to fast tran-
sient response.
V
LX
C
IN
L
TON
V
+
ESR
FB
C
OUT
V
LX
OUT
FB
is less than the
OUT
FB Threshold
for the present
Ripple
SC418
OUT
FB
V
OUT
and
13