MIC38C43BM TR Micrel Inc, MIC38C43BM TR Datasheet - Page 7
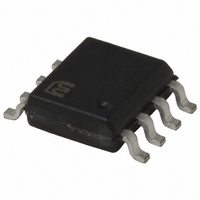
MIC38C43BM TR
Manufacturer Part Number
MIC38C43BM TR
Description
IC CTRLR PWM CURRENT MODE 8-SOIC
Manufacturer
Micrel Inc
Datasheet
1.MIC38C42YN.pdf
(11 pages)
Specifications of MIC38C43BM TR
Pwm Type
Current Mode
Number Of Outputs
1
Frequency - Max
500kHz
Duty Cycle
96%
Voltage - Supply
7.6 V ~ 20 V
Buck
Yes
Boost
Yes
Flyback
Yes
Inverting
No
Doubler
No
Divider
No
Cuk
No
Isolated
Yes
Operating Temperature
-40°C ~ 85°C
Package / Case
8-SOIC (3.9mm Width)
Frequency-max
500kHz
Lead Free Status / RoHS Status
Contains lead / RoHS non-compliant
Other names
MIC38C43BMTR
MIC38C43BMTR
MIC38C43BMTR
MIC38C42/3/4/5
Application Information
Familiarity with 384x converter designs is assumed.
The MIC38C4x has been designed to be compatible with
384xA series controllers.
MIC38C4x Advantages
Start-up Current
Start-up current has been reduced to an ultra-low 50µA (typi-
cal) permitting higher-valued, lower-wattage, start-up resistors
(powers controller during power supply start-up). The reduced
resistor wattage reduces cost and printed circuit space.
Operating Current
Operating current has been reduced to 4mA compared to
11mA for a typical bipolar controller. The controller runs
cooler and the V
start-up may be reduced.
Output Driver
Complementary internal P- and N-channel MOSFETs pro-
duce rail-to-rail output voltages for better performance driving
external power MOSFETs. The driver transistor’s low on-
resistance and high peak current capability can drive gate
capacitances of greater than 1000pF. The value of output
capacitance which can be driven is determined only by the
rise/fall time requirements. Within the restrictions of output
capacity and controller power dissipation, maximum switching
frequency can approach 500kHz.
Design Precautions
When operating near 20V, circuit transients can easily exceed
the 20V absolute maximum rating, permanently damaging the
controller’s CMOS construction. To reduce transients, use
a 0.1µF low-ESR capacitor to next to the controller’s supply
V
type capacitors, such as Wima MKS2, are recommended.
September 2007
DD
(or V
D
for ‘-1’ versions) and ground connections. Film
M17Z105
26V to 40V
1/4W
V
D2
IN
DD
MBR030
D3
R2
68k
hold-up capacitance required during
0.22µF
6.8k
R4
18
100k
Figure 1. 500kHz, 25W, Buck Converter
0.1µF*
C7
200pF
1
2
3
4
COM P
F B
I S N S
RT/CT GND
MIC38C42
CT1
16k
V R E F
R5
VDD
OU T
MKS2
8
7
6
5
0.1µF
4.7µF
C5
7
0.1µF
C8
1N765B
When designing high-frequency converters, avoid capacitive
and inductive coupling of the switching waveform into high-
impedance circuitry such as the error amplifier, oscillator, and
current sense amplifier. Avoid long printed-circuit traces and
component leads. Locate oscillator and compensation circuitry
near the IC. Use high frequency decoupling capacitors on
V
directly to their source and use large area ground planes.
Buck Converter
Refer to figure 1. When at least 26V is applied to the input,
C5 is charged through R2 until the voltage V
than 14.5V (the undervoltage lockout value of the MIC38C42).
Output switching begins when Q1 is turned on by the gate
drive transformer T1, charging the output filter capacitor C3
through L1. D5 supplies a regulated +12V to V
circuit is running.
Current sense transformer CT1 provides current feedback to
ISNS for current-mode operation and cycle-by-cycle current
limiting. This is more efficient than a high-power sense resistor
and provides the required ground-referenced level shift.
When Q1 turns off, current flow continues from ground through
D1 and L1 until Q1 is turned on again.
The 100V Schottky diode D1 reduces the forward voltage drop
in the main current path, resulting in higher efficiency than
could be accomplished using an ultra-fast-recovery diode.
R1 and C2 suppress parasitic oscillations from D1.
Using a high-value inductance for L1 and a low-ESR capaci-
tor for C3 permits small capacitance with minimum output
ripple. This inductance value also improves circuit efficiency
by reducing the flux swing in L1.
Magnetic components are carefully chosen for minimal loss
at 500kHz. CT1 and T1 are wound on Magnetics, Inc. P-
type material toroids. L1 is wound on a Siemens N49 EFD
core.
REF
4.7Ω
0.1µF
D4
T1
IRF820
, and if necessary, on V
Q1
*Locate near MIC38C42 supply pins
1000pF
R1
10
1/2W
C2
31DQ10
L1 48µH
D1
1N4001
D5
3.3µF
C3
DD
. Return high di/dt currents
0.1µF
C4
6.19k
1.62k
1%
1%
12V, 2A
V
O U T
DD
M9999-091107
DD
Micrel, Inc.
is greater
once the