ADN8830ACPZ Analog Devices Inc, ADN8830ACPZ Datasheet - Page 12
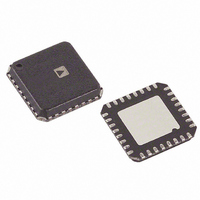
ADN8830ACPZ
Manufacturer Part Number
ADN8830ACPZ
Description
IC CTRLR THERMO COOLER 32-LFCSP
Manufacturer
Analog Devices Inc
Datasheet
1.ADN8830ACPZ-REEL7.pdf
(24 pages)
Specifications of ADN8830ACPZ
Applications
Thermoelectric Cooler
Current - Supply
8mA
Voltage - Supply
3.3 V ~ 5 V
Operating Temperature
-40°C ~ 85°C
Mounting Type
Surface Mount
Package / Case
32-LFCSP
Ic Function
Thermoelectric Cooler Controller
Supply Voltage Range
3V To 5.5V
Operating Temperature Range
-40°C To +85°C
Digital Ic Case Style
LFCSP
No. Of Pins
32
Msl
MSL 1 - Unlimited
Lead Free Status / RoHS Status
Lead free / RoHS Compliant
Other names
015-0070
Q2376189
Q2376189
Available stocks
Company
Part Number
Manufacturer
Quantity
Price
Company:
Part Number:
ADN8830ACPZ
Manufacturer:
ADI
Quantity:
317
Part Number:
ADN8830ACPZ
Manufacturer:
ADI/亚德诺
Quantity:
20 000
ADN8830
The unity-gain crossover frequency of the feedforward amplifier
is given as
To ensure stability, the unity-gain crossover frequency should be
lower than the thermal time constant of the TEC and thermistor.
However, this thermal time constant may not be specified and
can be difficult to characterize.
There are many texts written on loop stabilization, and it is beyond
the scope of this data sheet to discuss all methods and trade-offs
in optimizing compensation networks. A simple method that
can be used to empirically determine a PID compensation loop
as shown in Figure 9 involves the following procedure:
1. Connect thermistor and TEC to the ADN8830 application
2. Short C1 and open C2, leaving just R1 and R3 as a simple
3. While maintaining a constant TEMPSET voltage, increase
4. Add C1 capacitor and decrease value until oscillation starts,
5. Short R2 and increase C2 until oscillation starts. At this point,
6. TEMPSET should be adjusted with a step change while
7. An additional feedback capacitor, CF, in parallel with R1
The typical values shown in the typical application circuit in
Figure 1 have R1 = 100 k , R2 = 1 M , R3 = 205 k , C1 = 10 F,
C2 = 1 F, and an additional feedback capacitor of 330 pF. For
most pump laser modules, this results in a 10 C TEMPSET step
settling time to within 0.1 C in less than 5 seconds.
circuit. Power does not need to be applied to the laser diode
for this procedure. Monitor output voltage across the TEC
with an oscilloscope.
proportional-only compensation loop.
the ratio of R1/R3, thus increasing the gain until loop oscilla-
tion starts to occur. Decrease this ratio by a factor of 2 from
the point of oscillation. The R1/R3 ratio will likely be less
than unity for most laser modules.
then increase by a factor of 2. A good initial starting value for
C1 is to create a unity-gain crossover of 0.1 Hz based on
Equation 15.
either C2 can be decreased or R2 can be added to regain
stability. Generally speaking, R2 will be greater than R3 and
C2 will be one or more orders of magnitude less than C1.
observing the output voltage settling time. A step change of
100 mV should suffice. From here, C2, R2, and even C1 can
be decreased to minimize settling time at the expense of
additional output voltage overshoot.
and C1, can be added to add another high frequency pole. In
many cases, this improves the stability of the system without
increasing the settling time as out-of-band noise is filtered
out of the control signal. A 330 pF to 1 nF capacitor should
suffice, if required.
Figure 9. Implementing a PID Compensation Loop
f
0
dB
2
R C
TEMPCTL
ADN8830
1
12
3 1
R2
80
REFERENCE
R3
COMPFB
VOLTAGE
C2
TEC GAIN
13
R1
COMPOUT
CF
C1
14
(15)
–12–
Using the TEC Controller ADN8830 with a Wave Locker
Many optical applications require precision control of laser
wavelength. The wavelength of the laser diode can be adjusted
by changing its temperature, which is done through temperature
control of the TEC. Wavelength control can be done by feeding
a wave locker or etalon output back to the microprocessor and
using the microprocessor to calculate and reinstruct the TEC
controller with a new target temperature. However, this method
is computationally expensive and has time delays before the
adjustment is done. A faster responding and simpler method is
to feed the wave locker signal back to the TEC controller for
direct temperature control.
The ADN8830 is designed to be compatible with a wave locker
controller. Figure 11 shows the basic schematic. The TEMPCTL
output from ADN8830 is proportional to the object’s actual
temperature. This voltage is fed to the wave locker controller.
Also fed to the wave locker controller are the photodiode out-
puts from the wave locker, as well as the laser diode power and
a digital signal indicating a functional laser diode, both of which
come from the CW controller. The output of the wave locker
controller is then connected to the input of the compensation
network. This allows the wave locker controller to adjust the
TEC temperature based on the current temperature of the
object, the current wavelength of the laser diode, and the target
wavelength. Once the target wavelength is reached, the wave
locker controller sends a signal to the microcontroller indicating
that the laser signal is good.
Figure 11. Using the ADN8830 with a Wave Locker
R2||R3
COMPFB
Figure 10. Bode Plot for PID Compensation
ADN8830
13
R1
0dB
R1
R3
2 R3C1
1
COMPOUT
TEMPCTL
14
COMPENSATION
NETWORK
FREQUENCY (Hz LOG SCALE)
2 R1C1
12
FROM CW
CONTROLLER
1
FROM
LOCKER
2 C2(R2+R3)
WAVE LOCKER
PD1
PD2
LASER DIODE
POWER
LASER DIODE
GOOD
TEMP IN
1
LOCKER
LOCKER
CONTROL
GOOD
TEC
2 R2C2
1
TO
MICRO-
PROCESSOR
REV. C