LM629N-8/NOPB National Semiconductor, LM629N-8/NOPB Datasheet - Page 19
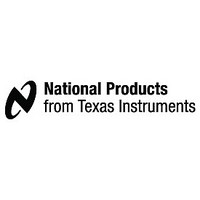
LM629N-8/NOPB
Manufacturer Part Number
LM629N-8/NOPB
Description
IC CONTROLLER PREC MOTION 28-DIP
Manufacturer
National Semiconductor
Datasheet
1.LM629N-6NOPB.pdf
(26 pages)
Specifications of LM629N-8/NOPB
Applications
DC Motor Controller, Servo
Number Of Outputs
1
Voltage - Supply
4.5 V ~ 5.5 V
Operating Temperature
-40°C ~ 85°C
Mounting Type
Through Hole
Package / Case
28-DIP (0.600", 15.24mm)
Lead Free Status / RoHS Status
Lead free / RoHS Compliant
Current - Output
-
Voltage - Load
-
Other names
*LM629N-8
*LM629N-8/NOPB
LM629N-8
*LM629N-8/NOPB
LM629N-8
Available stocks
Company
Part Number
Manufacturer
Quantity
Price
Company:
Part Number:
LM629N-8/NOPB
Manufacturer:
HITACHI
Quantity:
101
Company:
Part Number:
LM629N-8/NOPB
Manufacturer:
National Semiconductor
Quantity:
135
Typical Applications
provides the clock for the LM628. The 74LS245 is used to
decrease the read-data hold time, which is necessary when
interfacing to fast host busses.
INTERFACING A 12-BIT DAC
Figure 14 illustrates use of a 12-bit DAC with the LM628. The
74LS378 hex gated-D flip-flop and an inverter demultiplex
the 12-bit output. DAC offset must be adjusted to minimize
DAC linearity and monotonicity errors. Two methods exist for
making this adjustment. If the DAC1210 has been socketed,
remove it and temporarily connect a 15 kΩ resistor between
Pins 11 and 13 of the DAC socket (Pins 2 and 6 of the
LF356) and adjust the 25 kΩ potentiometer for 0V at Pin 6 of
the LF356.
If the DAC is not removable, the second method of adjust-
ment requires that the DAC1210 inputs be presented an
all-zeros code. This can be arranged by commanding the
appropriate move via the LM628, but with no feedback from
the system encoder. When the all-zeros code is present,
adjust the pot for 0V at Pin 6 of the LF356.
A MONOLITHIC LINEAR DRIVE USING LM12 POWER
OP AMP
Figure 15 shows a motor-drive amplifier built using the LM12
Power Operational Amplifier. This circuit is very simple and
can deliver up to 8A at 30V (using the LM12L/LM12CL).
Resistors R1 and R2 should be chosen to set the gain to
provide maximum output voltage consistent with maximum
input voltage. This example provides a gain of 2.2, which
allows for amplifier output saturation at
input, assuming power supply voltages of
fier gain should not be higher than necessary because the
system is non-linear when saturated, and because gain
should be controlled by the LM628. The LM12 can also be
configured as a current driver, see 1987 Linear Databook,
Vol. 1, p. 2–280.
(Continued)
±
22V with a
±
30V. The ampli-
±
10V
19
TYPICAL PWM MOTOR DRIVE INTERFACES
Figure 16 shows an LM18298 dual full-bridge driver inter-
faced to the LM629 PWM outputs to provide a switch-mode
power amplifier for driving small brush/commutator motors.
Incremental Encoder Interface
The incremental (position feedback) encoder interface con-
sists of three lines: Phase A (Pin 2), Phase B (Pin 3), and
Index (Pin 1). The index pulse output is not available on
some encoders. The LM628 will work with both encoder
types, but commands SIP and RDIP will not be meaningful
without an index pulse (or alternative input for this input …
be sure to tie Pin 1 high if not used).
Some consideration is merited relative to use in high
Gaussian-noise environments. If noise is added to the en-
coder inputs (either or both inputs) and is such that it is not
sustained until the next encoder transition, the LM628 de-
coder logic will reject it. Noise that mimics quadrature counts
or persists through encoder transitions must be eliminated
by appropriate EMI design.
Simple digital “filtering” schemes merely reduce susceptibil-
ity to noise (there will always be noise pulses longer than the
filter can eliminate). Further, any noise filtering scheme re-
duces decoder bandwidth. In the LM628 it was decided
(since simple filtering does not eliminate the noise problem)
to not include a noise filter in favor of offering maximum
possible decoder bandwidth. Attempting to drive encoder
signals too long a distance with simple TTL lines can also be
a source of “noise” in the form of signal degradation (poor
risetime and/or ringing). This can also cause a system to
lose positional integrity. Probably the most effective counter-
measure to noise induction can be had by using balanced-
line drivers and receivers on the encoder inputs. Figure 17
shows circuitry using the DS26LS31 and DS26LS32.
www.national.com