LM3410XMFE/NOPB National Semiconductor, LM3410XMFE/NOPB Datasheet - Page 11
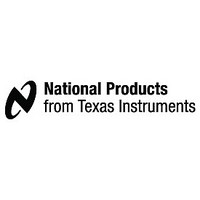
LM3410XMFE/NOPB
Manufacturer Part Number
LM3410XMFE/NOPB
Description
IC DRVR WT/OLED BCKLT SOT23-5
Manufacturer
National Semiconductor
Series
PowerWise®r
Type
Backlight, OLED, White LEDr
Datasheet
1.LM3410XMFNOPB.pdf
(32 pages)
Specifications of LM3410XMFE/NOPB
Constant Current
Yes
Topology
PWM, SEPIC, Step-Up (Boost)
Number Of Outputs
1
Internal Driver
Yes
Type - Primary
Automotive, Backlight, Flash/Torch
Type - Secondary
High Brightness LED (HBLED), OLED, White LED
Frequency
1.2MHz ~ 2MHz
Voltage - Supply
2.7 V ~ 5.5 V
Voltage - Output
3 V ~ 24 V
Mounting Type
Surface Mount
Package / Case
SOT-23-5, SC-74A, SOT-25
Operating Temperature
-40°C ~ 125°C
Current - Output / Channel
2.8A
Internal Switch(s)
Yes
Efficiency
88%
For Use With
LM3410XSDSEPEV - BOARD EVALUATION FOR LM3410
Lead Free Status / RoHS Status
Lead free / RoHS Compliant
Other names
LM3410XMFE
Available stocks
Company
Part Number
Manufacturer
Quantity
Price
Part Number:
LM3410XMFE/NOPB
Manufacturer:
NS/国半
Quantity:
20 000
This is very similar to our LM3410 demonstration boards that
are obtainable via the National Semiconductor website. The
demonstration board consists of a two layer PCB with a com-
mon input and output voltage application. Most of the routing
is on the top layer, with the bottom layer consisting of a large
ground plane. The placement of the external components
satisfies the electrical considerations, and the thermal perfor-
mance has been improved by adding thermal vias and a top
layer “Dog-Bone”.
For certain high power applications, the PCB land may be
modified to a "dog bone" shape (see Figure 8). Increasing the
size of ground plane and adding thermal vias can reduce the
R
Thermal Design
When designing for thermal performance, one must consider
many variables:
Ambient Temperature: The surrounding maximum air tem-
perature is fairly explanatory. As the temperature increases,
the junction temperature will increase. This may not be linear
though. As the surrounding air temperature increases, resis-
tances of semiconductors, wires and traces increase. This will
decrease the efficiency of the application, and more power
will be converted into heat, and will increase the silicon junc-
tion temperatures further.
θJA
for the application.
FIGURE 7. Boost PCB Layout Guidelines
FIGURE 8. PCB Dog Bone Layout
30038533
30038532
11
Forced Airflow: Forced air can drastically reduce the device
junction temperature. Air flow reduces the hot spots within a
design. Warm airflow is often much better than a lower am-
bient temperature with no airflow.
External Components: Choose components that are effi-
cient, and you can reduce the mutual heating between de-
vices.
PCB design with thermal performance in mind:
The PCB design is a very important step in the thermal design
procedure. The LM3410 is available in three package options
(5 pin SOT23, 8 pin eMSOP & 6 pin LLP). The options are
electrically the same, but difference between the packages is
size and thermal performance. The LLP and eMSOP have
thermal Die Attach Pads (DAP) attached to the bottom of the
packages, and are therefore capable of dissipating more heat
than the SOT23 package. It is important that the customer
choose the correct package for the application. A detailed
thermal design procedure has been included in this data
sheet. This procedure will help determine which package is
correct, and common applications will be analyzed.
There is one significant thermal PCB layout design consider-
ation that contradicts a proper electrical PCB layout design
consideration. This contradiction is the placement of external
components that dissipate heat. The greatest external heat
contributor is the external Schottky diode. It would be nice if
you were able to separate by distance the LM3410 from the
Schottky diode, and thereby reducing the mutual heating ef-
fect. This will however create electrical performance issues.
It is important to keep the LM3410, the output capacitor, and
Schottky diode physically close to each other (see PCB layout
guidelines). The electrical design considerations outweigh the
thermal considerations. Other factors that influence thermal
performance are thermal vias, copper weight, and number of
board layers.
Thermal Definitions
Heat energy is transferred from regions of high temperature
to regions of low temperature via three basic mechanisms:
radiation, conduction and convection.
Radiation: Electromagnetic transfer of heat between masses
at different temperatures.
Conduction: Transfer of heat through a solid medium.
Convection: Transfer of heat through the medium of a fluid;
typically air.
Conduction & Convection will be the dominant heat transfer
mechanism in most applications.
R
temperature.
R
temperature.
C
perature.
C
perature.
R
impedances, and most data sheets contain associated values
for these two symbols. The units of measurement are °C/
Watt.
R
thermal model Figures 9 and 10). Capacitors within the model
represent delays that are present from the time that power
and its associated heat is increased or decreased from steady
state in one medium until the time that the heat increase or
decrease reaches steady state in the another medium.
θJA
θJC
θJC
θCA
θJA
θJA
: Thermal impedance from silicon junction to ambient air
: Thermal impedance from silicon junction to device case
: Thermal Delay from silicon junction to device case tem-
: Thermal Delay from device case to ambient air tem-
is the sum of smaller thermal impedances (see simplified
& R
θJC
: These two symbols represent thermal
www.national.com