MAX16818ETI+ Maxim Integrated Products, MAX16818ETI+ Datasheet - Page 22
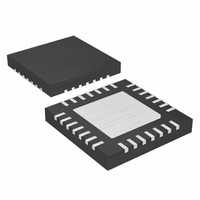
MAX16818ETI+
Manufacturer Part Number
MAX16818ETI+
Description
IC LED DRIVR PWM CONTROL 28-TQFN
Manufacturer
Maxim Integrated Products
Type
PWM Controlr
Datasheet
1.MAX16818ETI.pdf
(25 pages)
Specifications of MAX16818ETI+
Topology
High Side, Low Side, PWM, SEPIC, Step-Down (Buck), Step-Up (Boost)
Number Of Outputs
1
Internal Driver
No
Type - Primary
Automotive, Backlight
Type - Secondary
High Brightness LED (HBLED)
Frequency
125kHz ~ 1.5MHz
Voltage - Supply
4.75 V ~ 5.5 V, 7 V ~ 28 V
Voltage - Output
5.1V
Mounting Type
Surface Mount
Package / Case
28-TQFN Exposed Pad
Operating Temperature
-40°C ~ 85°C
Current - Output / Channel
30A
Internal Switch(s)
Yes
Low Level Output Current
4 A
High Level Output Current
4000000 uA (Typ)
Operating Supply Voltage
7 V to 28 V
Maximum Supply Current
5.5 mA
Maximum Power Dissipation
2758 mW
Maximum Operating Temperature
+ 85 C
Mounting Style
SMD/SMT
Minimum Operating Temperature
- 40 C
Lead Free Status / RoHS Status
Lead free / RoHS Compliant
Efficiency
-
Lead Free Status / Rohs Status
Lead free / RoHS Compliant
1.5MHz, 30A High-Efficiency, LED Driver
with Rapid LED Current Pulsing
Buck:
where I
example, at V
0.4A, and f
tance are calculated for the input peak-to-peak ripple of
100mV or less yielding an ESR and capacitance value
of 25mΩ and 10µF.
For boost regulator designs, the input-capacitor current
waveform is dominated by the inductor, a triangle wave
a magnitude of ∆I
waveform can be approximated by a square wave with
a magnitude that is half that of the triangle wave.
Calculate the input capacitance and ESR required for a
specified ripple using the following equation:
Boost:
Duty cycle, D, for a boost regulator is equal to (V
V
15.6V, I
ESR and input capacitance are calculated for the input
peak-to-peak ripple of 100mV or less yielding an ESR
and capacitance value of 250mΩ and 1µF, respectively.
For buck converters, the inductor always connects to
the load, so the inductance controls the ripple current.
The output capacitance shunts a fraction of this ripple
current and the LED string absorbs the rest. The
capacitor reactance (which includes the capacitance
and ESR) and the dynamic impedance of the LED
diode string form a conductance divider that splits the
ripple current between the LEDs and the capacitor. In
many cases, the capacitor is very large as compared to
the ESR, and this divider reduces to the ESR and the
LED resistance.
Boost converters place a harsher requirement on the
output capacitors as they must sustain the full load dur-
ing the on-time of the MOSFET and are replenished
during the off-time. The ripple current in this case is the
full load current, and the holdup time is equal to the
duty cycle times the switching period.
22
IN
) / V
______________________________________________________________________________________
OUT
OUT
OUT.
SW
is the output current of the converter. For
= 1A, ∆I
As an example, at V
IN
C
IN
= 330kHz, the ESR and input capaci-
= 13.2V, V
C
ESR
=
L.
IN
For simplicity’s sake, the current
L
I
OUT
=
IN
= 0.4A, and f
∆
V
∆
=
Q
LED
V
x D
∆
2
Q
I
x f
∆
L
V
∆
(
x f
= 7.8V, I
1
SW
ESR
x D
I
−
L
Output Capacitor
SW
D
IN
)
SW
= 13.2V, V
OUT
= 330kHz, the
= 1A, ∆I
LED
OUT
L
=
=
-
In addition to the average current limit, the MAX16818
also has hiccup current limit. The hiccup current limit is
set to 10% below the average current limit to ensure that
the circuit goes in hiccup mode during continuous out-
put short circuit. Connecting a resistor from LIM to
ground increases the hiccup current limit, while shorting
LIM to ground disables the hiccup current-limit circuit.
The average-current-mode control technique of the
MAX16818 accurately limits the maximum output current.
The MAX16818 senses the voltage across the sense
resistor and limit the peak inductor current (I
accordingly. The on-cycle terminates when the current-
sense voltage reaches 25.5mV (min). Use the following
equation to calculate the maximum current-sense resis-
tor value:
where PD
Select a 5% lower value of R
parasitics associated with the PCB. Also, select a non-
inductive resistor with the appropriate power rating.
The hiccup current-limit value is always 10% lower than
the average current-limit threshold, when LIM is left
unconnected. Connect a resistor from LIM to SGND to
increase the hiccup current-limit value from 90% to
100% of the average current-limit value. The average
current-limit architecture accurately limits the average
output current to its current-limit threshold. If the hiccup
current limit is programmed to be equal or above the
average current-limit value, the output current does not
reach the point where the hiccup current limit can trig-
ger. Program the hiccup current limit at least 5% below
the average current limit to ensure that the hiccup cur-
rent-limit circuit triggers during overload. See the
Hiccup Current Limit vs. R
Operating Characteristics .
R
is the dissipation in the series resistors.
PD
R
R
S
=
=
0 75
.
0 0255
I
.
OUT
R
x
EXT
S
S
10
Average Current Limit
to compensate for any
−
Hiccup Current Limit
graph in the Typical
3
Current Limit
L-PK
)