pth03010 Astec Powe, pth03010 Datasheet - Page 10
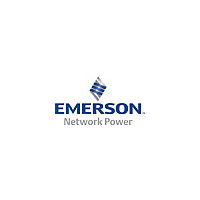
pth03010
Manufacturer Part Number
pth03010
Description
Pth03020 3.3vin Single
Manufacturer
Astec Powe
Datasheet
1.PTH03010.pdf
(12 pages)
Available stocks
Company
Part Number
Manufacturer
Quantity
Price
Part Number:
pth03010WAS
Manufacturer:
TI/德州仪器
Quantity:
20 000
Company:
Part Number:
pth03010YAZ
Manufacturer:
Texas Instruments
Quantity:
135
7.5 Remote Sense
The PTHxx010W, PTHxx020W, and PTHxx030W products
incorporate an output voltage sense pin, V
pin should be connected to V
standard application). A remote sense improves the load regulation
performance of the module by allowing it to compensate for any ‘IR’
voltage drop between itself and the load. An IR drop is caused by
the high output current flowing through the small amount of pin and
trace resistance. Use of the remote sense is optional. If not used, the
Vout Sense pin can be left opencircuit. An internal low-value resistor
(15 Ω or less) is connected between the V
that the output voltage remains in regulation.
With the sense pin connected, the difference between the voltage
measured directly between the V
measured from V
compensated by the regulator. This should be limited to a maximum
of 0.3 V.
Note: The remote sense feature is not designed to compensate for
the forward drop of non-linear or frequency dependent components
that may be placed in series with the converter output. Examples
include OR-ing diodes, filter inductors, ferrite beads, and fuses.
When these components are enclosed by the remote sense
connection they are effectively placed inside the regulation control
loop, which can adversely affect the stability of the regulator.
1 1 0 0
Figure 11 - Margin Up/Down Application Schematic
GND
MargUp
V
MargDown
in
Table 6 - Margin Up/Down Resistor Values
C
in
+
out sense
Q
R
% ADJUST
1
D
Q
to GND, is the amount of IR drop being
R
2
u
5
4
3
2
1
out
1
2
File Name: an_pth03020.pdf Rev (05): 21 Dec 2005
at the load circuit (see datasheet
out
and GND pins, and that
PTH05020
(Top View)
10
3
150.0 kΩ
397.0 kΩ
24.9 kΩ
66.5 kΩ
0.0 kΩ
R
9
4
U
o
8
5
/R
R
o
SET
Sense and V
Sense. The V
D
0.1W, 1%
7
6
out
C
+V
0V
out
o
, ensures
o
Sense
+
GND
+V
out
L
O
A
D
8. Thermal Information
8.1 Thermal Reference Points
The electrical operating conditions namely:
• Input voltage, V
• Output voltage, V
• Output current, I
determine how much power is dissipated within the converter. The
following parameters further influence the thermal stresses
experienced by the converter:
• Ambient temperature
• Air velocity
• Thermal efficiency of the end system application
• Parts mounted on system PCB that may block airflow
• Real airflow characteristics at the converter location
8.2 Safe Operating Area Curve
Thermal characterisation data is presented in the datasheet in a safe
operating area curve format which is repeated here in Figure 12.
This SOA curve shows the load current versus the ambient air
temperature and velocity.
8.3 Thermal Test Set-up
All of the data was taken with the converter soldered to a test board
which closely represents a typical application. The test board is a
1.6 mm, eight layer FR4 PCB with the inner layers consisting of 2 oz
power and ground planes. The top and bottom layers contain a
minimal amount of metalisation. A board to board spacing of 1 inch
was used. The data represented by the 0 m/s curve indicate a
natural convection condition i.e. no forced air. However, since the
thermal performance is heavily dependent upon the final system
application, the user needs to ensure the thermal reference point
temperatures are kept within the recommended temperature rating.
It is recommended that the thermal reference point temperatures are
measured using either AWG #36 or #40 gauge thermocouples or an
IR camera. In order to comply with stringent Artesyn de-rating
criteria, the ambient temperature should never exceed 85 °C. Please
contact Artesyn Technologies for further support.
90
80
70
60
50
40
30
20
0 2
PTH03020 Single Series | Application Note 151
Figure 12 - Safe Operating Curve
4
in
o
o
OUTPUT CURRENT (A)
PTH03020W V out = 2.5 V
6
8 10 12
14
16 18 20 22
400 LFM
200 LFM
100 LFM
Nat conv