sc172mltrt Semtech Corporation, sc172mltrt Datasheet - Page 15
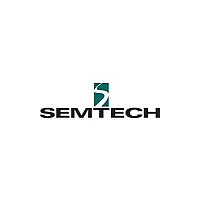
sc172mltrt
Manufacturer Part Number
sc172mltrt
Description
2a Ecospeed Synchronous Step-down Regulator With Optional Ultrasonic Power Save
Manufacturer
Semtech Corporation
Datasheet
1.SC172MLTRT.pdf
(27 pages)
Available stocks
Company
Part Number
Manufacturer
Quantity
Price
Applications Information (continued)
Design Procedure
When designing a switch mode supply the input voltage
range, load current, switching frequency, and inductor
ripple current must be specified.
The maximum input voltage (V
fied input voltage. The minimum input voltage ( V
determined by the lowest input voltage after evaluating
the voltage drops due to connectors, fuses, switches, and
PCB traces.
The following parameters define the design.
There are two values of load current to evaluate — con-
tinuous load current and peak load current. Continuous
load current relates to thermal stresses which drive the
selection of the inductor and input capacitors. Peak load
current determines instantaneous component stresses and
filtering requirements such as inductor saturation, output
capacitors, and design of the current limit circuit.
The following values are used in this design.
Frequency Selection
Selection of the switching frequency requires making a
trade-off between the size and cost of the external filter
components (inductor and output capacitor) and the
power conversion efficiency.
The desired switching frequency is 800kHz which results
from using components selected for optimum size and
cost .
A resistor (R
setting the frequency) using the following equation un-
© 2010 Semtech Corporation
•
•
•
•
•
•
•
•
Nominal output voltage (V
Static or DC output tolerance
Transient response
Maximum load current (I
V
V
f
Load = 2A maximum
SW
IN
OUT
= 5V + 10%
= 800kHz
= 1.0V + 4%
TON
) is used to program the on-time (indirectly
OUT
INMAX
OUT
)
)
) is the highest speci-
INMIN
) is
der zero load condition.
Since the f
R
to achieve 800kHz at full load.
Calculating R
R
Inductor Selection
In order to determine the inductance, the ripple cur-
rent must first be defined. Low inductor values result in
smaller size but create higher ripple current which can
reduce efficiency. Higher inductor values will reduce the
ripple current/voltage and for a given DC resistance are
more efficient. However, larger inductance translates di-
rectly into larger packages and higher cost. Cost, size,
output ripple, and efficiency are all used in the selection
process.
The ripple current will also set the boundary for power-
save operation. The switching will typically enter power-
save mode when the load current decreases to 1/2 of the
ripple current. For example, if ripple current is 1A then
power-save operation will typically start for loads less
than 0.5A. If ripple current is set at 40% of maximum load
current, then power-save will start for loads less than 20%
of maximum current.
The inductor value is typically selected to provide a rip-
ple current that is between 25% to 50% of the maximum
load current. This provides an optimal trade-off between
cost, efficiency, and transient performance.
During the DH on-time, voltage across the inductor is
(V
shown next.
TON
TON
IN
=22.2kW, we use R
- V
should be programmed at 600kHz under zero load
OUT
). The equation for determining inductance is
SW
R
may increase by about 100kHz per Ampere,
TON
TON
results in the following solution.
=
(
L
T
V
V
ON
TON
=
OUT
FB
(V
=22.1kW in real application.
=
)
IN
⋅
V
100pF
-
INMAX
I
V
RIPPLE
V
OUT
OUT
1
)
⋅
×
⋅
f
SW
f
T
SW
ON
SC172
15