tb6585fg TOSHIBA Semiconductor CORPORATION, tb6585fg Datasheet
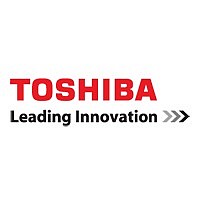
tb6585fg
Available stocks
Related parts for tb6585fg
tb6585fg Summary of contents
Page 1
... R-type flux (2) Use of Sn-3.0Ag-0.5Cu solder Bath · solder bath temperature = 245°C · dipping time = 5 seconds · the number of times = once · use of R-type flux TB6585FG = 0.5 V (typ.)) = 4 4.4 V (typ.), 20 mA (max) 1 TB6585FG Weight: 0.79 g (typ.) 2008-03-04 ...
Page 2
... Note: Pins 1 and 36 and pins 18 and 19 are respectively connected together on the frame inside the IC. The NC pin can be used as a jumper. The fin and the package bottom are electrically connected. To stabilize the chip, the Fin pins should be connected to S-GND and P-GND at a location as close to the TB6585FG as possible. ...
Page 3
... Shunt voltage input in Overcurrent protection input (Disables outputs when RS ≥ 0 P-GND Power ground 32 IR Connection pin for an output shunt resistor 33 W W-phase output 34 V V-phase output 35 U U-phase output Description = 4 4.4 V (typ.), (max)), refout refout 3 TB6585FG 2008-03-04 ...
Page 4
... When an input voltage of 3 higher is applied, the lead angle is clipped to a maximum of 28°. The LA pin should be left open when using the automatic-lead-angle control. At this time, the LA pin can be used for determining the lead angle. 4 TB6585FG Internal Circuit Diagram V V refout refout V refout 100 Ω ...
Page 5
... 4 upper-limit control When LL > UL fixed to the value determined by LL. I/O Signal G in output voltage − 0.4 V refout refout ) refout 5 TB6585FG Internal Circuit Diagram V refout 100 Ω − V refout 100 Ω V refout 100 Ω peak-hold circuitry V refout 100 Ω ...
Page 6
... RS The gate block protection is activated when RS reaches 0.5 V. (Disabled every carrier cycle) U Motor drive output U-phase, V-phase V I OUT and W-phase outputs W I/O Signal = 1.2 A (typ.) 1.8 A (max) 6 TB6585FG Internal Circuit Diagram V refout 100 Ω V refout 10 kΩ refout 200 kΩ Comparator ...
Page 7
... OUT 1.3 (Note 3.2 (Note 3) − opr °C −55 to 150 T stg jmax Symbol Min Typ. Max V 4 OSC P – 3.5 (3) 3 2.5 2 (2) 1.5 ( 100 125 Ambient Temperature Ta (°C) 7 TB6585FG = 150°C. Unit V MHz 150 2008-03-04 ...
Page 8
... Oscillation frequency 180 (H) Output start point M V (L) Output stop point M V Hysteresis width H OSC/C = 150 pF OSC kΩ F (5M) C TSD TSDhys Thermal shutdown hysteresis 8 TB6585FG Min Typ. ⎯ 7 ⎯ 22 ⎯ 30 ⎯ 44 ⎯ 1.5 ⎯ 50 ±4 ±8 (Note) −1 ⎯ V ⎯ 2.0 ⎯ ...
Page 9
... V sp Triangular wave (carrier voltage refout = Reference clock frequency (RC oscillator frequency) = 19.8 kHz c Automatic-lead-angle controller (typ.) 9 TB6585FG × 32 × MHz osc V refout Modulated waveform GND = V . The PWM duty SP refout is defined as 100%. 5-bit AD Modulated wave generator ...
Page 10
... Characteristics of the LA versus Lead Angle> Lead angle Step LA (V) (°) 1 0.00 0.00 2 0.09 0.94 3 0.19 1.88 4 0.28 2.81 5 0.38 3.75 6 0.47 4.69 7 0.56 5.63 8 0.66 6.56 9 0.75 7.5 10 0.84 8.44 11 0.94 9.38 12 1.03 10.31 13 1.13 11.25 14 1.22 12.19 15 1.31 13.13 16 1.41 14. 0.35 Lead angle Step LA (V) (° 1.59 15.94 19 1.69 16.88 20 1.78 17.81 21 1.88 18.75 22 1.97 19.69 23 2.06 20.63 24 2.16 21.56 25 2.25 22.50 26 2.34 23.44 27 2.44 24.38 28 2.53 25.31 29 2.63 26.25 30 2.72 27.19 31 2.81 28.13 32 2.91 29.06 LA (V) vs. Lead Angle (°) Characteristics 0.7 1.05 1.4 1.75 2.1 LA (V) 10 TB6585FG 2.45 2.8 3.15 2008-03-04 ...
Page 11
... The detection is performed at every electrical degree of 360°. CW/CCW Pin Actual Rotation Direction of the Motor Low (CW) CCW (counterclockwise) High (CCW) CCW (counterclockwise) Note: When the Hall signal frequency is below 2.5 Hz, the TB6585FG is put in 120° commutation mode even when 180° commutation mode is selected. IV pin Peak . Amp Gain × V Gain × ...
Page 12
... Example: When C 1 <Automatic Restart (ML = High)> When the Hall signal frequency is kept below 2.5 Hz for at least 500 ms (typ.), the TB6585FG becomes active and inactive periodically every 500 ms (typ.). The protection is disabled when the Hall signal frequency reaches 2.5 Hz and the operation mode is switched to 180° ...
Page 13
... CR System clock oscillation generator Power Supply Monitoring) M 3.5 V (typ.) Output: On Phase U Counter Phase V Sine waveform Comparator (modulated signal) Phase W Triangular wave (carrier frequency) 13 TB6585FG V M GND V M Output: Off Output U-phase power Output transistors V-phase Output (P-channel+ W-phase N-channel) Output 2008-03-04 ...
Page 14
... HW. Likewise, the modulated waveform (2)’ advances by 1/32 of the ) of HW and the rising edge ( (1)’ 32 data 14 TB6585FG *: Though the HUP, HVP and HWP pins are Hall effect inputs, they are indicated as square waveforms for the sake of simplicity HV. 2008-03-04 ...
Page 15
... In such cases, the modulated waveform is discontinuous at every reset ( ( Reset (1)’ 15 TB6585FG 2008-03-04 ...
Page 16
... Note: The above U-phase waveform shows the behavior of the U-phase output signal when a resistor is connected between the U and VM pins and also between the U pin and ground to obtain connected to the V and W pins. Modulated wave Carrier frequency V M indicates the high-impedance state TB6585FG Carrier frequency V (typ.) GND V GND V GND V ...
Page 17
... Hz < Hall signal frequency (180° commutation: Modulated wave inside the IC The lead-angle correction is performed in accordance with the LA input when the Hall signal frequency is 2 higher. The timing chart may be simplified for the sake of brevity. (CW/CCW = Low GND) 17 TB6585FG 2008-03-04 ...
Page 18
... If the Hall signal for counterclockwise rotation is applied when CW/CCW = Low, the motor is driven by the 120° commutation signal with a lead angle of 0°. (Reverse rotation by the wind) The timing chart may be simplified for the sake of brevity. (CW/CCW = Low GND) 18 TB6585FG 2008-03-04 ...
Page 19
... Hz < Hall signal frequency (180° commutation: Modulated wave inside the IC The lead-angle correction is performed in accordance with the LA input when the Hall signal frequency is 2 higher. The timing chart may be simplified for the sake of brevity. (CW/CCW = High GND) 19 TB6585FG 2008-03-04 ...
Page 20
... If the Hall signal for clockwise rotation is applied when CW/CCW = High, the motor is driven by the 120° commutation signal with a lead angle of 0°. (Reverse rotation by the wind) The timing chart may be simplified for the sake of brevity. (CW/CCW = High GND) 20 TB6585FG 2008-03-04 ...
Page 21
... TB6585FG V V refout refout Upper limit Lower limit V (Note Pin TSD (165° Fin S-GND P-GND pin at a location as close to the refout pin at a location as close to the TB6585FG M 2008-03-04 (Note 3) ...
Page 22
... Package Dimensions Weight: 0.79 g (typ.) 22 TB6585FG 2008-03-04 ...
Page 23
... Otherwise, the current or power consumption may exceed the absolute maximum rating, and exceeding the rating(s) may cause the device breakdown, damage or deterioration, and may result injury by explosion or combustion. In addition, do not use any device that is applied the current with inserting in the wrong orientation or incorrectly even just one time. 23 TB6585FG 2008-03-04 ...
Page 24
... If the current sink capability of the power supply is small, the device’s motor power supply and output pins might be exposed to conditions beyond maximum ratings. To avoid this problem, take the effect of back-EMF into consideration in system design. 24 TB6585FG 2008-03-04 ...
Page 25
... Please use this product in compliance with all applicable laws and regulations that regulate the inclusion or use of controlled substances. Toshiba assumes no liability for damage or losses occurring as a result of noncompliance with applicable laws and regulations. 060819_AF • The products described in this document are subject to foreign exchange and foreign trade control laws. 021023_D 021023_B 060106_Q 25 TB6585FG 070122EBA_R6 060925_E 2008-03-04 ...