hip9010 Intersil Corporation, hip9010 Datasheet - Page 6
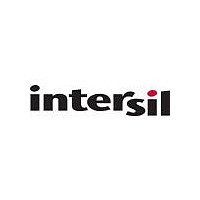
hip9010
Manufacturer Part Number
hip9010
Description
Engine Knock Signal Processor
Manufacturer
Intersil Corporation
Datasheet
1.HIP9010.pdf
(12 pages)
Available stocks
Company
Part Number
Manufacturer
Quantity
Price
Company:
Part Number:
hip9010AB
Manufacturer:
HAR
Quantity:
550
Company:
Part Number:
hip9010AB
Manufacturer:
HARRIS
Quantity:
10
Part Number:
hip9010AB
Manufacturer:
HAR
Quantity:
20 000
Part Number:
hip9010ABT
Manufacturer:
INTERSIL
Quantity:
20 000
Company:
Part Number:
hip9010ABTS2457
Manufacturer:
INTERSIL
Quantity:
4 000
Part Number:
hip9010ABZT
Manufacturer:
INTERSIL
Quantity:
20 000
Description of the HIP9010 Operation
This IC is designed to be a universal digitally controlled,
analog interface between engine acoustical sensors or
accelerometers and internal combustion engine fuel
management systems. Two wideband input amplifiers are
provided that allow the use of two sensors that may be of the
piezoelectric type that can be mounted in optimum locations
on either in-line or V-type engine configurations.
Output from these amplifiers is directed from a channel
select switch into both digitally controlled filter and amplifier
channels. Both filter bandpass and gain settings are
programmable from a microprocessor. Output from the two
channels is combined in a digitally programmable integrator.
Integrator output is applied to a line driver for further
processing by the engine fuel management system.
Broadband piezoelectric ceramic transducers used for the
engine signal pickup have device capacitances in the order
of 1100pF and output voltages that range from 5mV to
8V
channel is selected and applied to the filters. One filter
channel processes a signal that is used to establish the
background reference level. The second channel is used to
observe the engine during the time interval that preignition
may be expected. This information is compared with the
“background” signal via the IC’s integrator and will tend to
cancel the background noise and accentuate noise due to
engine pre-detonation. Moreover, the bandpass of filter
channels can be optimized to further discriminate between
engine background and combustion noise and
pre-detonation noise.
A basic approach to engine pre-detonation systems is to only
observe engine background during the time interval that noise
is expected and if detected, retard timing. This approach does
not require the sensitivity and selectivity that is needed for a
continuously adjustable solution. Enhanced fuel economy and
performance is obtainable when this IC is coupled with a
microprocessor controlled fuel management system.
Circuit Block Description
Input Amplifiers
Two amplifiers are used to interface to the two engine
sensors. These amplifiers have a typical open loop gain of
100dB, with a typical bandwidth of 2.6MHz. The common
mode input voltage range extends to within 0.5V of either
supply rail. The amplifier output has a similar output range.
Sufficient gain, bandwidth and output swing capability was
provided to ensure that the amplifiers can handle attenuation
gain settings of 20 to 1 or -26dB. This would be needed
when high peak output signals, in the range of 8V
obtained from the transducer. Gain settings of 10 times can
also be needed when the transducers have output levels of
5mV
RMS.
RMS
During normal engine operation a single input
.
4-6
RMS
, are
HIP9010
In a typical application the input signal frequency may vary
from DC to 20kHz. External capacitors are used to decouple
the IC from the sensor (C1 and C2). A typical value of the
capacitors is 3.3nF. Series input resistors, R1 and R2, are
used to connect the inverting inputs of the amplifiers, (pins
20 and 17). Feedback resistors, R3 and R4, in conjunction
with R1 and R2 are used to set the gain of the amplifiers.
A mid-voltage level is generated by the IC. This level is set to
be half way between V
this level is used as a quiet, DC reference for the circuits
within the IC. This point is brought out for several reasons: it
can be used as a reference voltage, and it must be bypassed
to ensure that it is a quiet reference for the internal circuitry.
The input amplifiers are designed with power down capability,
which, when activated disables their bias circuit and their
output goes into a three-state condition. This is very important
during the test mode, in which the output terminals of the
amplifiers are driven by the outside world with test signals.
Antialiasing Filter
The IC has a 3rd order Butterworth filter with a -3dB point at
70kHz. Double poly-silicon capacitors and implanted
resistors are used to set poles in the filter. This filter is
required to have no more than 1dB attenuation at 20kHz
(highest frequency off interest) and a minimum attenuation
of 10dB at 180kHz. This filter precedes the switch capacitor
filters which run at 200kHz.
Programmable Band Pass Switched Capacitor Filters
Two identical programmable filters are used to detect the two
frequencies of interest. The Knock Frequency Filter is
programmed to pass the frequency component of the engine
knock. The Reference Frequency Filter is used to detect
background noise at a second programmed frequency. The filter
frequency is established by the characteristics of the particular
engine and transducer. By subtracting the energy component of
these two filters, we can detect if a knock has occurred.
The filters have a nominal differential gain of 4. Their
frequency is set by program words (discussed in the
Communications Protocol section). Center frequencies can
be programmed from 1.22kHz to 19.98kHz, in 64 steps. The
filter Qs are typically 2.4.
FIGURE 3. INPUT AMPLIFIER CONNECTIONS
SENSOR
SENSOR
0
1
C1
C2
DD
V
V
R1
R2
MID
MID
and ground. Throughout the IC
PIN 20
PIN 17
PIN 3
PIN 3
-
+
-
+
R3
R4
PIN 19
PIN 18