FT18 Philips Semiconductors, FT18 Datasheet - Page 11
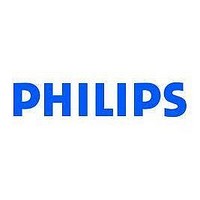
FT18
Manufacturer Part Number
FT18
Description
Frame Transfer CCD Image Sensor
Manufacturer
Philips Semiconductors
Datasheet
1.FT18.pdf
(16 pages)
Available stocks
Company
Part Number
Manufacturer
Quantity
Price
Part Number:
FT1869
Manufacturer:
ST/MOTO
Quantity:
20 000
Part Number:
FT1881
Manufacturer:
ST/MOTO
Quantity:
20 000
Philips Semiconductors
Application information
Current handling
One of the purposes of VPS is to drain the holes that are generated
during exposure of the sensor to light. Free electrons are either
transported to the VRD connection and, if excessive (from over-
exposure), free electrons are drained to VNS. No current should
flow into any VPS connection of the sensor. During high overexposure
a total current 10 to 15mA through all VPS connections together
may be expected. The PNP emitter follower in the circuit diagram
(figure 6) serves these current requirements.
VNS drains superfluous electrons as a result of overexposure. In
other words, it only sinks current. During high overexposure a total
current of 10 to 15mA through all VNS connections together may be
expected. The NPN emitter follower in the circuit diagram meets
these current requirements.
Decoupling of DC voltages
All DC voltages should be decoupled with a 100nF decoupling
capacitor. This capacitor must be mounted as close as possible to
the sensor pin. Further noise reduction (by bandwidth limiting) is
achieved by the resistors in the connections between the sensor
and its voltage supplies. The electrons that build up the charge
packets that will reach the floating diffusions only add up to a small
current, which will flow through VRD. Therefore a large series resistor
in the VRD connection may be used.
Outputs
To limit the on-chip power dissipation, the output buffers are designed
with open source outputs. Outputs to be used should therefore be
loaded with a current source or more simply with a resistance to
GND. In order to prevent the output (which typically has an output
impedance of about 400 ) from bandwidth limitation as a result of
capacitive loading, load the output with an emitter follower built from
2000 January
Frame Transfer CCD Image Sensor
11
a high-frequency transistor. Mount the base of this transistor as close
as possible to the sensor and keep the connection between the
emitter and the next stage short. The CCD output buffer can easily
be destroyed by ESD. By using this emitter follower, this danger is
suppressed; do NOT reintroduce this danger by measuring directly
on the output pin of the sensor with an oscilloscope probe. Instead,
measure on the output of the emitter follower. Slew rate limitation is
prevented by avoiding a too-small quiescent current in the emitter
follower; about 10mA should do the job. The collector of the emitter
follower should be decoupled properly to suppress the Miller effect
from the base-collector capacitance.
A CCD output load resistor of 3.3k
of 110MHz. The bandwidth can be enlarged to about 130MHz by
using a resistor of 2.2k instead, which, however, also enlarges the
on-chip power dissipation.
Device protection
The output buffers of the FT 18 are likely to be damaged if VPS
rises above SFD or RD at any time. This danger is most realistic
during power-on or power-off of the camera. The RD voltage should
always be lower than the SFD voltage.
Never exceed the maximum output current. This may damage the
device permanently. The maximum output current should be limited
to 6mA.
Be especially aware that the output buffers of these image sensors
are very sensitive to ESD damage.
Because of the fact that our CCDs are built on an n-type substrate,
we are dealing with some parasitic npn transistors. To avoid activation
of these transistors during switch-on and switch-off of the camera,
we recommend the application diagram of figure 6.
typically results in a bandwidth
Product specification
FT 18