SC2447 Semtech Corporation, SC2447 Datasheet - Page 19
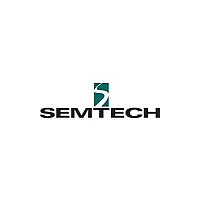
SC2447
Manufacturer Part Number
SC2447
Description
Dual-Phase Single or Two Output Synchronous Step-Down Controller
Manufacturer
Semtech Corporation
Datasheet
1.SC2447.pdf
(26 pages)
For reliable operation, the maximum power dissipation
in the capacitors should not result in more than 10
temperature rise. Many manufacturers specify the
maximum allowable ripple current (ARMS), rating of the
capacitor at a given ripple frequency and ambient
temperature. The input capacitance should be large
enough to handle the ripple current. For higher power
applications, multiple capacitors are placed in parallel to
increase the ripple current handling capability.
Sometimes meeting tight input voltage ripple
specifications may require the use of larger input
capacitance. At full load, the peak-to-peak input voltage
ripple due to the ESR is
The peak-to-peak input voltage ripple due to the capacitor
is
From these two expressions, C
the input voltage ripple specification. In a multi-phase
converter, interleaved switching reduces ripple. The two
step-down channels of the SC2447 operate at 180 degrees
from each other. If both step-down channels in the SC2447
are connected in parallel, both the input and the output
RMS currents will be reduced.
Ripple cancellation effect of interleaving allows the use
of smaller input capacitors. When converter outputs are
connected in parallel and interleaved, a smaller inductor
and capacitor can be used for each channel. The total
output ripple-voltage remains unchanged. The use of a
smaller inductor helps speed up the output load
transient.
When two channels with a common input are interleaved,
the combined input current waveform depends on the duty
ratios and the output currents of both channels. Assuming
that the output current ripple is small, the following formula
can be used to estimate the RMS ripple current in the
input capacitor.
Let the duty ratio and output current of Channel 1 and
Channel 2 be D
POWER MANAGEMENT
Application Information (Cont.)
2006 Semtech Corp.
∆
1
, D
v
ESR
2
and I
=
∆
R
v ≈
esr
C
1 (
o1
, I
+
C
DI
in
o2
δ
2
o
f
, respectively.
IN
)
s
I
,
o
can be found to meet
.
o
C of
19
If D
Choosing Power MOSFETs
Power MOSFETs with integrated gate drivers such as
PIP212, R2J20601NP, PIP202, PIP201 and IP2001,
IP2002 are suitable for SC2447 application.
Current Sensing
Inductor current sensing is required for the current-mode
control. Although the inductor current can be sensed
with a precision resistor in series with the inductor, the
lossless inductive current sense technique can be used
in the SC2447. This technique has the advantages of,
1) lossless current sensing
2) lower cost compared to resistive sensing
3) more accurate compared to R
The basic arrangement of the inductive current sense is
shown in Figure 13.
R
R
In steady state, the DC voltage across R
Notice that the DC value of V
values of L, R
average load current information is needed (such as in
L
s
Figure 13. The Basic Structure of Inductive Current
Vin
is the equivalent series resistance of the output inductor.
and C
1
<0.5 and D
s
form a RC network for inductor current sensing.
Cin
I
Cin
s
2
and C
<0.5, then
≈
Q1
Q2
D
1
I
iL(t)
V
s
o
CS
. This means that, if only the
1
2
Sense
+
= R
D
L
Rs
2
I
L
o
2
I
Cs
www.DataSheet4U.com
2
O
.
RL
Cs
vC(t)
.
DS(ON)
is independent of the
sensing
L
is
www.semtech.com
Cout
SC2447
Rload
Vo