NCV7680 ON Semiconductor, NCV7680 Datasheet - Page 13
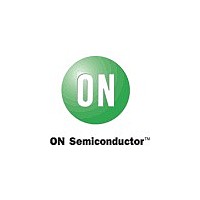
NCV7680
Manufacturer Part Number
NCV7680
Description
Linear Current Regulator and Controller
Manufacturer
ON Semiconductor
Datasheet
1.NCV7680.pdf
(20 pages)
Available stocks
Company
Part Number
Manufacturer
Quantity
Price
Company:
Part Number:
NCV7680PWR2G
Manufacturer:
ON
Quantity:
1 000
Company:
Part Number:
NCV7680PWR2G
Manufacturer:
ON Semiconductor
Quantity:
440
Programmability
applications. The NCV7680 provides eight matched outputs
allowing individual string drive with current set by a single
resistor. Individual string drive is a benefit to ensure equal
current distribution amongst all of the strings. Output
currents are mirrored and matched within ±5% at hot
temperature.
equation 1 below.
a duty cycle (DC) programmed using equation 2 below.
can be referenced from the RSTOP Pin. Exceeding the
R
DIAG Pin will go high (reference Figure 18). This helps
limit output current (brightness and power) for this type of
fault.
dimmed tail illumination function and assures a fixed
brightness level for tail. The PWM generator’s fixed
frequency (1 kHz typ.) oscillator allows flicker−free
illumination. PWM control is the preferred method for
dimming LEDs.
any one of the output circuits. The active−low diagnostic
output (DIAG) is coincident with the STOP input. DIAG
remains high (pulled up) if an open load is detected in any
LED string when STOP is high.
Output Current Programming
(R
Cycle vs. R
resistor for output duty cycle (with a typical R
3.09 kW). Note the duty cycle is dependent on both R
STOP
Strings of LEDs are a common configuration for RCL
A high STOP condition sets the output current using
A low STOP condition, modulates the output currents at
Note, current limiting on R
The average I
The diagnostic function allows the detection of an open in
Reference Figure 10 to choose programming resistor
STOP
Current Limit will reduce the output current and the
) value for stop current. Reference Figure 12 (Duty
V
bat
TAIL
) to choose a typical value programming
STOP
MRA4003T3G
Duty Cycle current provides the
0.1 mF
STOP
C1
limits the current which
Figure 21. Alternative V
R3
1K
STOP
NTD2955
Rsd
0.22 mF
value of
http://onsemi.com
C2
STOP
13
P
Connection with Rsd
and R
stop current is only dependent on this value.
a typical value and used for worst case analysis.
Set the Stop Current using R
Set the Duty Cycle (DC) using R
parameter table to be ±10% (with R
31.5 mA (min), 35 mA (typ), 38.5 mA (max) at room and hot
temperature.
Voltage and R
through R
and comparator errors and are included in testing as the Duty
Cycle. Typical duty cycle measurements are 5% with R
= 0.59 V and 70% with R
Current and vary as 300 mA (min), 350 mA (typ), and 450 mA
(max) with R
difficult to specify duty cycle minimum and maximum
limits, but worst case conditions can be calculated when
considering the variation in the voltage threshold and
current source. Duty Cycle variation must include the direct
DC = duty cycle expressed in fractional form.
(e.g. 0.50 is equivalent to 50% duty cycle)
R
(ground R
C3
100 nF
Alternatively, the equations below can be used to calculate
Output Current is directly tested per the electrical
Duty Cycle will vary according to the changes in R
Voltage errors encompass generator errors (0.4 V to 4.4 V)
R
The error duality and choice of duty cycle levels make it
STOP
TAIL
TAIL
Bias Voltage = 1.08 V (typ)
OUTX + 100
R
Bias Current errors are measured as R
TAIL
TAIL
STOP
values. R
STOP
when using external modulation)
TAIL
+ 4
).
OUT1
V
Ballast Drive
FB
STOP
DIAG
R
R
feedback
I
Bias Current (generated form the current
P
STOP
TAIL
= 3.09 kW.
LEDs
STOP
R
STOP
&
NCV7680
should always be chosen first as the
R
TAIL
STOP_Bias_Voltage
(DC ) 0.1)
R
= 3.29 V.
STOP
STOP
OUT2
OUT3
OUT4
OUT5
OUT6
OUT7
OUT8
GND
TAIL
STOP
www.DataSheet4U.com
= 3.09 kW) or
TAIL
(eq. 1)
(eq. 2)
Bias
TAIL
TAIL