BD63847EFV Rohm, BD63847EFV Datasheet - Page 4
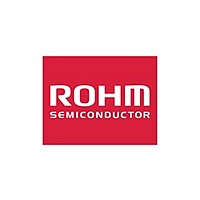
BD63847EFV
Manufacturer Part Number
BD63847EFV
Description
(BD63843EFV / BD63847EFV) Micro step 36V Stepping Motor Drivers
Manufacturer
Rohm
Datasheet
1.BD63847EFV.pdf
(9 pages)
●Points to notice for terminal description
●Protection Circuits
www.rohm.com
© 2012 ROHM Co., Ltd. All rights reserved.
BD63843EFV, BD63847EFV
○CLK/Clock input terminal for advancing the electrical angle
○MODE0,MODE1/Motor excitation mode setting terminal
○CW_CCW /Motor rotating direction setting terminal
○Thermal Shutdown (TSD)
○Over Current Protection (OCP)
○ENABLE/Output enable terminal
○PS/Power save terminal
This IC has a built-in thermal shutdown circuit for thermal protection. When the IC’s chip temperature rises above 175°C
(Typ.), the motor output becomes OPEN. Also, when the temperature returns to under 150°C (Typ.), it automatically returns
to normal operation. However, even when TSD is in operation, if heat is continued to be added externally, heat overdrive
can lead to destruction.
This IC has a built in over current protection circuit as a provision against destruction when the motor outputs are shorted
each other or VCC-motor output or motor output-GND is shorted. This circuit latches the motor output to OPEN condition
when the regulated threshold current flows for 4µs (Typ.). It returns with power reactivation or a reset of the PS terminal.
The over current protection circuit’s only aim is to prevent the destruction of the IC from irregular situations such as motor
output shorts, and is not meant to be used as protection or security for the set. Therefore, sets should not be designed to
take into account this circuit’s functions. After OCP operating, if irregular situations continues and the return by power
reactivation or a reset of the PS terminal is carried out repeatly, then OCP operates repeatly and the IC may generate heat
or otherwise deteriorate. When the L value of the wiring is great due to the wiring being long, after the over current has
flowed and the output terminal voltage jumps up and the absolute maximum values may be exceeded and as a result, there
is a possibility of destruction. Also, when current which is over the output current rating and under the OCP detection
current flows, the IC can heat up to over Tjmax=150°C and can deteriorate, so current which exceeds the output rating
should not be applied.
CLK is reflected at rising edge. The Electrical angle advances by one for each CLK input.Motor’s misstep will occur if
noise is picked up at the CLK terminal, so please design the pattern in such a way that there is no noise plunging.
Set the step mode.
Set the motor’s rotating direction. Change in setting is reflected at the CLK rising edge immediately after the change in
setting
Turn off forcibly all the output transistors (motor output is open).
At ENABLE=L, electrical angle or operating mode is maintained even if CLK is inputted.
If step modes are changed during ENABLE=L, new step mode is carried out at ENABLE=L to H
PS can make circuit standby state and make motor output OPEN. In standby state, translator circuit is reset (initialized)
and electrical angle is initialized.
Please be careful because there is a delay of 40µs(max.) before it is returned from standby state to normal state and the
motor output becomes ACTIVE
The electrical angle (initial electrical angle) of each step mode immediately after RESET is as follows
MODE0
CW_CCW
ENABLE
Step mode
H
H
L
L
1/16 step
Half step
Full step
1/8 step
PS
H
H
H
L
L
L
MODE1
Clockwise (CH2’s current is outputted with a phase lag of 90°in regard to CH1’s current)
Counter Clockwise(CH2’s current is outputted with a phase lead of 90°in regard to CH1’s current)
H
H
L
L
OPEN (electrical angle maintained)
Initial electrical angle
Standby state (RESET)
Motor output
45°
45°
45°
45°
ACTIVE
ACTIVE
State
Step mode
1/16 step
Half step
Full step
1/8 step
4/8
Rotating direction
www.DataSheet.co.kr
Technical Note
2012.02 - Rev.A
Datasheet pdf - http://www.DataSheet4U.net/