MAX1887 Maxim Integrated Products, MAX1887 Datasheet - Page 15
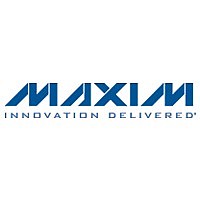
MAX1887
Manufacturer Part Number
MAX1887
Description
(MAX1887 / MAX1897) Quick-PWM Slave Controllers
Manufacturer
Maxim Integrated Products
Datasheet
1.MAX1887.pdf
(33 pages)
Available stocks
Company
Part Number
Manufacturer
Quantity
Price
Company:
Part Number:
MAX1887EEE
Manufacturer:
MAXIM
Quantity:
6 237
Part Number:
MAX1887EEE
Manufacturer:
MAXIM/美信
Quantity:
20 000
prevent the on times from overlapping. Therefore, the
instantaneous input current peaks of each phase do
not overlap, resulting in reduced input and output volt-
age ripple and RMS ripple current. This lowers the
input and output capacitor requirements, which allows
fewer or less expensive capacitors, and decreases
shielding requirements for EMI. When the on-times
overlap at low input-to-output differential voltages (V
<
may sum together, increasing the total input and output
ripple voltage and RMS ripple current.
During in-phase operation, the input capacitors must
support large, instantaneous input currents when the
high-side MOSFETs turn on simultaneously, resulting in
increased ripple voltage and current when compared
to out-of-phase operation. The higher RMS ripple cur-
rent degrades efficiency due to power loss associated
with the input capacitor’s effective series resistance
(ESR). This typically requires a large number of low-
ESR input capacitors in parallel to meet input ripple
current ratings or minimize ESR-related losses.
For the MAX1897, the polarity select input (POL) deter-
mines whether rising edges (POL = V
edges (POL = GND) trigger a new cycle. For low duty-
cycle applications (duty factor < 50%), triggering on
the rising edge of the master’s low-side gate driver pre-
vents both high-side MOSFETs from turning on at the
same time. Staggering the phases in this way lowers
the input ripple current, thereby reducing the input
capacitor requirements. For applications operating with
approximately a 50% duty factor, out-of-phase opera-
tion (POL = V
plete an on-pulse coincident to the master controller
determining when to initiate its next on-time. The noise
generated when the slave controller turns off its high-
side MOSFET could compromise the master controller’s
feedback voltage and current-sense inputs, causing
inaccurate decisions that lead to more jitter in the
switching waveforms. Under these conditions, trigger-
ing off of the falling edge (POL = GND) of the master’s
low-side gate driver forces the controllers to operate in-
phase, improving the system’s noise immunity.
The MAX1887/MAX1897 controllers do not allow light-
load pulse skipping. Therefore, the master controller
must be configured for forced-PWM operation. This
PWM control scheme forces the low-side gate drive
waveform to be the complement of the high-side gate
drive waveform, allowing the inductor current to
reverse. During negative load and downward output
voltage transitions, forced-PWM operation allows the
converter to sink current, rapidly pulling down the out-
η
V
OUT
), the input currents of the overlapping phases
CC
) causes the slave controller to com-
______________________________________________________________________________________
Forced-PWM Mode
Quick-PWM Slave Controllers for
Multiphase, Step-Down Supplies
CC
) or falling
IN
put voltage. Another benefit of forced-PWM operation,
the switching frequency remains relatively constant
over the full load and input voltage ranges.
The MAX1887/MAX1897 require an external 5V bias
supply in addition to the battery. Typically this 5V bias
supply is the notebook’s 95% efficient 5V system sup-
ply. Keeping the bias supply external to the IC
improves efficiency, eliminates power dissipation limita-
tions, and removes the cost associated with the inter-
nal, 5V linear regulator that would otherwise be needed
to supply the PWM circuit and gate drivers. If stand-
alone capability is needed, the 5V supply can be gen-
erated with an external linear regulator.
The 20-pin MAX1897 has a separate analog PWM sup-
ply voltage input (V
(V
PWM supply voltage input and the gate-driver supply
voltage input are internally connected and named V
The battery input (V+) and 5V bias inputs (V
V
4.5V to 5.5V supply.
The maximum current required from the 5V bias supply
to power V
power) is:
where I
frequency, and Q
sheets’ total gate charge specification limits at
V
When SHDN is driven low, the MAX1897 enters the
micropower shutdown mode (Table 3). Shutdown
immediately forces DL high, pulls DH low, and shuts
down the PWM controller so the total supply current
(I
ven high, the MAX1897 operates normally with the
PWM controller enabled.
Table 3. Approximate K-Factor Errors
*The MAX1887 is internally preset for 300kHz operation.
CONNECTION
DD
I
GS
CC
BIAS
DD
(MAX1897)*
) can be tied together if the input source is a fixed
= 5V.
+ I
). For the 16-pin MAX1887 device, the analog
Float
GND
TON
V
= I
CC
DD
CC
CC
+ I+) drops below 1µA. When SHDN is dri-
CC
is 525µA typical, f
+ f
(PWM controller) and V
SW
FREQUENCY
5V Bias Supply (V
SETTING
(Q
G1
(kHz)
200
300
550
CC
G1
Shutdown (MAX1897 only)
and Q
) and gate-driver supply input
+ Q
G2
G2
K-FACTOR
) = 10mA to 45mA (typ)
are the MOSFET data
(µs)
3.3
1.8
SW
5
is the switching
CC
DD
K-FACTOR
and V
(gate-drive
ERROR
MAX
(%)
10
10
10
CC
DD
and
DD
15
)
.