MAX16903 Maxim Integrated Products, MAX16903 Datasheet - Page 10
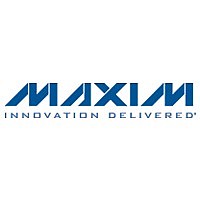
MAX16903
Manufacturer Part Number
MAX16903
Description
1A Mini-Buck Converter
Manufacturer
Maxim Integrated Products
Datasheet
1.MAX16903.pdf
(13 pages)
Available stocks
Company
Part Number
Manufacturer
Quantity
Price
Company:
Part Number:
MAX16903RAUE33/V+
Manufacturer:
Maxim Integrated Products
Quantity:
1 846
Company:
Part Number:
MAX16903RAUE50/V+
Manufacturer:
Maxim Integrated Products
Quantity:
1 004
Part Number:
MAX16903SA50
Manufacturer:
MAXIM/美信
Quantity:
20 000
Part Number:
MAX16903SATB50/V+T
Manufacturer:
MAXIM/美信
Quantity:
20 000
Company:
Part Number:
MAX16903SAUE33+T
Manufacturer:
MAXIM
Quantity:
17
Company:
Part Number:
MAX16903SAUE50+T
Manufacturer:
MAXIM
Quantity:
17
D a t a S h e e t . i n
2.1MHz, High-Voltage, 1A Mini-Buck Converter
where:
and
where I
and f
input capacitance at lower input voltages to avoid pos-
sible undershoot below the UVLO threshold during tran-
sient loading.
The allowable output-voltage ripple and the maximum
deviation of the output voltage during step load cur-
rents determine the output capacitance and its ESR.
The output ripple comprises of ∆V
capacitor discharge) and ∆V
the output capacitor). Use low-ESR ceramic or alu-
minum electrolytic capacitors at the output. For alu-
minum electrolytic capacitors, the entire output ripple is
contributed by ∆V
culate the ESR requirement and choose the capacitor
accordingly. If using ceramic capacitors, assume the
contribution to the output ripple voltage from the ESR
and the capacitor discharge to be equal. The following
equations show the output capacitance and ESR
requirement for a specified output-voltage ripple.
where:
∆I
above and f
The allowable deviation of the output voltage during
fast transient loads also determines the output capaci-
tance and its ESR. The output capacitor supplies the
step load current until the converter responds with a
10
P-P
______________________________________________________________________________________
SW
is the peak-to-peak inductor current as calculated
OUT
is the switching frequency. Use additional
SW
is the output current, D is the duty cycle,
V
∆I
∆I
OUT RIPPLE
P P
P P
C
is the converter’s switching frequency.
−
−
OUT
ESR
_
ESR
=
=
. Use the ESR
(
(
=
D
V
V
IN
IN
8
=
=
V
V
×
−
IN
−
IN
V
∆
∆
∆
≅ ≅
OUT
V
∆
V
V
V
I
P P
V
×
IN
ESR
OUT
OUT
ESR
I
∆
×
P P
Q
−
V
f
−
SW
f
SW
ESR
×
(caused by the ESR of
)
)
Output Capacitor
f
SW
×
×
×
×
OUT
+
V
V
L
Q
OUT
L
∆
OUT
V
(caused by the
equation to cal-
Q
greater duty cycle. The response time (t
depends on the closed-loop bandwidth of the convert-
er. The high switching frequency of the MAX16903
allows for a higher closed-loop bandwidth, thus reduc-
ing t
ment. The resistive drop across the output capacitor’s
ESR and the capacitor discharge causes a voltage
droop during a step load. Use a combination of low-
ESR tantalum and ceramic capacitors for better tran-
sient load and ripple/noise performance. Keep the
maximum output-voltage deviations below the tolerable
limits of the electronics being powered. When using a
ceramic capacitor, assume an 80% and 20% contribu-
tion from the output capacitance discharge and the
ESR drop, respectively. Use the following equations to
calculate the required ESR and capacitance value:
where I
response time of the converter. The converter response
time depends on the control-loop bandwidth.
Careful PCB layout is critical to achieve low switching
power losses and clean stable operation. Use a multilayer
board wherever possible for better noise immunity. Refer
to MAX16903 Evaluation Kit for recommended PCB lay-
out. Follow these guidelines for a good PCB layout:
1) The input capacitor (4.7µF, see the applications
2) Solder the exposed pad to a large copper plane
3) Isolate the power components and high current
schematic in the Typical Operating Circuits ) should be
placed right next to the SUP pins (pins 2 and 3 on the
TSSOP-EP package) of the MAX16903. Since the
MAX16903 operates at 2.1MHz switching frequency,
this placement is critical for effective decoupling of
high-frequency noise from the SUP pins.
area under the device. To effectively use this copper
area as heat exchanger between the PCB and ambi-
ent expose the copper area on the top and bottom
side. Add a few small vias or 1 large via on the cop-
per pad for efficient heat transfer. Connect the
exposed pad to PGND ideally at the return terminal
of the output capacitor.
paths from sensitive analog circuitry.
RESPONSE
STEP
C
is the load step and t
OUT
and the output capacitance require-
ESR
=
I
STEP
OUT
PCB Layout Guidelines
=
×
∆
∆
I
STEP
t
V
V
RESPONSE
Q
ESR
RESPONSE
RESPONSE
is the
)