NCP1015 ON Semiconductor, NCP1015 Datasheet - Page 10
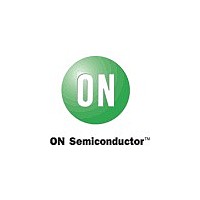
NCP1015
Manufacturer Part Number
NCP1015
Description
Self-supplied Monolithic Switcher For Low Standby-power Offline Smps W/out Ovp
Manufacturer
ON Semiconductor
Datasheet
1.NCP1015.pdf
(22 pages)
Available stocks
Company
Part Number
Manufacturer
Quantity
Price
Part Number:
NCP1015AP065G
Manufacturer:
ON/安森美
Quantity:
20 000
Company:
Part Number:
NCP1015AP100G
Manufacturer:
FREESCALE
Quantity:
9 100
Part Number:
NCP1015AP100G
Manufacturer:
ON/安森美
Quantity:
20 000
Part Number:
NCP1015ST100T3G
Manufacturer:
ON/安森美
Quantity:
20 000
Part Number:
NCP1015ST65T3G
Manufacturer:
ON/安森美
Quantity:
20 000
to <V
370 Vdc. With ICC1 = 1.2 mA (65 kHz version), we can
expect a DSS dissipation around 440 mW. If you select a
higher switching frequency version, the ICC1 increases and
it is likely that the DSS consumption exceeds 500 mW. In
that case, we recommend adding an auxiliary winding in
order to offer more dissipation room to the power MOSFET.
power capability of the NCP101X members” to help
selecting the right part / configuration for your application.
Lowering the Standby Power with an Auxiliary
Winding
dissipation is too high b) extremely low standby power is a
must. In both cases, one can connect an auxiliary winding to
disable the self-supply. The current source then ensures the
startup sequence only and stays in the off state as long as
V
that the insertion of a resistor (R
dc level and the V
internal 8.7 V zener diode during an overshoot for instance
(absolute maximum current is 15 mA) b) to implement the
fail-safe optocoupler protection as offered by the active
clamp. Please note that there cannot be bad interaction
between the clamping voltage of the internal zener and
V
of V
applications often puzzles the designer. Actually, if a SMPS
operated at nominal load can deliver an auxiliary voltage of
an arbitrary 16 V (V
10 V (V
recurrence of the switching pulses expands so much that the
low frequency re-fueling rate of the V
enough to keep a proper auxiliary voltage. Figure 18 shows
a typical scope shot of a SMPS entering deep standby
(output un-loaded). So care must be taken when calculating
R
operation but 2) not to drop too much voltage over R
when entering standby. Otherwise the DSS could reactivate
and the standby performance would degrade. We are thus
able to bound R
limit
CC
CC(off)
Plugging Equation 7 and Equation 8 into Equation 6 leads
The worse case occurs at high line, when V
Please read application note AND8125/D “Evaluating the
The DSS operation can bother the designer when a) its
Self-supplying controllers in extremely low standby
CC(off)
does not drop below V
ds(t)
1) to not excess the maximum pin current in normal
stby
since this clamping voltage is actually built on top
> = V
with a fixed amount of offset (200 mV typical).
) when entering standby. This is because the
in
limit
and thus:
CC
P
between two equations:
pin is mandatory a) not to damage the
nom
DSS
), this voltage can drop to below
+ V
CC(on)
in
limit
@ ICC1
or 7.5 V. Figure 17 shows
) between the auxiliary
CC
capacitor is not
in
http://onsemi.com
(eq. 9)
equals
limit
NCP1015
10
Where:
V
V
I
It thus must be selected to avoid false tripping in overshoot
conditions.
ICC1 is the controller consumption. This number slightly
decreases compared to ICC1 from the spec since the part in
standby does almost not switch.
V
to keep the DSS in the OFF mode. It is good to shoot around
8 V in order to offer an adequate design margin, e.g. to not
re-activate the startup source (which is not a problem in
itself if low standby power does not matter)
keep V
select a V
experience shows that a 40% decrease can be seen on
auxiliary windings from nominal operation down to standby
mode. Let's select a nominal auxiliary winding of 20 V to
offer sufficient margin regarding 8 V when in standby (R
also drops voltage in standby). Plugging the values in
Equation 10 gives the limits within which R
selected:
that is to say: 1.8 kW < R
the ratio auxiliary/power must be: 12 / 20 = 0.6. The I
current has to not exceed 6.4 mA. This will occur when V
grows-up to: 8.7 V + 1.8 k x (6.4 m + 1.1 m) = 22.2 V for
the first boundary or 8.7 V + 3.6 k x (6.4 m +1.1 m) = 35.7 V
for second boundary. On the power output, it will
respectively give 22.6 x 0.6 = 13.3 V and 35.7 x 0.6 = 21.4 V.
As one can see, tweaking the R
selection of a given overvoltage output level. Theoretically
predicting the auxiliary drop from nominal to standby is an
almost impossible exercise since many parameters are
involved, including the converter time constants. Fine
tuning of R
experiments on a breadboard to check V
also output voltage excursion in fault. Once properly
adjusted, the fail-safe protection will preclude any lethal
voltage runaways in case a problem would occur in the
feedback loop.
trip
nom
stdby
CC(on)
Since R
If we are designing a power supply delivering 12 V, then
is the current corresponding to the nominal operation.
is the auxiliary voltage at nominal load
aux
is the auxiliary voltage when standby is entered
V
is the level above which V
nom
limit
nom
to around 8 V (as selected above), we purposely
* V
I
limit
trip
shall not bother the controller in standby, e.g.
well above this value. As explained before,
20 * 8.7
6.3 m
clamp
thus requires a few iterations and
v R
v R
limit
lim
limit
< 3.6 kW.
v
V
v 12 * 8
limit
stby
aux
1.1 m
value will allow the
ICC1
* V
must be maintained
aux
CC(on)
variations but
limit
shall be
(eq. 10)
(eq. 11)
limit
aux
CC