TB6607FLG Toshiba, TB6607FLG Datasheet
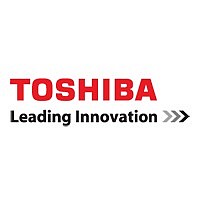
TB6607FLG
Specifications of TB6607FLG
Related parts for TB6607FLG
TB6607FLG Summary of contents
Page 1
... TOSHIBA BiCD Integrated Circuit Silicon Monolithic DC and Stepping Motor Driver IC The TB6607FLG motor driver IC using LDMOS output transistors with low ON-resistance. The TB6607FLG incorporates two PWM-controlled, constant-current H-bridge drivers and three direct-PWM-controlled H-bridge drivers. The TB6607FLG is best suited to control various lens actuators in digital still cameras. ...
Page 2
... REF OSC 24 OSC PWME PWMD PWMC PWMB B.G V ref (0.3 V) 6-bit DAC1 6-bit DAC2 2 TB6607FLG PWMA NCNC H-bridge Pre- driver PGND1 33 Pre- H-bridge driver VM2 28 Pre- H-bridge driver PGND2 TSD ...
Page 3
... PWM signal input (Channel-B) 28 CO1 O Channel-C output 1 ⎯ 29 PGND2 Motor ground pin 2 30 CO2 O Channel-C output 2 ⎯ No-connect 32 BO2 O Channel-B output 2 33 BO1 O Channel-B output 1 ⎯ 34 PGND1 Motor ground pin 1 35 AO2 O Channel-A output 2 ⎯ No-connect Function 3 TB6607FLG 2008-01-15 ...
Page 4
... Min Typ. Max V 2 2.5 5 5.5 M ⎯ ⎯ 600 I OUT ⎯ ⎯ 350 ⎯ ⎯ f 500 pwm ⎯ ⎯ osc 4 TB6607FLG Remarks Control input pins IC only (Note) Unit 5 2.2 V ≤ V ≤ kHz MHz 2008-01-15 ...
Page 5
... Cr ⎯ ⎯ DCH ⎯ CHD ⎯ t 200 ns CHL ⎯ t 200 ns LDC ⎯ t 100 ns LDC2 ⎯ μ LDH ⎯ MHz CLK t CKH CKL CHD t t CHL LDH t DCH 5 TB6607FLG t LDC2 2008-01-15 ...
Page 6
... PWM is turned on and off.) OUT1 M OUT2 <PWM: ON> t1 OUT1 <PWM: OFF → ON> Output voltage waveform (OUT1) OUT1 M OUT2 GND <PWM: ON → OFF> OUT2 OUT1 GND TB6607FLG OUT1 M OUT2 GND <PWM: OFF> OUT2 GND <PWM: ON> GND 2008-01-15 GND ...
Page 7
... OSC = 1 t2, then the V OSC as follows: OSC ⋅ C OSC OSC × × C 6.957 10 C OSC OSC = 270 pF OSC = 560 pF OSC OSC ) experimentally. 7 TB6607FLG V Waveform OSC slope (Δ OSC OSC OSC can be calculated as: may slightly differ from the theoretical 2008-01-15 slope, ...
Page 8
... When high-side output transistors are turned off, the TB6607FLG, by default, counts five rising edges of the internal CK signal as turn-off period. (The counter resets at the sixth rising edge of CK.) Based on this turn-off period, the TB6607FLG generates a PWM signal that turns on and off the output transistors. ...
Page 9
... TB6607FLG Last Data Address ⎯ ⎯ p1b 0 ⎯ ⎯ pm1 1 ⎯ ⎯ p3b 2 p4b off5 off4 3 ⎯ ⎯ pm4 ...
Page 10
... IC Pins pxb PWMx OutxA OutxB TB6607FLG Mode Stop Short brake Reverse Short brake Forward Short brake Mode Stop Reverse Short brake Forward Short brake Short brake Mode Stop Forward Reverse Short brake 2008-01-15 ...
Page 11
... L ( ( (Design target only (L) V ref LB Channels D and E DLB = 270 osc OSC T SD (Design target only.) Δ TB6607FLG = 3 Min. Typ. Max. Unit ⎯ ⎯ 0.1 10 μA ⎯ ⎯ −0.8 +0 ...
Page 12
... AO1 1 Step H-bridge AO2 motor PGND1 34 BO1 33 H-bridge BO2 B 32 VM2 25 CO1 28 DC H-bridge CO2 motor C 30 PGND2 29 TSD VM3 14 DO1 15 DC H-bridge DO2 motor 0.5 Ω RFD 17 EO1 10 Shutter H-bridge EO2 coil 0.5 Ω RFE 11 TB6607FLG V M 2.2 to 5.5 V 2008-01-15 ...
Page 13
... When using the TB6607FLG, it should be ensured that the thermal pad and solder plated pads (shaded areas in the top and bottom views) are electrically insulated (Note). Note: Care should be taken in the board design to prevent solder for through-hole joints from flowing to the solder plated pads on the bottom of the package (shaded areas in the bottom view). • ...
Page 14
... Top View Image CO1 28 PGND2 29 CO2 BO2 32 BO1 33 PGND1 34 AO2 TB6607FLG (top view TB6607FLG 19 18 DO2 17 RFD DO1 VM3 14 13 EO2 RFE EO1 2008-01-15 ...
Page 15
... Package Dimensions Weight: 0.08 g (typ.) 15 TB6607FLG 2008-01-15 ...
Page 16
... Otherwise, the current or power consumption may exceed the absolute maximum rating, and exceeding the rating(s) may cause the device breakdown, damage or deterioration, and may result injury by explosion or combustion. In addition, do not use any device that is applied the current with inserting in the wrong orientation or incorrectly even just one time. 16 TB6607FLG 2008-01-15 ...
Page 17
... If the current sink capability of the power supply is small, the device’s motor power supply and output pins might be exposed to conditions beyond maximum ratings. To avoid this problem, take the effect of back-EMF into consideration in system design. 17 TB6607FLG ) at any time J 2008-01-15 ...
Page 18
... Please use this product in compliance with all applicable laws and regulations that regulate the inclusion or use of controlled substances. Toshiba assumes no liability for damage or losses occurring as a result of noncompliance with applicable laws and regulations. 060819_AF • The products described in this document are subject to foreign exchange and foreign trade control laws. 021023_D 021023_B 060106_Q 18 TB6607FLG 070122EBA_R6 060925_E 2008-01-15 ...