FW250C1 Lineage Power, FW250C1 Datasheet - Page 8
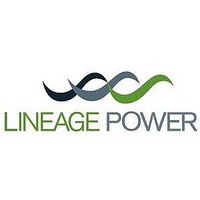
FW250C1
Manufacturer Part Number
FW250C1
Description
Manufacturer
Lineage Power
Datasheet
1.FW250C1.pdf
(20 pages)
dc-dc Converters; 36 to 75 Vdc Input, 15 Vdc Output; 250 W to 300 W
Test Configurations
Note: Measure input reflected-ripple current with a simulated source
Note: Use a 0.1 µF ceramic capacitor and a 10 µF aluminum or
Figure 9. Peak-to-Peak Output Noise
Note: All measurements are taken at the module terminals. When
Figure 10. Output Voltage and Efficiency
8 8
BATTERY
V
Figure 8. Input Reflected-Ripple Test Setup
V
inductance (L
tery impedance. Measure current as shown above.
tantalum capacitor. Scope measurement should be made
using a BNC socket. Position the load between 50 mm and
76 mm (2 in. and 3 in.) from the module.
socketing, place Kelvin connections at module terminals to
avoid measurement errors due to socket contact resistance.
η
O
SUPPLY
O
RESISTANCE
(+)
(+)
=
CONTACT
⎛
⎝
TO OSCILLOSCOPE
[
------------------------------------------------- -
Measurement Test Setup
Measurement Test Setup
V
[
V
O
I
I
I
+ ( ) – V
+ ( ) – V
TEST
COPPERSTRIP
1.0μF
) of 12 µH. Capacitor C
Cs 220 μF
ESR < 0.1 Ω
@ 20 °C, 100 kHz
V
V
I
I
(+)
(–)
O
LTEST
I
SENSE(+)
SENSE(–)
12 μH
– ( )
– ( )
V
10.0μF
V
]I
]I
O
O
(+)
(–)
I
O
ESR < 0.3 Ω
⎞ x 100
⎠
@ 100 kHz
100 μF
SCOPE
DISTRIBUTION LOSSES
I
O
CONTACT AND
S
offsets possible bat-
%
RESISTIVE
LOAD
LOAD
V
V
8-513 (F).m
8-203 (F).o
8-683 (F).f
I
I
(+)
(–)
Design Considerations
Input Source Impedance
The power module should be connected to a low
ac-impedance input source. Highly inductive source
impedances can affect the stability of the power mod-
ule. For the test configuration in Figure 8, a 100 µF
electrolytic capacitor (ESR < 0.3 ¾ at 100 kHz)
mounted close to the power module helps ensure sta-
bility of the unit. For other highly inductive source
impedances, consult the factory for further application
guidelines.
Safety Considerations
For safety-agency approval of the system in which the
power module is used, the power module must be
installed in compliance with the spacing and separation
requirements of the end-use safety agency standard,
i.e., UL1950, CSA C22.2 No. 950-95, and VDE 0805
(EN60950, IEC950).
If the input source is non-SELV (ELV or a hazardous
voltage greater than 60 Vdc and less than or equal to
75 Vdc), for the module’s output to be considered
meeting the requirements of safety extra-low voltage
(SELV), all of the following must be true:
n
n
n
n
Note: Do not ground either of the input pins of the
The power module has extra-low voltage (ELV) outputs
when all inputs are ELV.
The input to these units is to be provided with a maxi-
mum 20 A normal-blow fuse in the ungrounded lead.
The input source is to be provided with reinforced
insulation from any hazardous voltages, including the
ac mains.
One V
both the input and output pins are to be kept floating.
The input pins of the module are not operator acces-
sible.
Another SELV reliability test is conducted on the
whole system, as required by the safety agencies, on
the combination of supply source and the subject
module to verify that under a single fault, hazardous
voltages do not appear at the module’s output.
module without grounding one of the output pins.
This may allow a non-SELV voltage to appear
between the output pin and ground.
I
pin and one V
O
pin are to be grounded, or
Lineage Power
April 2008