AD9101AR Analog Devices Inc, AD9101AR Datasheet - Page 6
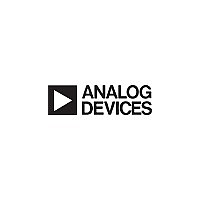
AD9101AR
Manufacturer Part Number
AD9101AR
Description
Sample and Hold 1-CH 0.016us 20-Pin SOIC W
Manufacturer
Analog Devices Inc
Datasheet
1.AD9101AR.pdf
(12 pages)
Specifications of AD9101AR
Package
20SOIC W
Acquisition Time
0.016 us
Number Of S/h
1
Operating Supply Voltage
-5.2/5 V
Available stocks
Company
Part Number
Manufacturer
Quantity
Price
Company:
Part Number:
AD9101AR
Manufacturer:
AD
Quantity:
5 510
Company:
Part Number:
AD9101AR
Manufacturer:
PHILIPS
Quantity:
5 510
Part Number:
AD9101AR
Manufacturer:
ADI/亚德诺
Quantity:
20 000
Company:
Part Number:
AD9101ARZ
Manufacturer:
IXYS
Quantity:
101
Part Number:
AD9101ARZ
Manufacturer:
ADI/亚德诺
Quantity:
20 000
AD9101
The architecture of the AD9101 minimizes hold mode distor-
tion over its specified frequency range. As an example, in track
mode the worst harmonic generated for a 20 MHz input tone is
typically –65 dBFS. In hold mode, under the same conditions
and sampling at 50 MSPS, the worst harmonic generated is
–75 dBFS. The reason is the output amplifier in hold mode has
only a dc distortion relevancy. With its inherent linearity (7 ns
settling to 0.01%), the output amplifier has essentially settled to
its dc distortion level even for track plus hold times as short as
20 ns. For a traditional open-loop output buffer, the ac (track
mode) and dc (hold mode) distortion levels are often the same.
Droop Rate
Droop rate does not necessarily affect a track-and-hold’s distor-
tion characteristics. If the droop rate is constant versus the input
voltage for a given hold time, it manifests itself as a dc offset
to the encoder. For the AD9101, the droop rate is typically
3 mV/ s. If a signal is held for 1 s, a subsequent encoder will
see a 3 mV offset voltage. If there is no droop sensitivity to the
held voltage value, the offset would be constant and “ride” on
the input signal and introduce no hold-mode nonlinearities.
When droop rate varies proportionately to the level of the held
voltage signal level, only a gain error is introduced to the A/D
encoder. The AD9101 has a droop sensitivity to the input level
of 20 mV/V s. For a 2 V p-p output signal, this translates to a
1%/ s gain error and does not cause additional distortion errors.
However, hold times longer than about 500 ns can cause distor-
tion due to the R
addition, hold mode noise will increase linearly vs. hold time
and thus degrade SNR performance.
Layout Considerations
For best performance results, good high speed design tech-
niques must be applied. The component (top) side ground
plane should be as large as possible; two-ounce copper cladding
is preferable. All runs should be as short as possible, and de-
coupling capacitors must be used.
The schematic of a recommended AD9101 evaluation board is
shown. (Contact factory concerning availability of assembled
boards.) All 0.01 F decoupling capacitors should be low induc-
tance surface mount devices (P/N 05085C103MT050 from
AVX) and connected with short lead lengths to minimize stray
inductance.
The 10 F, low frequency tantalum power supply decoupling
capacitors should be located within 1.5 inches of the AD9101.
The common 0.01 F supply capacitors can be wired together.
The common power supply bus (connected to the 10 F capaci-
tor and power supply source) can be routed to the underside of
the board to the daisy chain wired 0.01 F supply capacitors.
For remote input and/or output drive applications, controlled
impedances are required to minimize line reflections which will
reduce signal fidelity. When capacitive and/or high impedance
levels are present, the load and/or source should be physically
located within approximately one inch of the AD9101. Note
that a series resistance, R
6 pF. (The Recommended R
formance Section” shows values of R
loads which result in no more than a 20% increase in settling
time for loads up to 80 pF.) For best results when driving
heavily capacitive or low resistance loads, the AD9630 buffer is
strongly suggested. As much of the ground plane as possible
HC time constant at the hold capacitor. In
S
, is required if the load is greater than
S
vs. C
L
S
chart in the “Typical Per-
for various capacitive
–6–
should be removed from around the V
mize coupling onto the analog signal path.
While a single ground plane is recommended, the analog signal
and differential ECL clock ground currents follow a narrow path
directly under their common voltage signal line. To reduce re-
flections, especially when terminations are used for transmission
line efficiency, the clock, V
ground paths should not cross each other; if they do, unwanted
coupling can result. Analog terminations should be kept as far as
possible from the power supply decoupling capacitors to mini-
mize supply current spike feedthrough.
Driving the Encode Clock
The AD9101 requires a differential ECL clock command. Due
to the high gain bandwidth of the AD9101 internal switch, the
input clock should have a slew rate of at least 400 V/ s.
To obtain maximum signal to noise performance, especially at
high analog input frequencies, a low jitter clock source is re-
quired. The AD9101 clock can be driven by an AD96685, an
ultrahigh speed ECL comparator with very low jitter.
Figure 2 illustrates a recommended termination for the differen-
tial encode clock inputs of the AD9101. The 40
quired to level shift the ECL voltages more negative. This
increases the linear signal range of the sampler. When the input
is less than 600 mV (2.4 V p-p output), these level shift resistors
are not required.
When driving the encode clock from a remote circuit via
transmission lines, or where stray capacitance exceeds 2 pF,
Thevenin equivalent terminations should be used (270
–5.2 V and 160
nation, R
Driving the Analog Input
Special care must be taken to ensure that the analog input signal
is not compromised before it reaches the AD9101. To obtain
maximum signal to noise performance, a very low phase noise
analog source is required. In addition, input filtering and/or a
low harmonic signal source is necessary to maximize the spuri-
ous free dynamic range. Any required filtering should be located
close to the AD9101 and away from digital lines.
Matching the AD9101 to A/D Encoders
The AD9101’s analog output level may have to be offset or am-
plified to match the full-scale range of a given A/D converter.
This can generally be accomplished by inserting an amplifier af-
ter the AD9101. For example, the AD671 is a 12-bit 500 ns
monolithic ADC encoder that requires a 0 V to +5 V full-scale
analog input. An AD84X series amplifier could be used to con-
dition the AD9101 output to match the full-scale range of the
AD671.
The AD9101 can perform a dc level shift function when its input
is bipolar and the ADC requires a unipolar signal. The AD9002
Figure 2. Recommended Encode Clock Termination
LS
R
40
LS
should be 20 .
510
–5.2 V
to ground). For this 100
CLK
10
IN
, and V
OUT
IN
signals and respective
and V
CLK
11
equivalent termi-
–5.2 V
OUT
510
R
pins to mini-
R
40
LS
LS
is re-
REV. 0
to