AD7874AR-REEL Analog Devices Inc, AD7874AR-REEL Datasheet - Page 12
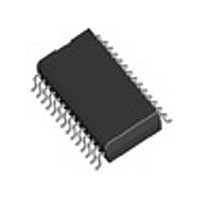
AD7874AR-REEL
Manufacturer Part Number
AD7874AR-REEL
Description
Manufacturer
Analog Devices Inc
Datasheet
1.AD7874AR-REEL.pdf
(16 pages)
Specifications of AD7874AR-REEL
Number Of Elements
1
Resolution
12Bit
Architecture
SAR
Sample Rate
116KSPS
Input Polarity
Bipolar
Input Type
Voltage
Rated Input Volt
±10V
Differential Input
No
Power Supply Requirement
Dual
Single Supply Voltage (typ)
Not RequiredV
Single Supply Voltage (min)
Not RequiredV
Single Supply Voltage (max)
Not RequiredV
Dual Supply Voltage (typ)
±5V
Dual Supply Voltage (min)
±4.75V
Dual Supply Voltage (max)
±5.25V
Power Dissipation
150mW
Differential Linearity Error
±1LSB
Integral Nonlinearity Error
±1LSB
Operating Temp Range
-40C to 85C
Operating Temperature Classification
Industrial
Mounting
Surface Mount
Pin Count
28
Package Type
SOIC W
Input Signal Type
Single-Ended
Lead Free Status / Rohs Status
Not Compliant
AD7874
APPLICATIONS
Vector Motor Control
The current drawn by a motor can be split into two compo-
nents: one produces torque and the other produces magnetic
flux. For optimal performance of the motor, these two compo-
nents should be controlled independently. In conventional
methods of controlling a three-phase motor, the current (or
voltage) supplied to the motor and the frequency of the drive are
the basic control variables. However, both the torque and flux
are functions of current (or voltage) and frequency. This cou-
pling effect can reduce the performance of the motor because,
for example, if the torque is increased by increasing the fre-
quency, the flux tends to decrease.
Vector control of an ac motor involves controlling phase in addi-
tion to drive and current frequency. Controlling the phase of the
motor requires feedback information on the position of the rotor
relative to the rotating magnetic field in the motor. Using this
information, a vector controller mathematically transforms the
three phase drive currents into separate torque and flux compo-
nents. The AD7874, with its four-channel simultaneous sam-
pling capability, is ideally suited for use in vector motor control
applications.
SETPOINT
SETPOINT
TORQUE
FLUX
Figure 17. Vector Motor Control Using the AD7874
MICROPROCESSOR
TRANSFORMATION
CALCULATIONS &
*ADDITIONAL PINS OMITTED FOR CLARITY
TORQUE & FLUX
CONTROL LOOP
FLUX CURRENT
TWO TO THREE
COMPONENTS
INFORMATION
TO TORQUE &
PHASE
DSP
–12–
DAC
DAC
DAC
AD7874*
A block diagram of a vector motor control application using the
AD7874 is shown in Figure 17. The position of the field is de-
rived by determining the current in each phase of the motor.
Only two phase currents need to be measured because the third
can be calculated if two phases are known. Channel 1 and
Channel 2 of the AD7874 are used to digitize this information.
Simultaneous sampling is critical to maintain the relative phase
information between the two channels. A current sensing isola-
tion amplifier, transformer or Hall effect sensor is used between
the motor and the AD7874. Rotor information is obtained by
measuring the voltage from two of the inputs to the motor.
Channel 3 and Channel 4 of the AD7874 are used to obtain this
information. Once again the relative phase of the two channels
is important. A DSP microprocessor is used to perform the
mathematical transformations and control loop calculations on
the information fed back by the AD7874.
V
V
V
V
IN2
IN3
IN4
IN1
CIRCUITRY
DRIVE
AMPLIFIERS
ISOLATION
ATTENUATORS
VOLTAGE
I
I
I
C
B
A
V
V
B
A
MOTOR
PHASE
3
REV. C