FNY-NS115 Omron, FNY-NS115 Datasheet
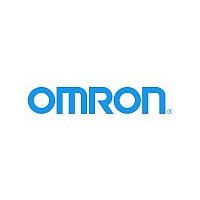
FNY-NS115
Specifications of FNY-NS115
FNY-NS115 Summary of contents
Page 1
Cat. No. W453-E1-08 SYSMAC CXONE-AL@@C-V@/ CXONE-AL@@D-V@ CX-Drive OPERATION MANUAL ...
Page 2
...
Page 3
CXONE-AL@@C-V@/ CXONE-AL@@D-V@ CX-Drive Operation Manual Revised October 2008 ...
Page 4
iv ...
Page 5
... OMRON. No patent liability is assumed with respect to the use of the information contained herein. Moreover, because OMRON is con- stantly striving to improve its high-quality products, the information contained in this manual is subject to change without notice ...
Page 6
vi ...
Page 7
TABLE OF CONTENTS PRECAUTIONS . . . . . . . . . . . . . . . . . . . . . . . . . . . . . . . . . . . 1 ...
Page 8
TABLE OF CONTENTS ...
Page 9
... The CX-Drive runs on Windows 98, 2000, XP, or Vista and is used to set, transfer, and compare parameters; perform test runs and adjustment; and perform- ing monitoring and data tracing for OMRON Inverters and Servos. Please read this manual carefully and be sure you understand the information provided before attempting to use the CX-Drive ...
Page 10
For details on procedures for installing the CX-Drive from the CX-One FA Integrated Tool Package, refer to the CX-One Setup Manual (W463) provided with CX-One. Cat. No. W463 CXONE-AL@@C-V3/ AL@@D-V3 Precautions provides general precautions for using the CX-Drive, Programmable Controller, ...
Page 11
Version Improvements Addition of Supported Inverters Support for the following Inverters has been added for version 1.12 of the CX-Drive: 3G3RV Inverters, Version 1 (-V1) To specify the 3G3RV-V1 offline with CX-Drive version 1.3, select "3G3RV" in the Drive Type ...
Page 12
xii ...
Page 13
... OMRON within the above warranty period, OMRON will replace the Software without charge by offering media or downloading services from the Internet. And if the User discovers a defect in the media which is attributable to OMRON and returns the Software to OMRON within the above warranty period, OMRON will replace the defective media without charge. If OMRON is unable to replace the defective media or correct the Software, the liability of OMRON and the User's remedy shall be limited to a refund of the license fee paid to OMRON for the Software ...
Page 14
xiv ...
Page 15
This section provides general precautions for using the CX-Drive. The information contained in this section is important for the safe and reliable application of the CX-Drive. You must read this section and understand the information contained before attempting to install ...
Page 16
... It is extremely important that the CX-Drive and related devices be used for WARNING the specified purpose and under the specified conditions, especially in appli- cations that can directly or indirectly affect human life. You must consult with your OMRON representative before applying CX-Drive and related devices to the above-mentioned applications. 3 Safety Precautions ...
Page 17
... BHS-US01/GP manufactured by Buffalo USB-CVRS9 manufactured by Sanwa The commercially available USB-serial converters have been successfully tested for OMRON Inverters but operation may be unstable in some operating environments (mainly depending on the ambient temperature, humidity, and noise). The functions, performance, and reliability of these converters may not be as specified under all possible conditions ...
Page 18
Application Precautions xviii 4 ...
Page 19
This section provides an overview of the CX-Drive, and describes the functions and system requirements required to operate the CX-Drive. It also provided installation methods and the overall procedure for using the CX-Drive. 1-1 Introduction . . . . . ...
Page 20
... CN3 CN1 CN2 CNB CNA The CX-Drive can be used with OMRON's 3G3JX, 3G3MX, and 3G3RX, 3G3JV, 3G3MV, and 3G3RV Inverters, as well as OMRON's SMARTSTEP2, SMARTSTEP, OMNUC G-series, and MECHATROLINK-II compliant (see note) G-series, OMNUC W-series, and MECHATROLINK-II compliant W- series Servo Drives. Inverter and Servo parameters can be edited using parameter numbers or by category ...
Page 21
Introduction Inverter Tuning and Test Runs Auto-tuning for the 3G3RV Just enter the specified motor parameters and let the Servo automatically tune itself to match the characteristics of the motor. Inverter Test Runs The test run options enable the acceleration, ...
Page 22
... Communications Unit (3G3JV-PSI232JC) or RS-422/485 Communications Unit (3G3JV-PSI485J) re- quired. Uses Modbus-RTU protocol. *2.RS-422A/485: Modbus-RTU protocol. *3.DeviceNet Communications Unit (3G3MV-PDRT2) required. *4.DeviceNet Communications Unit (3G3RV-PDRT2) required. *5.RS-232C: Special protocol. *6.MECHATROLINK-II Interface Unit (JUSP-NS115/FNY-NS115) required. 4 The CX-Drive supports the following drives and communications. Communications Serial communications Supported ...
Page 23
Introduction 1-1-4 Files Created by CX-Drive The CX-Drive creates the following files. Note Consecutive parameters can be exported to Microsoft Excel via the clipboard by selecting the required parameters with the mouse or from the keyboard (Shift + Cursor Keys) ...
Page 24
Installation 1-2 Installation 1-2-1 Required Software To use the CX-Drive, the software applications listed below must be installed on the same computer. CX-Drive Availability The CX-Drive Ver.1.6 must be installed from the CX-One Package. CX-Drive Ver.1.7 will be available either ...
Page 25
System Configuration 1-3 System Configuration 1-3-1 Inverter Connection Direct serial connection Configuration for 3G3JX/MX/RX Note USB Genral purpose USB-RS422 convert cable CX-Drive Detach Digital USB Operator. USB-RS422 Convert Cable SYSDRIVE 3G3JX/MX/RX 3G3JX : Set parameter C070=02(OPE). 3G3MX/RX : Remove front ...
Page 26
System Configuration Configuration for 3G3JV/MV/RV Computer-Inverter Connecting Cable Required devices The CS1W-CIF31 Serial Conversion Cable cannot be used to connect a computer running the CX- Caution Drive to the 3G3MV. (See the following note.). 8 CX-Drive RS-232C Detach Digital Operator. ...
Page 27
... BHS-US01/GP manufactured by Buffalo USB-CVRS9 manufactured by Sanwa The commercially available USB-serial converters have been successfully tested for OMRON Inverters but operation may be unstable in some operating environments (mainly depending on the ambient temperature, humidity, and noise). The functions, performance, and reliability of these converters may not be as specified under all possible conditions ...
Page 28
System Configuration PLC Serial Communications Unit / Board connection Configuration For Peripheral Port : CS1W-CN226 or CS1W-CN626 For RS-232C Port: XW2Z-200S-CV or XW2Z-500S-CV Or via network *1. Required devices Note The Serial Gateway Mode is used as the serial communications ...
Page 29
System Configuration PLC DeviceNet connection Configuration For Peripheral Port : CS1W-CN226 or CS1W-CN626 For RS-232C Port : XW2Z-200S-CV or XW2Z-500S-CV Or via network Required devices CX-Drive Peripheral port Or RS-232C port RS-232C PA205R SYSMAC POWER CJ1G-CPU44 PROGRAMMABLE CONTROLLER L1 AC100-240V ...
Page 30
System Configuration 1-3-2 Servo Connection Direct serial connection Configuration Required devices 12 CX-Drive RS-232C POWER ALM Computer Monitor Cable Model SMARTSTEP2 R88A-CCG002P2 Computer Monitor Cable Series (R7D-BP) OMNUC G Series *1 (R88D-GT) OMNUC G Series (R88D-GN) SMARTSTEP A R7A-CCA002P2 Computer ...
Page 31
System Configuration PLC Serial Communications Unit / Board connection With Servo Relay Unit to Control Servo • Configuration For Peripheral Port : CS1W-CN226 CS1W-CN626 For RS-232C Port : XW2Z-200S-CV XW2Z-500S-CV *1. CS/CJ-series Serial Communications Unit / Board Ver. 1.2 or ...
Page 32
System Configuration • Required devices Note 14 Model SMARTSTEP2 *1 --- Series (R7D-BP) OMNUC G Series *1 --- (R88D-GT) OMNUC G Series *2 --- (R88D-GN) SMARTSTEP A XW2Z-@@@J-CJ Serial Communications Unit / Board Connect- Series ing Cable + XW2B-40J6-4A Servo ...
Page 33
System Configuration Without Servo Relay Unit • Configuration RS-232C For Peripheral Port : CS1W-CN226 CS1W-CN626 For RS-232C Port : XW2Z-200S-CV XW2Z-500S-CV *1. CS/CJ-series Serial Communications Unit / Board Ver. 1.2 or later • Required devices Note The Serial Gateway Mode ...
Page 34
... SMARTSTEP A *1 --- Series (R7D-AP) OMNUC W Series MECHATROLINK-II Cable MECHATROLINK-II Interface Unit (FNY-NS115) (R88D-WT) OMNUC W Series MECHATROLINK-II Cable (R88D-WN) *1.MECHATROLINK-II communication via PLC is not available. *2.CX-Drive does not support R88D-GN MECHATROLINK-II connection. Controller support tool (CX-Motion-NCF) can be used. Section 1-3 ...
Page 35
This section provides basic operating procedures for using the CX-Drive, including descriptions of CX-Drive windows and parameter setting procedures. 2-1 Overall Operating Procedure ...
Page 36
... Connect the CX-Drive (computer) to the drive (Inverter or Servo) using one of the system configurations. • Refer to 1-3 System Configuration • Select Program - OMRON - CX-One - CX-Drive - CX-Drive from the Windows Start Menu. • Detect the drives connected online automatically and create drive file for the desired drive ...
Page 37
Overall Operating Procedure 6. Connect online to the drive. 7. Transfer and verify the parameters. 8. Tune and test operation. 9. Monitor operation. 10. Save the data. • Select Drive - Work Online from the menu bar. • Select Drive ...
Page 38
... Connect the CX-Drive (computer) to the drive (Inverter or Servo) using one of the system configurations. • Refer to 1-3 System Configuration • Select Program - OMRON - CX-One - CX-Drive - CX-Drive from the Windows Start Menu. • Detect the drives connected online automatically and create drive file for the desired drive ...
Page 39
Overall Operating Procedure 5. Edit the parameters. 6. Connect online to the drive. 7. Transfer and verify the parameters. 8. Tune and test operation. 9. Monitor operation. 10. Save the data. • Edit the parameters for the Servo. • In ...
Page 40
... Starting the CX-Drive Note 22 Select Program - OMRON - CX-One - CX-Drive - CX-Drive from the Win- dows Start Menu to start the CX-Drive. (The path depends on where the CX- Drive was installed.) When using the 3G3MV or 3G3RV as a DeviceNet slave, right-click the Inverter on the CX-Integrator network configuration, and select Start special application - Start with Settings Inherited from the pop-up menu ...
Page 41
Creating New Drive Files 2-3 Creating New Drive Files There are two methods to create a new drive file in the Workspace. Method 1: Go online and automatically detect the connected drives to create the drive file. Method 2: Create ...
Page 42
Creating New Drive Files 24 3. Push Advanced Options button, and select further settings. 4. Select Drive-Autodetect menu. CX-Drive searches selected targets in option settings, and creates the drive data for detected target. Section 2-3 ...
Page 43
Creating New Drive Files Other Connections 1. Select Drive- Autodetect Option. 1,2,3... 2. Push Advanced Options and select settings. 3. Select Drive - Autodetect. 4. The rest of the procedure is the same as Serial Direct Connention. “via PLC” can ...
Page 44
Creating New Drive Files 2-3-2 Method 2: Creating a New Data File without a Connected Drive Select File - New. The following New Drive Dialog Box will be displayed. Drive Name Any name may be input for the drive name. ...
Page 45
Creating New Drive Files Detailed Drive Settings Click the Settings… Button to open the Detail Setting Dialog Box. Inverters Inverter Series Dialog box Drive Type Installation A Type/Option Voltage 2/E Class Maximum 002, 004, 007, 015, 022, 037 Motor Capacity ...
Page 46
Creating New Drive Files Servos Servo Series Dialog box Drive Type Maximum A5 ( (400 W) Motor Capacity Voltage H (200 V), HH(200V), Class L (100 V) Specifica- --- tions Servo Series Dialog box Drive Type Maximum ...
Page 47
... Not supported. supported. supported. Section 2-3 3G3JV 3G3MV 3G3RV Suported. Suported. Suported. Suported. Suported. Suported. Not Suported. Suported. supported. R7D-AP R88D-WT R88D-WN supported. Supported. Supported. Not supported. Not Supported Supported. supported. with FNY- NS115. Not Supported Supported. supported. with FNY- NS115. 29 ...
Page 48
Creating New Drive Files Network Settings Click the Settings... Button to the right of the Connection Type Field. The following dialog box will be displayed. Detailed Settings for Direct Connections Item Network Tab Page Dialog box Inverter • Slave Unit ...
Page 49
Creating New Drive Files Via PLC (SCU/SCB) Connections (Except R88D-WN) Item Network Tab Page Dialog box Inverter • Slave Unit Address (Modbus-RTU slave address) (See note 1.) • Master Unit Address (Unit address for ...
Page 50
Creating New Drive Files Via PLC (DeviceNet) Connections (3G3MV, 3G3RV) Via PLC (MCH/MECHATROLINK-II) or Via PLC (NCF/MECHATROLINK-II) (R88D-WN) 32 Network Tab Page • Slave Unit Address (DeviceNet slave address) • Master Unit Address (DeviceNet ...
Page 51
User Interface 2-4 User Interface 2-4-1 Window Structure Workspace Output Window Status bar 2-4-2 Functions Functions Table Windows Folder Parameter Editor Edits the parameters of Inverters or Servos. Graphs Displays parameters graphically. Diagrams Displays parameters in block diagrams. Status Displays ...
Page 52
User Interface Functions Folder Parameter Editor Graphs Diagrams Status Monitor Tuning Settings Folder Parameter Editor Graphs Diagrams Status Monitor Tuning Settings Note These functions are not supported when communicating via MECHA- TROLINK II. 34 Inverters 3G3JX 3G3MX 3G3RX OK OK ...
Page 53
User Interface Inverters Folder 3G3JX Parameter • Basic Settings Editor • Analog Input • Multi-Step Speed, Jogging • Charasteristics, Torque Boost • DC Injection Braking • Upper/Lower Limit, Jump • PID Control • AVR • RUN Mode, Accel/Decel Func- tions ...
Page 54
User Interface Folder 3G3JV Parameter • Initialize Editor • Application • Tuning • Reference • Motor • Terminal • Protection • Operator • Monitor Constants Graphs • Analogue Input 1 • Analogue Output 1 • Jump Frequencies • V/F Profile ...
Page 55
User Interface Servos Folder R7D-BP Parameter • Function Selection Parameters Editor • Gain Related Parameters • Position Control Related Parameters • Internal Speed Control Related Parameters • Sequence Related Parameters Diagrams • Internal Speed Control Mode • Position Control Mode ...
Page 56
User Interface 2-4-3 Menu Commands Menu Submenu/Command File New Autodetect Open Close Open Workspace Close Workspace Save Workspace Save as Workspace Save Save As Save All Print Print Preview Page Setup Import Export Recent file Recent Workspace Exit Edit Undo ...
Page 57
User Interface Menu Submenu/Command View Motor Manegement Zoom Pan Mode Cursor Mode Show Parameter Labels Show Parameter Value Show Changes Only Show Differences Only Show Invalids Only Display Format Drive Change Work Online Initialize Password Protection Parameter Editor Select Parameter ...
Page 58
... Arranges the icons at the bottom of the window. Displays an index to topics on which help is available. Provides contextual help to provide help relating to the active window. Registers your application on the OMRON website. Opens the OMRON Corporate website. Displays the version number of the appli- cation. Section 2-4 Inverter Servo Icon OK ...
Page 59
Editing Drive Files 2-5 Editing Drive Files 1. Use the New Drive Dialog Box to set the drive name, drive type, connection type, and other information Use Autodetect to select the target drive. The following window will be ...
Page 60
Editing Drive Files 2-5-1 Editing Parameters Parameter Editor: Numeric Order Parameter Editor in Functional Categories Comparing Drive and Parameter Data 42 The parameters for each drive (an Inverter or Servo) can be edited under the parameter numbers. Double-click Parameter Editor ...
Page 61
Editing Drive Files 2-5-2 Graphs Parameters can be displayed in graphic form for review (for Inverters only). 2-5-3 Diagrams Parameters can be displayed in block diagrams for relevant parameters. Inverters support PID block diagrams, and Servos support position, speed and ...
Page 62
Editing Drive Files 2-5-4 Status Displays 2-5-5 Monitoring 44 The status of the online drive can be displayed. Double-click. Performs status monitor for the connected drive. Realtime traces can be displayed for the selected parameters of the online drive. Data ...
Page 63
Editing Drive Files 2-5-6 Data Trace There is the Data Trace function for Servo drive serial direct connection com- munication to get Servo Drive Trace data in detail and show it and save it into the file. At the CX-Drive ...
Page 64
Editing Drive Files 2-5-8 Settings The parameters of the online drive can be initialized, and password authoriza- tion can be set for some drive models. 46 The parameters in the online drive can be initialized. Double-click. Also refer to the ...
Page 65
A manual revision code appears as a suffix to the catalog number on the front cover of the manual. The following table outlines the changes made to the manual during each revision. Page numbers refer to the previous version. Revision ...
Page 66
Revision History ...
Page 67
... Cancellation; Etc. Orders are not subject to rescheduling or cancellation unless Buyer indemnifies Omron against all related costs or expenses. 10. Force Majeure. Omron shall not be liable for any delay or failure in delivery resulting from causes beyond its control, including earthquakes, fires, floods, strikes or other labor disputes, shortage of labor or materials, accidents to machinery, acts of sabotage, riots, delay in or lack of transportation or the requirements of any government authority ...
Page 68
... OMRON ELECTRONICS LLC • THE AMERICAS HEADQUARTERS Schaumburg, IL USA • 847.843.7900 • 800.556.6766 • www.omron247.com OMRON CANADA, INC. • HEAD OFFICE Toronto, ON, Canada • 416.286.6465 • 866.986.6766 • www.omron.ca OMRON ELETRÔNICA DO BRASIL LTDA • HEAD OFFICE São Paulo, SP, Brasil • 55.11.2101.6300 • www.omron.com.br OMRON ELECTRONICS MEXICO • ...