XW2Z-200J-B13 Omron, XW2Z-200J-B13 Datasheet - Page 6
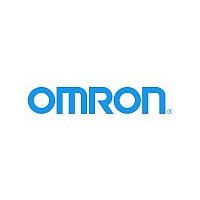
XW2Z-200J-B13
Manufacturer Part Number
XW2Z-200J-B13
Description
SERVO RELAY UNIT CABLES 2M
Manufacturer
Omron
Datasheet
1.XW2Z-200J-B13.pdf
(16 pages)
Specifications of XW2Z-200J-B13
Lead Free Status / Rohs Status
Lead free / RoHS Compliant
Other names
XW2Z200JB13
10
Applications
Pulse Output Control with the FMQ1's High-speed Input Response
Timing Control with the FQM1's Pulse Inputs
Speed
Sensor inputs can be detected with high precision by
using the FQM1's dependable interrupt input
response and the high-speed input latching function
for pulse inputs. This improves precision when
switching or stopping machine operation and
performing processing from sensor inputs.
The pulse input and high-precision output functions
of the FQM1 provide support to perform processing
at a specific distance after detection for when
processing cannot be performed based on time after
an ON/OFF sensor detects an object or when
precision is insufficient.
Cut position detection
Feed cycle
Interrupt
feeding
Cycle time
Mark sensor detection
Servomotor
Cut
Interrupt
feeding
Time
Cutter, nozzle,
camera shutter,
etc.
Sensor
Encoder
Sensor
Cutter
Label feed drive
Servomotor
Pulse output
Servo
driver
Servo driver
Intermittent feeding
Speed pattern
calculation
V
Print feed drive
Pulse
input
Encoder
FQM1
FQM1-MMP22
For example, the stop function can be performed with high-precision
stop positioning at a position a constant distance forward after the
sensor input has entered.
For example, the output can be controlled with high-precision time
control after the target number of pulses has been counted after the
sensor has been input when processing with high-precision is
required at a specified distance advanced (with timing generated
from a number of pulses) after the sensor input has been received.
Application Examples
Functions used: Interrupt input function, pulse latch function
Configuration example: FQM1-CM002 plus FQM1-MMP22 (with pulse I/O)
Application Examples
W
Pulse input
Dancer
roller
Continuous feeding
SPEED command
V
Printer
Servomotor
Pulse output
t
FQM1
FQM1-MMP22
• Cutting printing materials
• Nozzle exposure on items flowing at high-speed
Servo driver
Labeler
Encoder
Note: Also applicable as a 1-µs high-precision timer.
Functions used: Pulse input-target value match
Configuration example: FQM1-CM002 plus
Pulse output
from encoder
Label
Sensor
One-shot output
interrupt function, one-shot
pulse output function (See note.)
Section not to be printed
(distance set from PT)
Cutting position
FQM1-MMP22 (with
pulse I/O)
Fixed pulse
counter
High-precision time
control
t
Target
number of
pulses
Time
Power Supply Module
Note: When using only Motion Control Modules with analog I/O, a maximum of only three Motion Control Modules can be connected.
Note 1: The follow CJ-series Units can be connected as long as the current consumption does not exceed the supply capacity.
Note 2: MECHATROLINK is a registered trademark of Yaskawa Electric Corporation.
The FQM1 consists of a Power Supply Module, a
Coordinator Module, Motion Control Modules, and an End
Module. Motion Control Modules are available with pulse
I/O or analog I/O, and up to four Motion Control Modules of
either type can be connected. (See note.) Each Motion
Control Module controls two axes. Therefore, when four
Some of the PLC SYSMAC CJ-series Units can be used by
mounting an I/O Control Module for the FQM1 to the
FQM1. CJ-series Units can be connected on the right end
Example 1: Expansion with CJ-series Basic I/O Units
Example 3: I/O Expansion and Reduced Wiring with
For the Optimal Control Customers Demand for Their Machines
For the Optimal Control Customers Demand for Their Machines
Flexible
Flexible
Flexible System Configuration Using Modular Configuration
I/O and Other Functions Expandable with CJ-series Units
• CJ-series Basic I/O Units • CompoBus/S Master Units • DeviceNet Units • Position Control Units (NCF Units) with MECHATROLINK-II (See note 2.)
• SYSMAC SPU High-speed Data Collection Unit
CompoBus/S
FQM1-IC101
I/O Control Module
CompoBus/S
Coordinator Module
CJ-series
Basic I/O or other Units
(See note 1.)
FQM1-IC101
I/O Control Module
CJ1W-SRM21
CompoBus/S
Master Unit
Maximum of four Motion Control Modules
Modules are connected, motion control can be performed
for up to eight axes. Also, CJ-series Units can
be mounted if an I/O Control Module is used, enabling a
flexible system configuration to meet the needs of the
application.
of the FQM1 or using the CJ-series I/O Interface Unit with
up to one Expansion Rack.
CJ-series
Expansion Rack
Example 2: Expansion with CJ-series Expansion Rack
Example 4: Expansion with Multi-axis Position Control Units
CJ1W-II101
CJ-series
I/O Interface Unit
Support FQM1 operation
with Position Control Units
for simplified PTP control of
peripheral devices.
Synchronized/High-speed
Response Control
FQM1-IC101
I/O Control Module
FQM1-series
End Module
CJ-series Basic I/O or
other Units (See note 1.)
or
MECHATROLINK-II
FQM1-IC101
I/O Control Module
Multi-axis PTP Control
CJ-series
Unit
CJ1W-NCF71
MECHATROLINK-II
Multi-axis Position
Control Unit
FQM1-IC101
I/O Control
Module
CJ1W-TER01
CJ-series End Cover
Servo
drives
Motors
11