LM4802BLQ National Semiconductor, LM4802BLQ Datasheet - Page 12
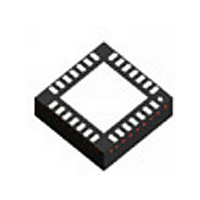
LM4802BLQ
Manufacturer Part Number
LM4802BLQ
Description
Manufacturer
National Semiconductor
Datasheet
1.LM4802BLQ.pdf
(17 pages)
Specifications of LM4802BLQ
Operational Class
Class-AB
Audio Amplifier Output Configuration
1-Channel Mono
Audio Amplifier Function
Speaker
Total Harmonic Distortion
0.05@30Ohm%
Single Supply Voltage (typ)
Not RequiredV
Dual Supply Voltage (typ)
3/5V
Power Supply Requirement
Dual
Rail/rail I/o Type
No
Power Supply Rejection Ratio
66dB
Single Supply Voltage (min)
Not RequiredV
Single Supply Voltage (max)
Not RequiredV
Dual Supply Voltage (min)
2.7V
Dual Supply Voltage (max)
5.5/6.1V
Operating Temp Range
-40C to 85C
Operating Temperature Classification
Industrial
Mounting
Surface Mount
Pin Count
28
Package Type
LLP EP
Lead Free Status / Rohs Status
Not Compliant
Available stocks
Company
Part Number
Manufacturer
Quantity
Price
Company:
Part Number:
LM4802BLQ/NOPB
Manufacturer:
National Semiconductor
Quantity:
1 885
Company:
Part Number:
LM4802BLQX/NOPB
Manufacturer:
NS
Quantity:
171
www.national.com
Application Information
SETTING THE OUTPUT VOLTAGE (V
CONVERTER
The output voltage is set using the external resistors R1 and
R2 (see Figure 1). A value of approximately 13.3kΩ is rec-
ommended for R2 to establish a divider current of approxi-
mately 92µA. R1 is calculated using the formula:
FEED-FORWARD COMPENSATION FOR BOOST
CONVERTER
Although the LM4802B’s internal Boost converter is inter-
nally compensated, the external feed-forward capacitor C
required for stability (see Figure 1). Adding this capacitor
puts a zero in the loop response of the converter. The
recommended frequency for the zero fz should be approxi-
mately 6kHz. C
SELECTING DIODES
The external diode used in Figure 1 should be a Schottky
diode. A 20V diode such as the MBR0520 is recommended.
The MBR05XX series of diodes are designed to handle a
maximum average current of 0.5A. For applications exceed-
ing 0.5A average but less than 1A, a Microsemi UPS5817
can be used.
DUTY CYCLE
The maximum duty cycle of the boost converter determines
the maximum boost ratio of output-to-input voltage that the
converter can attain in continuous mode of operation. The
duty cycle for a given boost application is defined as:
This applies for continuous mode operation.
INDUCTANCE VALUE
The first question we are usually asked is: “How small can I
make the inductor.” (because they are the largest sized
component and usually the most costly). The answer is not
simple and involves trade-offs in performance. Larger induc-
tors mean less inductor ripple current, which typically means
less output voltage ripple (for a given size of output capaci-
tor). Larger inductors also mean more load power can be
delivered because the energy stored during each switching
cycle is:
Where “lp” is the peak inductor current. An important point to
observe is that the LM4802B will limit its switch current
based on peak current. This means that since lp(max) is
fixed, increasing L will increase the maximum amount of
power available to the load. Conversely, using too little in-
ductance may limit the amount of load current which can be
drawn from the output.
Duty Cycle = V
f
1 can be calculated using the formula:
OUT
R1 = R2 X (V
C
f
1 = 1 / (2 X R1 X fz)
+ V
E = L/2 X (lp)2
DIODE
2
- V
/1.23 − 1)
IN
/ V
1
OUT
) OF BOOST
(Continued)
+ V
DIODE
- V
SW
(5)
f
(6)
is
12
Best performance is usually obtained when the converter is
operated in “continuous” mode at the load current range of
interest, typically giving better load regulation and less out-
put ripple. Continuous operation is defined as not allowing
the inductor current to drop to zero during the cycle. It should
be noted that all boost converters shift over to discontinuous
operation as the output load is reduced far enough, but a
larger inductor stays “continuous” over a wider load current
range.
To better understand these trade-offs, a typical application
circuit (5V to 12V boost with a 10µH inductor) will be ana-
lyzed. We will assume:
Since the frequency is 1.6MHz (nominal), the period is ap-
proximately 0.625µs. The duty cycle will be 62.5%, which
means the ON-time of the switch is 0.390µs. It should be
noted that when the switch is ON, the voltage across the
inductor is approximately 4.5V. Using the equation:
We can then calculate the di/dt rate of the inductor which is
found to be 0.45 A/µs during the ON-time. Using these facts,
we can then show what the inductor current will look like
during operation:
During the 0.390µs ON-time, the inductor current ramps up
0.176A and ramps down an equal amount during the OFF-
time. This is defined as the inductor “ripple current”. It can
also be seen that if the load current drops to about 33mA,
the inductor current will begin touching the zero axis which
means it will be in discontinuous mode. A similar analysis
can be performed on any boost converter, to make sure the
ripple current is reasonable and continuous operation will be
maintained at the typical load current values.
MAXIMUM SWITCH CURRENT
The maximum FET switch current available before the cur-
rent limiter cuts in is dependent on duty cycle of the appli-
cation. This is illustrated in a graph in the typical perfor-
mance characterization section which shows typical values
of switch current as a function of effective (actual) duty cycle.
V
IN
= 5V, V
FIGURE 2. 10µH Inductor Current
5V - 12V Boost (LM4802B)
OUT
= 12V, V
V = L (di/dt)
DIODE
= 0.5V, V
SW
= 0.5V
20094198