ADP1111 Panasonic, ADP1111 Datasheet - Page 5
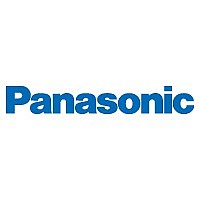
ADP1111
Manufacturer Part Number
ADP1111
Description
Board Mount Pressure Sensors 14.7kPa 0.15kgf/cm Pressure Sensor
Manufacturer
Panasonic
Datasheet
1.ADP1191.pdf
(5 pages)
Specifications of ADP1111
Operating Pressure
0 KPa to 14.7 KPa
Pressure Type
Gauge
Mounting Style
Through Hole
Maximum Operating Temperature
+ 100 C
Minimum Operating Temperature
- 20 C
Package / Case
DIP-6
Lead Free Status / Rohs Status
Lead free / RoHS Compliant
Available stocks
Company
Part Number
Manufacturer
Quantity
Price
Company:
Part Number:
ADP1111A12
Manufacturer:
ADI
Quantity:
8 933
Company:
Part Number:
ADP1111ANZ-3.3
Manufacturer:
AD
Quantity:
2 100
Company:
Part Number:
ADP1111ANZ-5
Manufacturer:
JOHANSON
Quantity:
24 000
Part Number:
ADP1111AR
Manufacturer:
ADI/亚德诺
Quantity:
20 000
Part Number:
ADP1111AR-5
Manufacturer:
ADI/亚德诺
Quantity:
20 000
Company:
Part Number:
ADP1111ARZ
Manufacturer:
AD
Quantity:
1 143
Part Number:
ADP1111ARZ
Manufacturer:
ADI/亚德诺
Quantity:
20 000
Company:
Part Number:
ADP1111ARZ-12
Manufacturer:
ADI
Quantity:
9 343
Part Number:
ADP1111ARZ-12
Manufacturer:
ADI/亚德诺
Quantity:
20 000
Part Number:
ADP1111ARZ-3.3
Manufacturer:
ADI/亚德诺
Quantity:
20 000
NOTES
1. Mounting
Use lands on the printed-circuit boards to
which the sensor can be securely fixed.
2. Soldering
Due to its small size, the thermal capacity
of the pressure sensor DIP type is low.
Therefore, take steps to minimize the ef-
fects of external heat.
Damage and changes to characteristics
may occur due to heat deformation.
Use a non-corrosive resin type of flux.
Since the pressure sensor DIP type is ex-
posed to the atmosphere, do not allow
flux to enter inside.
1) Manual soldering
• Set the soldering tip from 260 to 300°C
500 to 572°F
more than 5 seconds.
• Please note that output may change if
the pressure is applied on the terminals
when the soldering.
• Thoroughly clean the soldering iron.
2) DIP soldering (DIP terminal type)
• Please keep the DIP solder bath temper-
ature no higher than 260°C 500°F. When
soldering, heat should be applied no long-
er than five seconds.
• When mounting onto a PCB of low ther-
mal capacity, please avoid DIP soldering
as this may cause heat deformity.
3) Solder reworking
• Finish reworking in one operation.
• For reworking of the solder bridge, use a
soldering iron with a flat tip. Please do not
add more flux when reworking.
• Please use a soldering iron that is below
the temperature given in the specifications
in order to maintain the correct tempera-
ture at the tip of the soldering iron.
4) Too much force on the terminals will
cause deformation and loss in effective-
ness of the solder. Therefore, please
avoid dropping and careless handling of
the product.
5) Please control warping of the PCB
within 0.05 mm of the sensor width.
6) When cut folding the PCB after mount-
APPLICATION CIRCUIT
DIAGRAM (EXAMPLE)
The pressure sensor is designed to con-
vert a voltage by means of constant cur-
rent drive and then, if necessary, it
amplifies the voltage for use. The circuit
shown below is a typical example of a cir-
cuit in which the pressure sensor is used.
Constant current
circuit unit
(30W), and solder for no
Pressure
sensor
Amplifier circuit unit
OP
AMP
OP
AMP
OP
AMP
All Rights Reserved © COPYRIGHT Panasonic Electric Works Co., Ltd.
ing the sensor, take measures to prevent
stress to the soldered parts.
7) The sensor terminals are designed to
be exposed, so contact of the terminals
with metal shards and the like will cause
output errors. Therefore, please be careful
and prevent things such as metal shards
and hands from contacting the terminals.
8) To prevent degradation of the PCB in-
sulation after soldering, please be careful
not to get chemicals on the sensor when
coating.
9) Please consult us regarding the use of
lead-free solder.
3. Cleaning
1) Since the pressure sensor chip is ex-
posed to the atmosphere, do not allow
cleaning fluid to enter inside.
2) Avoid ultrasonic cleaning since this
may cause breaks or disconnections in
the wiring.
4. Environment
1) Please avoid using or storing the pres-
sure sensor chip in a place exposed to
corrosive gases (such as the gases given
off by organic solvents, sulfurous acid
gas, hydrogen sulfides, etc.) which will ad-
versely affect the performance of the pres-
sure sensor chip.
2) Since this pressure sensor chip does
not have a water-proof construction,
please do not use the sensor in a location
where it may be sprayed with water, etc.
3) Avoid using the pressure sensors chip
in an environment where condensation
may form.
Furthermore, its output may fluctuate if
any moisture adhering to it freezes.
4) The pressure sensor chip is construct-
ed in such a way that its output will fluctu-
ate when it is exposed to light. Especially
when pressure is to be applied by means
of a transparent tube, take steps to pre-
vent the pressure sensor chip from being
exposed to light.
5) Avoid using the pressure sensor chip
where it will be susceptible to ultrasonic or
MOUNTING METHOD
The general method for transmitting air
pressures differs depending on whether
the pressure is low or high.
• Checkpoints for use
<1> Select a pressure inlet pipe which is
sturdy enough to prevent pressure leaks.
<2> Fix the pressure inlet pipe securely
so as to prevent pressure leaks.
<3> Do not block the pressure inlet pipe.
other high-frequency vibration.
5. Quality check under actual loading
conditions
To assure reliability, check the sensor un-
der actual loading conditions. Avoid any
situation that may adversely affect its per-
formance.
6. Other handling precautions
1) That using the wrong pressure range or
mounting method may result in accidents.
2) The only direct pressure medium you
can use is dry air. The use of other media,
in particular, corrosive gases (organic sol-
vent based gases, sulfurous acid based
gases, and hydrogen sulfide based gases,
etc.) and media that contains moisture or
foreign substances will cause malfunction
and damage. Please do not use them.
3) The pressure sensor chip is positioned
inside the pressure inlet. Never poke
wires or other foreign matter through the
pressure inlet since they may damage the
chip or block the inlet. Avoid use when the
atmospheric pressure inlet is blocked.
4) Use an operating pressure which is
within the rated pressure range. Using a
pressure beyond this range may cause
damage.
5) Since static charge can damage the
pressure sensor chip, bear in mind the fol-
lowing handling precautions.
• When storing the pressure sensor chips,
use a conductive material to short the
pins or wrap the entire chip in aluminum
foil. Plastic containers should not be used
to store or transport the chips since they
readily become charged.
• When using the pressure sensor chips,
all the charged articles on the bench sur-
face and the work personnel should be
grounded so that any ambient static will
be safely discharged.
6) Based on the pressure involved, give
due consideration to the securing of the
pressure sensor DIP type and to the se-
curing and selection of the inlet tube. Con-
sult us if you have any queries.
Methods of transmitting air pressures
When the pressure
(4.9 to 98.1 kPa)
is low
Tube
If a tube is used as the pressure inlet pipe,
it may become disengaged. Therefore, use
a sturdy tube and secure it using O-rings.
Printed-
circuit
board
PF (ADP1)
(196.1 to 980.7 kPa)
When the pressure
is high
Printed-
circuit
board
O-ring
Pressure
inlet pipe