RD4247MAG3110 Freescale Semiconductor, RD4247MAG3110 Datasheet - Page 9
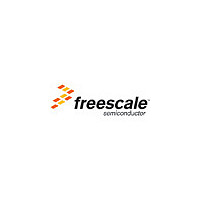
RD4247MAG3110
Manufacturer Part Number
RD4247MAG3110
Description
DEV KIT MAG3110 LFSTBUSB
Manufacturer
Freescale Semiconductor
Series
-r
Specifications of RD4247MAG3110
Sensor Type
Accelerometer, 3 Axis
Sensing Range
±10g
Interface
I²C
Sensitivity
1mg/bit
Voltage - Supply
1.95 V ~ 3.6 V
Embedded
No
Utilized Ic / Part
MAG3110
Features
LFSTBUSB For Communication To PC, MAG3110FC & MMA8451Q For System Calibration
Peak Reflow Compatible (260 C)
Yes
Rohs Compliant
Yes
Application Sub Type
Magnetic Sensor
Lead Free Status / Rohs Status
Lead free / RoHS Compliant
Available stocks
Company
Part Number
Manufacturer
Quantity
Price
Company:
Part Number:
RD4247MAG3110
Manufacturer:
FSL
Quantity:
18
* Data Bytes Outgoing
* Data Bytes Incoming
4.3.2
is set to skip over the LSB data. When FR bit is cleared, the complete 16-bit data is read accessing all 6 bytes sequentially
(OUT_X_MSB, OUT_X_LSB, OUT_Y_MSB, OUT_Y_LSB, OUT_Z_MSB, OUT_Z_LSB).
4.3.3
device board mount. These values may be used to compensate for hard iron interference.
offset values (RAW = 0), or can be read out uncorrected for user offset values (RAW = 1). The factory calibration correction is
always applied irrespective of the setting of the RAW bit. In order to not saturate the sensor output, offset values should be within
±10,000 counts.
of the RAW bit which only controls the subtraction of the user defined hard iron offset.
4.3.4
on one or more axes. Software polling can be used to detect the transition of the ZYXDR bit from 0 to 1 but, since the ZYXDR bit
is also logically connected to the INT1 pin, a more efficient approach is to use INT1 to trigger a software interrupt when new
measurement data is available as follows:
4.3.5
9
Single/Burst Write Operation
Single/Burst Read Operation
MAG3110
IIC Start
IIC Start
See
When the Fast Read (FR) bit is set (CTRL_REG1, 0x10, bit 2), the MSB 8-bit data is read through the I
The 2’s complement user offset correction register values are used to compensate for correcting the X, Y , and Z-axis after
Depending on the setting of the RAW bit (CTRL_REG2, 0x11, bit 5) the magnetic field sample data is corrected with the user
The factory calibration for gain, offset and temperature compensation is always automatically applied irrespective of the setting
The DR_STATUS register (see section 5.1.1) contains the ZYXDR bit which denotes the presence of new measurement data
Set the TM bit in CTRL_REG1 when you want the part to acquire only 1 sample on each axis. See table below for details.
1. Enable automatic resets by setting AUTO_MRST_EN bit in CTRL_REG2 (CTRL_REG2 = 0b1XXXXXX).
2. Put MAG3110 in ACTIVE mode (CTRL_REG1 = 0bXXXXXX01).
3. Idle until INT1 goes HIGH and activates an interrupt service routine in the user software.
4. Read magnetometer data as required from registers 0x01 to 0x06. INT1 is cleared when register 0x01 OUT_X_MSB is
5. Return to idle in step 2.
read and this register must therefore always be read in the interrupt service routine.
Figure 6
IIC Slave ADDR
IIC Slave ADDR
(R/W bit = 0)
(R/W bit = 0)
Fast Read Mode
User Offset Corrections
INT1
Triggered Measurements
for details on how to perform read/write operations with MAG3110.
AC
0
0
1
1
MAG3110 Register Address to Start Write
MAG3110 Register Address to Start Read
TM
0
1
0
1
Figure 6. MAG3110 I
ASIC is in low power standby mode.
The ASIC shall exit standby mode, perform one measurement cycle based on
the programmed ODR and OSR setting, update the I
enter standby mode.
The ASIC shall perform continuous measurements based on the current OSR
and ODR settings.
The ASIC shall continue current measurement at fastest applicable ODR for
programmed OSR. The ASIC shall return to programmed ODR after completing
the triggered measurement.
2
C Generic Read/Write Operations
Data0*
IIC Repeated Start
Description
Data1
—
IIC Slave ADDR
(R/W bit = 1)
2
C data registers and re-
STOP
IIC
Data0*
Freescale Semiconductor
2
C bus. Auto-increment
Data1
—
Sensors
STOP
IIC