MHST02525 Lineage Power, MHST02525 Datasheet - Page 7
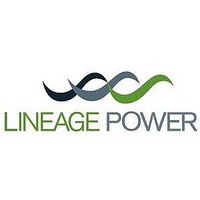
MHST02525
Manufacturer Part Number
MHST02525
Description
HEATSINK 1.48L X.225"H EXTRUSION
Manufacturer
Lineage Power
Datasheet
1.MHSL02525.pdf
(8 pages)
Specifications of MHST02525
Attachment Method
Bolt On
Outline
37.60mm x 36.80mm
Height
0.225" (5.715mm)
Lead Free Status / RoHS Status
Contains lead / RoHS non-compliant
Package Cooled
-
Power Dissipation @ Temperature Rise
-
Thermal Resistance @ Forced Air Flow
-
Thermal Resistance @ Natural
-
Technical Note
July 1996
Basic Thermal Model
Another approach for analyzing thermal performance is
to model the overall thermal resistance of the module.
This presentation method is especially useful when
considering heat sinks, since their performance is also
typically given as a resistance. Total module thermal
resistance ( ) is defined as the maximum case temper-
ature rise ( Tc,max) divided by the module power dis-
sipation (P
This can be represented as an equivalent circuit as
shown in Figure 10. In this model P
are analogous to current flow, voltage drop, and electri-
cal resistance, respectively, in Ohm's law. Also,
ambient temperature (T
perature (Tc) as defined in Figures 3 and 1 respec-
tively.
For FC- and FW-Series 250 W to 300 W BMPMs, the
module's thermal resistance values versus air velocity
have been determined experimentally and are plotted
in Figures 11 and 12 for a unit without a heat sink and
for the various heat sink configurations (see Figures 6
and 7). Note that the highest values on the curves rep-
resent natural convection. In a system with free-flowing
air and other heat sources, there may be additional air-
flow.
It is important to point out that the thermal resistances
shown in Figures 11 and 12 are for heat transfer from
the sides and bottom of the module as well as the top
side with the attached heat sink; therefore, the case-to-
ambient thermal resistances shown will generally be
lower than the resistance of the heat sink by itself. The
data in Figures 11 and 12 were taken with a thermally
conductive dry pad between the case and the heat sink
to minimize contact resistance (typically 0.1 °C/W to
0.3 °C/W).
Tyco Electronics Corp.
Tc,max is defined as the difference between the inlet
Tc,max = Tc – T
= Tc,max / P
Figure 10. Basic Thermal Resistance Module
BMPM
P
D
D
):
D
A
A
) and the module case tem-
D
, Tc,max, and
THERMAL
RESISTANCE
= BMPM
8-695
250 W—300 W Board-Mounted Power Modules
Thermal Management for FC- and FW-Series
Figure 11. Case-to-Ambient Thermal Resistance
Figure 12. Case-to-Ambient Thermal Resistance
4.5
4.0
3.5
3.0
2.5
2.0
1.5
1.0
0.5
0.0
4.5
4.0
3.5
3.0
2.5
2.0
1.5
1.0
0.5
0.0
0
0
Curves, Longitudinal Orientation
Curves; Transverse Orientation
100
100
AIR VELOCITY, (ft./min.)
200
AIR VELOCITY, (ft./min.)
200
300
300
1 1/2 in. HEAT SINK
1 in. HEAT SINK
1/2 in. HEAT SINK
1/4 in. HEAT SINK
NO HEAT SINK
1 1/2 in. HEAT SINK
1 in. HEAT SINK
1/2 in. HEAT SINK
1/4 in. HEAT SINK
NO HEAT SINK
400
400
500
500
8-1320
8-1321
600
600
7