ADP1864-BL-EVALZ Analog Devices Inc, ADP1864-BL-EVALZ Datasheet - Page 8
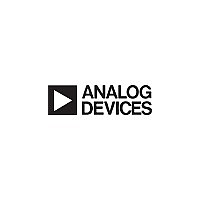
ADP1864-BL-EVALZ
Manufacturer Part Number
ADP1864-BL-EVALZ
Description
Blank Boards
Manufacturer
Analog Devices Inc
Specifications of ADP1864-BL-EVALZ
Main Purpose
DC/DC, Step Down
Regulator Topology
Buck
Board Type
Partially Populated - Main IC Only
Utilized Ic / Part
ADP1864
Lead Free Status / RoHS Status
Lead free / RoHS Compliant
Current - Output
-
Voltage - Output
-
Voltage - Input
-
Power - Output
-
Frequency - Switching
-
Outputs And Type
-
Lead Free Status / RoHS Status
Lead free / RoHS Compliant
EVAL-ADP1864
EXCEL DESIGN TOOL INTERFACE
ENTER PERFORMANCE SPECIFICATIONS
In this section, the user can provide the specifications on how
the power supply being designed needs to perform. The voltage
range for the first two pull-down menus (Vinmin and Vinmax)
is 3.15 V to 14 V. In the third pull-down menu, the user provides
the required regulated output voltage (Vout), which needs to be
less than Vinmin and Vinmax, because this tool is to be used
with the buck topology. The next pull-down menu is the required
output current (Ioutmax). It is wise to design for the peak current
the regulator needs to provide, even if the peak is required for
only a short period of time. Without taking this into considera-
tion, it is possible to hit the current limit when peak current is
needed. The information provided in the ambient temperature
(Tmax ambient) pull-down menu allows the estimated temper-
ature to be computed for each component. This is a required
piece of information to ensure that the parts selected are thermally
capable of handling the rise in temperature associated with
internal losses of the parts. The switching frequency is internally
set in the
specification, and the minimum and maximum limits can be
selected through the pull-down menu (Fsw). When the
switching frequency is at a minimum, the current in the
ADP1864
to 580 kHz. There is a tolerance on this
Figure 18. Excel Design Tool Interface
Rev. C | Page 8 of 16
inductor rises to a slightly higher amplitude than in the nominal
switching frequency case. Consequently, the voltage across the
sense resistor will also be higher, which needs to be accounted
for when the tool calculates the current limit trip point. A
robust design should always consider this minimum switching
frequency. Additionally, the performance of the system can be
viewed when selecting the maximum switching frequency from
the pull-down menu.
The inductor ripple selection (IripplemaxL) affects several
parameters. As a general guideline, it is recommended to set
this value between 30% to 50% of the output load. A small
inductor allows energy to be transferred from the input to the
output more quickly during a load step, resulting in a smaller
output voltage excursion during the load step. However, a small
inductor requires a higher current rating of the inductor itself,
that is, the ripple current is inversely proportional to the size of
the inductor. Higher ripple current also translates to higher
output voltage ripple for a fixed capacitance value. Selecting the
maximum output voltage ripple from the next pull-down menu
(Vripple ppk) determines the amount and type (MLCC, alumi-
num electrolytic, for example) of output capacitance needed and
correspondingly how the compensation components are sized.