ADIS16080ACCZ Analog Devices Inc, ADIS16080ACCZ Datasheet - Page 12
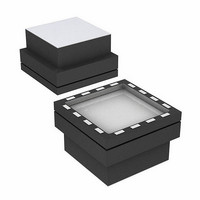
ADIS16080ACCZ
Manufacturer Part Number
ADIS16080ACCZ
Description
IC,Acceleration Detector,LGA,16PIN,PLASTIC
Manufacturer
Analog Devices Inc
Datasheet
1.ADIS16080PCBZ.pdf
(16 pages)
Specifications of ADIS16080ACCZ
Range °/s
±80°/s
Sensitivity
0.09766°/sec/LSB
Typical Bandwidth
40Hz
Voltage - Supply
4.75 V ~ 5.25 V
Current - Supply
7mA
Output Type
SPI
Operating Temperature
-40°C ~ 85°C
Package / Case
16-LGA
Lead Free Status / RoHS Status
Lead free / RoHS Compliant
For Use With
ADIS16080/PCBZ - BOARD EVALUATION FOR ADIS16080
Lead Free Status / RoHS Status
Lead free / RoHS Compliant
Available stocks
Company
Part Number
Manufacturer
Quantity
Price
Company:
Part Number:
ADIS16080ACCZ
Manufacturer:
PHILIPS
Quantity:
570
ADIS16080
BASIC OPERATION
The ADIS16080 is designed for simple integration into indus-
trial system designs, requiring only a 5.0 V power supply and a
four-wire, industry standard serial peripheral interface (SPI). The
SPI handles all digital I/O communication in the ADIS16080.
SERIAL PERIPHERAL INTERFACE (SPI)
The ADIS16080 SPI port includes four signals: chip select ( CS ),
serial clock (SCLK), data input (DIN), and data output
(DOUT). The CS line enables the ADIS16080 SPI port and
frames each SPI event. When this signal is high, the DOUT
lines are in a high impedance state and the signals on DIN and
SCLK have no impact on operation. A complete data frame
contains 16 clock cycles. Because the SPI port operates in full
duplex mode, it supports simultaneous, 16-bit receive (DIN) and
transmit (DOUT) functions within the same data frame.
Control Register
The DIN control register provides controls for two operational
settings: the output data source and the coding (twos comple-
ment vs. offset binary). Table 5 and Figure 22 provide the
proper bit definitions for control register configuration. The
DIN sequence starts with a 1 for configuration sequences and a
0 for read sequences. When this bit is 0, the remaining DIN bits
do not change the control register and the next sample’s output
data reflects the existing configuration. Data loads from
the DIN pin into the ADIS16080 on the falling edge of SCLK.
Once the 16-SCLK sequence is complete, the control register is
updated and ready for the next read sequence. If a data frame
has less than 16 SCLK cycles, the control register does not
update and maintains its previous configuration. The DIN bit
definitions in Table 5, which have either 0 or 1 assigned to
them, are critical for proper operation.
DOUT
SCLK
DOUT
SCLK
DIN
CS
DIN
CS
WRITE
0
1
CONFIGURATION COMMAND FOR NEXT OUTPUT SEQUENCE
0
ADC PLACED IN HOLD MODE
0
DATA OUTPUT, BASED ON PREVIOUS CONFIGURATION
2
ADD1
D/C
DATA FRAME
3
ADD0
D/C
4
Figure 22. SPI Sequence, Clock Polarity = 1, Clock Phase = 0
D11
ADD1
Figure 21. Configuration and Read Sequence
5
D10
ADD0
6
D9
Rev. | Page 12 of 16
1
7
D8
1
8
D7
D/C
ADC Conversion
The chip select ( CS ) and serial clock (SCLK) lines control the
on-board A/D conversion process. When the chip select line
goes low, the DOUT line comes out of three-state mode, the
track-and-hold goes into hold mode, and the ADC samples the
analog input at this point. The track-and-hold returns to track
mode on the 14
drives the internal ADC conversion clock, using its falling edge
for control of this process. All 16 SCLK cycles are required for a
complete conversion. If a data frame has less than 16 SCLK
cycles, the conversion cannot complete and does not update the
output data for the next data frame cycle.
Output Data Access
The DOUT sequence starts with two zeros, one that clocks out
after the falling edge of CS , and a second one that clocks out on
the first SCLK falling edge. The next 14 bits, ADD0, ADD1 and
the 12 data bits, clock out on SCLK falling edges. After the 16
falling edge, the DOUT line moves to a three-state mode.
When setting up the system process to receive data from the
ADIS16080, use a clock phase setting of 0 and a clock polarity
setting of 1. These settings reflect the timing displayed in
Figure 22. To maintain proper communication at the maximum
specified clock rates, the system processor must be able to
support the setup time requirement, listed in Figure 2 and
Table 2 (t
ADC PLACED IN TRACK MODE
9
D6
D/C
10
9
).
NEXT COMMAND, IF NECESSARY
D5
0
11
th
D4
CODE
DATA FRAME
falling edge of the SCLK line. The serial clock
12
D3
D/C
13
D2
D/C
14
D1
D/C
15
D0
D/C
16
th