HFBR-0537 Avago Technologies US Inc., HFBR-0537 Datasheet - Page 10
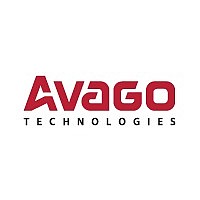
HFBR-0537
Manufacturer Part Number
HFBR-0537
Description
Fiber Optics, Evaluation Kit
Manufacturer
Avago Technologies US Inc.
Specifications of HFBR-0537
Tool / Board Applications
Fiber Optic Transceivers
Mcu Supported Families
HFBR-1527, HFBR-2526
Development Tool Type
Hardware / Software - Eval/Demo Board
Main Purpose
Interface, Fiber Optics
Embedded
No
Utilized Ic / Part
HFBR-1527, HFBR-2526
Primary Attributes
DC ~ 32MBd TTL
Secondary Attributes
TTL-Compatible
Lead Free Status / RoHS Status
Lead free / RoHS Compliant
Lead Free Status / RoHS Status
Lead free / RoHS Compliant, Lead free / RoHS Compliant
Other names
516-2146
HFBR-0537
HFBR-0537
Error Rates and Noise Immunity
The probability that a fiberoptic link will make an error
is related to the receiver’s own internal random noise
and its ability to reject noise originating from the sys-
tem in which it is installed. The total noise present in
any fiberoptic receiver is normally the sum of the PIN
diode preamplifier’s noise and the host system’s elec-
trical noise. The amount of hysteresis applied to the
comparator determines the minimum signal amplitude
(also known as minimum signal threshold level) at
which the receiver can reliably detect data. The ratio
between the comparator’s switching threshold (also
known as hysteresis) and the receiver’s noise also has a
dramatic impact on probability of error. Small increases
in the comparator’s threshold-to-noise ratio result in a
very sharp reduction in the probability of error. Figure 8
shows that the receiver’s probability of error is reduced
by six orders of magnitude from (1x10-9 to 1x10-15)
when the receiver’s threshold-tonoise ratio improves
from 12:1 to 15.8:1. At any fixed temperature the total
value of the receiver’s random noise plus the host sys-
tem’s noise can be assumed to be a constant. So the
most obvious way to reduce the probability of error is
to increase the comparator’s hysteresis and increase the
amplitude of the optical signal applied to the receiver. A
less obvious but better technique for lowering the error
rate is to improve the receiver’s ability to reject electrical
noise from the system in which it resides. The fiberoptic
receivers recommended in this application note have
sufficient noise immunity to be used in most systems
without electrostatic shielding. The Avago Technologies
PIN diode pre-amps, which are used in the receiver’s
first stage, are small hybrid circuits, and these small
hybrid components do not function as particularly
effective antennas. For extremely noisy applications,
Avago Technologies offers PIN diode pre-amps in elec-
trically conductive plastic or all metal packages. Avago
Technologies manufactures a wide range of conductive
and non-conductive fiberoptic components that mate
with various industry-standard fiberoptic connectors.
However, the overwhelming majority of the fiberoptic
applications successfully implemented with Avago
Technologies’ fiberoptic components have not required
conductive plastic or metal receiver housings. The most
insidious and the most overlooked source of noise is
10
usually the host system’s +5 V power supply. The host
system’s +5 volt supply normally powers the fiberoptic
receiver, the fiberoptic transmitter and an entire system
comprised of relatively noisy digital circuits. The simple
and inexpensive power supply filters recommended
in this publication have been proven to work in a wide
range of system applications. The power-supply filters
recommended in this application note are normally suf-
ficient to protect the fiberoptic receiver from very noisy
host systems, but in extremely noisy applications addi-
tional power supply filtering could be needed.
Parts List
The TTL-compatible fiberoptic transceivers recommend-
ed in this publication are very simple and inexpensive,
so only a few external components are needed. Com-
plete parts lists for the circuits recommended in this ap-
plication note are provided in Table 5 and Table 6. The
parts listed in Table 5 are for the transmitter in Figure
3 and the receiver in Figure 4. The parts listed in Table
6 are for the transmitter in Figure 3 and the receiver in
Figure 5. All of the components described in the part
lists are compatible with the printed circuit artworks
shown in Figure 6 and Figure 7, thus minimizing the
design time and resources needed to use the low cost
fiberoptic transceivers shown in the application note.
Figure 8. Receiver Threshold-to-Noise Ratio vs. Probability of Error
(aka BER)
16
14
12
10
1E-3
8
6
1E-5
BIT-ERROR RATIO - (BER)
1E-7
1E-9
1E-11
1E-13
1E-15