HLMP-HB55-JKCDD Avago Technologies US Inc., HLMP-HB55-JKCDD Datasheet - Page 9
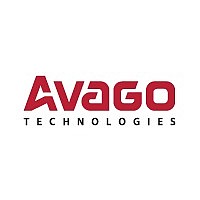
HLMP-HB55-JKCDD
Manufacturer Part Number
HLMP-HB55-JKCDD
Description
LED Lamp
Manufacturer
Avago Technologies US Inc.
Datasheet
1.HLMP-HM55-MQ000.pdf
(12 pages)
Specifications of HLMP-HB55-JKCDD
Bulb Size
T-1 3/4 (5mm)
Led Color
Blue
Luminous Intensity
400mcd
Viewing Angle
100°
Forward Current If
20mA
Forward Voltage
3.2V
Led Mounting
Through Hole
Lens Shape
Oval
Wavelength Typ
470nm
Lead Spacing
2.54mm
Color
Blue
Millicandela Rating
320mcd
Current - Test
20mA
Wavelength - Dominant
470nm
Wavelength - Peak
467nm
Voltage - Forward (vf) Typ
3.2V
Lens Type
Clear, Blue Tinted
Lens Style/size
Oval, 5mm
Package / Case
Radial - 2 Lead
Height
7.00mm
Mounting Type
Through Hole
Resistance Tolerance
470nm
Lead Free Status / RoHS Status
Lead free / RoHS Compliant
Luminous Flux @ Current - Test
-
Lead Free Status / RoHS Status
Lead free / RoHS Compliant, Lead free / RoHS Compliant
Available stocks
Company
Part Number
Manufacturer
Quantity
Price
Company:
Part Number:
HLMP-HB55-JKCDD
Manufacturer:
AVAGO
Quantity:
40 000
9
Relative Light Output vs. Junction Temperature
Precautions:
Lead Forming
• The leads of an LED lamp may be preformed or cut to
• If lead forming is required before soldering, care must
• For better control, it is recommended to use proper
Soldering Conditions
• Care must be taken during PCB assembly and soldering
• The closest LED is allowed to solder on board is 1.59 mm
• Recommended soldering conditions:
length prior to insertion and soldering into PC board.
be taken to avoid any excessive mechanical stress
induced to LED package. Otherwise, cut the leads of
LED to length after soldering process at room
temperature. The solder joint formed will absorb the
mechanical stress of the lead cutting from traveling to
the LED chip die attach and wirebond.
tool to precisely form and cut the leads to applicable
length rather than doing it manually.
process to prevent damage to LED component.
below the body (encapsulant epoxy) for those parts
without standoff.
Pre-heat Temperature
Pre-heat Time
Peak Temperature
Dwell Time
1.2
1.0
0.8
0.6
0.4
0.2
0
-40
-20
Wave Soldering
105 C Max.
30 sec Max.
250 C Max.
3 sec Max.
T
J
– JUNCTION TEMPERATURE – C
0
20
Manual Solder
Dipping
–
–
260 C Max.
5 sec Max.
40
GREEN
60
• Wave soldering parameter must be set and maintained
Notes:
1. PCB with different size and design (component density)
2. Avago Technologies' high brightness LED are using high
according to recommended temperature and dwell
time in the solder wave. Customer is advised to
periodically check on the soldering profile to ensure the
soldering profile used is always conforming to
recommended soldering condition.
BLUE
will have different heat mass (heat capacity). This might
cause a change in temperature experienced by the board if
same wave soldering setting is used. So, it is recommended
to recalibrate the soldering profile again before loading a
new type of PCB.
efficiency LED die with single wire bond as shown below.
Customer is advised to take extra precaution during wave
soldering to ensure that the maximum wave temperature
is not exceeding 250 C. Overstressing the LED during
soldering process might cause premature failure to the LED
due to delamination.
80