QSH4218-51-10-049 TRINAMIC, QSH4218-51-10-049 Datasheet
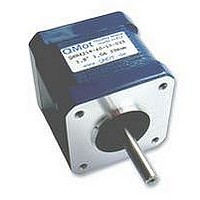
QSH4218-51-10-049
Specifications of QSH4218-51-10-049
Related parts for QSH4218-51-10-049
QSH4218-51-10-049 Summary of contents
Page 1
... QMot QSH4218 family Manual V1.05 2009-JUN-20 Trinamic Motion Control GmbH & Co. KG Sternstraß – 20357 Hamburg, Germany http://www.trinamic.com ...
Page 2
... Figure 4.1: Lead wire configuration ................................................................................................................................ 6 Figure 4.2: Dimensions (all values in mm) ................................................................................................................... 6 Figure 5.1: QSH4218-35-10-027 speed vs. torque characteristics ............................................................................. 7 Figure 5.2: QSH4218-41-10-035 speed vs. torque characteristics ............................................................................. 7 Figure 5.3: QSH4218-51-10-049 speed vs. torque characteristics ............................................................................. 8 Figure 5.4: QSH4218-47-28-040 speed vs. torque characteristics ............................................................................. 8 List of Tables Table 2.1: Motor technical data ......................................................................................................................................... 4 Table 4 ...
Page 3
... QSH4218 Manual (V1.05/2009-JUN-20) 1 Life support policy TRINAMIC Motion Control GmbH & Co. KG does not authorize or warrant any of its products for use in life support systems, without the specific written consent of TRINAMIC Motion Control GmbH & Co. KG. Life support systems are equipment intended to ...
Page 4
... These two phase hybrid stepper motors are optimized for microstepping and give a good fit to the TRINAMIC family of motor controllers and drivers. They are all used in the 42mm PANdrive™ family. The QSH4218-35-10-027, QSH4218-41-10-035 and QSH4218-51-10-049 are motors with 1A RMS coil current. The QSH4218-47-28-40 is different designed for 2.8A RMS coil current to provide maximum torque at high velocities ...
Page 5
... Order codes Description Order code QSH4218-35-10-027 QMot stepper motor 42mm, 1A, 0.27Nm QSH4218-41-10-035 QMot stepper motor 42mm, 1A, 0.35Nm QSH4218-51-10-049 QMot stepper motor 42mm, 1A, 0.49Nm QSH4218-47-28-040 QMot stepper motor 42mm, 2.8A, 0.40Nm Related products PDx-110-42 (-option) PANdrive™ with QSH42-18 motor and interface option PDx-013-42 PANdrive™ ...
Page 6
... Dimensions 24±1 20 4.5 22-0. Motor Length QSH4218-35-10-027 33.5mm QSH4218-41-10-035 38mm QSH4218-51-10-049 47mm QSH4218-47-28-040 47mm Figure 4.2: Dimensions (all values in mm) Copyright © 2008, TRINAMIC Motion Control GmbH & Co. KG black A green Figure 4.1: Lead wire configuration Length±1 5 42.3 4xM3 Deep 4 ...
Page 7
... Testing conditions: driver supply voltage +24V DC, coil current 1.0A RMS, half step operation Figure 5.1: QSH4218-35-10-027 speed vs. torque characteristics 5.2 Motor QSH4218-41-10-035 Testing conditions: driver supply voltage +24V DC, coil current 1.0A RMS, half step operation Figure 5.2: QSH4218-41-10-035 speed vs. torque characteristics Copyright © 2008, TRINAMIC Motion Control GmbH & Co ...
Page 8
... QSH4218 Manual (V1.05/2009-JUN-20) 5.3 Motor QSH4218-51-10-049 Testing conditions: driver supply voltage +24V DC, coil current 1.0A RMS, half step operation Figure 5.3: QSH4218-51-10-049 speed vs. torque characteristics 5.4 Motor QSH4218-47-28-040 Testing conditions: driver supply voltage: +24V DC, coil current: 2.8A RMS, half step operation Figure 5.4: QSH4218-47-28-040 speed vs. torque characteristics Copyright © ...
Page 9
... QSH4218 Manual (V1.05/2009-JUN-20) 6 Considerations for operation The following chapters try to help you to correctly set the key operation parameters in order to get a stable system. 6.1 Choosing the best fitting motor for an application For an optimum solution it is important to fit the motor to the application and to choose the best mode of operation ...
Page 10
... QSH4218 Manual (V1.05/2009-JUN-20) 6.2.1 Choosing the optimum current setting Generally, you choose the motor in order to give the desired performance at nominal current. For short time operation, you might want to increase the motor current to get a higher torque than specified for the motor hot environment, you might want to work with a reduced motor current in order to reduce motor self heating ...
Page 11
... QSH4218 Manual (V1.05/2009-JUN-20) 6.3.1 Determining if the given driver voltage is sufficient Try to brake the motor and listen different velocities. Does the sound of the motor get raucous or harsh when exceeding some velocity? Then the motor gets into a resonance area. The reason is that the motor back-EMF voltage reaches the supply voltage. Thus, the driver cannot bring the full current into the motor any more ...
Page 12
... QSH4218 Manual (V1.05/2009-JUN-20) 6.5 Choosing the Commutation Scheme While the motor performance curves are depicted for fullstepping and halfstepping, most modern drivers provide a microstepping scheme. Microstepping uses a discrete sine and a cosine wave to drive both coils of the motor, and gives a very smooth motor behavior as well as an increased position resolution ...
Page 13
... Chapter Fehler! Verweisquelle konnte nicht gefunden werden. optimum motor settings added Chapter 0: motor codes corrected Chapter 6.4 Back EMF (BEMF) added Max. operating voltage added QSH4218-47-28-040 and order codes added, dimensions and torque figures reconditioned, further minor changes Table 7.1: Document revision 13 ...