AS5035-T austriamicrosystems, AS5035-T Datasheet - Page 8
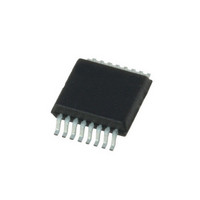
AS5035-T
Manufacturer Part Number
AS5035-T
Description
IC ENCODER ROTARY 8-BIT 16-SSOP
Manufacturer
austriamicrosystems
Type
Linear, Rotary Encoder - Programmabler
Datasheet
1.AS5035-T.pdf
(17 pages)
Specifications of AS5035-T
Sensing Range
45mT ~ 75mT
Voltage - Supply
3 V ~ 3.6 V, 4.5 V ~ 5.5 V
Current - Supply
25mA
Current - Output (max)
4mA
Output Type
Quadrature with Index (Incremental)
Features
Programmable
Operating Temperature
-40°C ~ 125°C
Package / Case
16-SSOP
Lead Free Status / RoHS Status
Lead free / RoHS Compliant
Other names
AS5035-TTR
AS5035 – 64 PPR INCREMENTAL MAGNETIC ROTARY ENCODER
The magnet’s field strength perpendicular to the die
surface should be verified using a gauss-meter. The
magnetic field B
circle with a radius of 1.1mm (R1), should be in the range
of ±45mT…±75mT. (see Figure 10).
9.1
The best linearity can be achieved by placing the center
of the magnet exactly over the defined center of the IC
package as shown in Figure 11:
Magnet Placement:
The magnet’s center axis should be aligned within a
displacement radius R
center of the IC with reference to the edge of pin #1 (see
Figure 11). This radius includes the placement tolerance
of the chip within the SSOP-16 package (+/- 0.235mm).
The displacement radius R
the center of the chip
The vertical distance should be chosen such that the
magnetic field on the die surface is within the specified
limits (see Figure 10). The typical distance “z” between
the magnet and the package surface is 0.5mm to 1.8mm
with the recommended magnet (6mm x 3mm). Larger
gaps are possible, as long as the required magnetic field
strength stays within the defined limits.
A magnetic field outside the specified range may still
produce usable results, but the out-of-range condition
will be indicated by MagINCn (pin 1) and MagDECn (pin
2), see 5.5.
Revision 1.5
2.433 mm
2.433 mm
Figure 11: Defined IC center and magnet displacement radius
Physical Placement of the Magnet
v
1
at a given distance, along a concentric
Area of recommended maximum
magnet misalignment
3.9 mm
d
of 0.25mm from the defined
d
is 0.485mm with reference to
R
d
Defined
center
3.9 mm
www.austriamicrosystems.com
10 Angular Output Tolerances
10.1 Accuracy
Accuracy is defined as the error between measured
angle and actual angle. It is influenced by several
factors:
As a sum of all these errors, the accuracy with centered
magnet = (Err
± 0.5 degrees @ 25°C (see Figure 14).
Misalignment
accuracy. Figure 14 shows an example of a 3D-graph
displaying non-linearity over XY-misalignment. The
center of the square XY-area corresponds to a centered
magnet (see dot in the center of the graph). The X- and
Y- axis extends to a misalignment of ± 1mm in both
directions. The total misalignment area of the graph
covers a square of 2x2 mm (79x79mil) with a step size of
100µm.
Die surface
Figure 13: Example of linearity error over XY misalignment
6
°
the non-linearity of the analog-digital converters,
internal gain and mismatch errors,
non-linearity due to misalignment of the magnet
5
4
3
2
1
0
N
Figure 12: Vertical placement of the magnet
max
Package surface
of the magnet further reduces the
– Err
y
S
min
)/2 is specified as better than
z
1.282mm ± 0.15mm
0.576mm ± 0.1mm
-1000
-700
-400
-100
200
500
x
800
Page 8 of 17