ATS617LSGTN-T Allegro Microsystems Inc, ATS617LSGTN-T Datasheet - Page 12
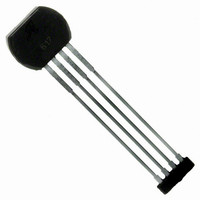
ATS617LSGTN-T
Manufacturer Part Number
ATS617LSGTN-T
Description
IC HALL EFFECT GEAR SENSOR 4SIP
Manufacturer
Allegro Microsystems Inc
Type
Special Purposer
Datasheet
1.ATS617LSGTN-T.pdf
(16 pages)
Specifications of ATS617LSGTN-T
Package / Case
4-SIP
Sensing Range
60G
Voltage - Supply
4.5 V ~ 24 V
Current - Supply
12mA
Current - Output (max)
55mA
Output Type
Digital, Open Collector
Features
Gear Tooth Type
Operating Temperature
-40°C ~ 150°C
Output Current
45mA
Bandwidth
15kHz
Supply Voltage Max
24V
Hall Effect Type
Gear Tooth
Operating Temperature Range
-40°C To +150°C
Supply Voltage Min
4.5V
Lead Free Status / RoHS Status
Lead free / RoHS Compliant
Other names
620-1326-2
Available stocks
Company
Part Number
Manufacturer
Quantity
Price
ATS617LSG
Superior Performance The ATS617 peak-detecting differen-
tial design has several advantages over conventional Hall-effect
gear-tooth sensors. The signal-processing techniques used in the
ATS617 solve the catastrophic issues that affect the functionality
of conventional digital gear-tooth sensors, such as the following:
• Temperature drift. Changes in temperature do not greatly affect
• Timing accuracy variation due to air gap. The accuracy varia-
• Dual edge detection. Because this device switches based on the
• Tilted or off-center installation. Traditional differential sensors
• Large operating air gaps. Large operating air gaps are achiev-
• Immunity to magnetic overshoot. The patented adjustable
• Response to surface defects in the target. The gain-adjust
• Immunity to vibration and backlash. The gain-adjust circuitry
• Immunity to gear run out. The differential chip configuration
Differential vs. Single-Element Design The differential
chip is superior in most applications to the classical single-ele-
ment design. The single-element configuration commonly used
(Hall-effect element mounted on the face of a simple permanent
magnet) requires the detection of a small signal (often <100 G)
that is superimposed on a large back-biased field, often 1500 G to
3500 G. For most gear/target configurations, the back-biased field
this device due to the stable amplifier design and the offset
rejection circuitry.
tion caused by air gap changes is minimized by the self-calibra-
tion circuitry. A 2×-to-3× improvement can be seen.
positive and negative peaks of the signal, dual edge detection is
guaranteed.
can switch incorrectly due to baseline changes versus air gap
caused by tilted or off-center installation. The peak detector cir-
cuitry references the switchpoint from the peak and is immune
to this failure mode. There may be a timing accuracy shift
caused by this condition.
able with this device due to the sensitive switchpoints after
power-on (dependent on target dimensions, material, and
speed).
hysteresis circuit makes the ATS617 immune to switching on
magnetic overshoot within the specified air gap range.
circuitry reduces the effect of minor gear anomalies that would
normally cause false switching.
keeps the hysteresis of the device roughly proportional to the
peak-to-peak signal. This allows the device to have good im-
munity to vibration even when operating at close air gaps.
eliminates the baseline variations caused by gear run out
Dynamic, Self-Calibrating, Peak-Detecting, Differential
values change due to concentration effects, resulting in a varying
baseline with air gap, valley widths, eccentricities, and vibration
(figure 4). The differential configuration (figure 5) cancels the
effects of the back-biased field and avoids many of the issues
presented by the single Hall element design.
Figure 4. Affect of varying valley widths on single-element circuits.
Figure 5. Affect of varying air gaps on differential circuits.
Hall Effect Gear Tooth Sensor IC
115 Northeast Cutoff
1.508.853.5000; www.allegromicro.com
Allegro MicroSystems, Inc.
Worcester, Massachusetts 01615-0036 U.S.A.
12